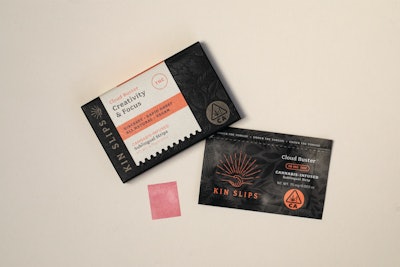
That transition took place recently at San Francisco-based Kin Slips. Now operating at the firm is a semi-automated pouch packaging system that lets one or two operators perform the tasks for which several were required in the recent past. Says CEO Josh Kirby, “We’re very glad that’s over with.
The rotary system for filling and sealing premade pouches that Kin State fills was installed in the summer of 2019. Before exploring how it works, it’s important to point out that the product being packaged is a sublingual strip. As for the premade pouch that serves as the primary package, it comes from Fortis Solutions Group. The pouch is a three-side-sealed pouch made from a three-layer lamination consisting of reverse-printed matte polypropylene/metallized polyester/polyethylene. These pouches arrive in 2,500-count corrugated cases. An operator puts the pouches into four magazines in a Pouchmaster ABS system supplied by About Packaging Robotics Inc. A vacuum cup picker picks pouches four pouches at a time from the four magazines and rotates to the station at which two operators sit. The operators put a slip into each pouch and then one of them hits a foot pedal to advance the four pouches to a station where the ambient air is pressed out and a heat-seal bar seals the pouches closed. Then the pouches drop into a bin. All that’s left is for the operator to place the pouches into the secondary packaging, which Kirby refers to as a “wallet.” The wallet is closed and then a pressure-sensitive paper label is applied. Applied to the bottom is a second pressure-sensitive label that has all of the specific batch information that is required.