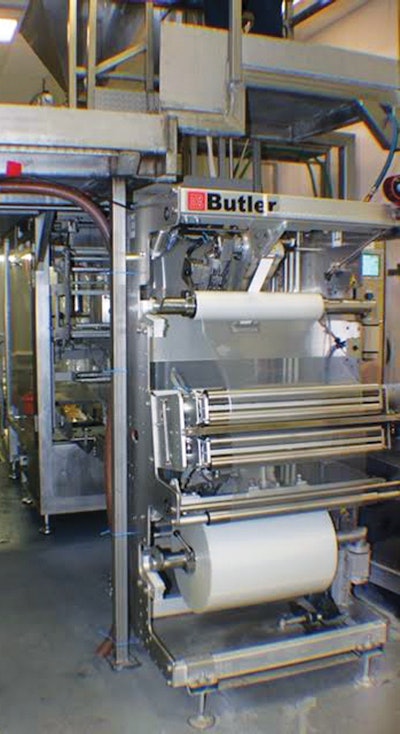
JTM Group, headquartered in Harrison, OH, is a family-owned international, multi-segmented food processing company that produces and markets an expansive range of fully cooked and frozen products (about 700 in all). The diverse line includes hamburgers, meatballs, pork sausages, buns in various sizes/shapes, macaroni and cheese, taco fillings, and JTM’s newest product, beer cheese, just to name a few. About 65% of the company’s products are sold to school lunch cafeterias, 20% to restaurants, 10% to military, and 5% to retail groceries.
Many of these products are packaged using vertical form/fill/seal machinery from Prodo-Pak Corp. and Matrix Packaging Machinery, LLC. Specific film structures, gauges, and suppliers are considered proprietary by JTM. Company VP Joe Maas notes that JTM had been experiencing significant packaging line downtime, due to the need to stop and change film rolls on the vf/f/s equipment. Maas estimates that it was taking about 15 minutes for each packaging roll changeover and splice to the next roll, which adds up to a considerable amount of downtime during the course of each day.
Then, on a visit to PACK EXPO 2013, Maas discovered a possible solution to the film changeover and splice downtime problem. He and his team ran across a new fast and efficient splicing system that can be easily retrofitted to existing vf/f/s equipment. The automated splicing equipment, manufactured by Butler Automatic, is specially designed to eliminate film roll changeover downtime. Its automatic web splicing technology joins two film rolls together, maintaining registration, without stopping the packaging line. When the running roll expires, the machine fires a splice, joining the beginning of the new roll to the end of the expiring roll. After the splice is completed, the film roll accumulator is refilled, and the expired roll is removed with zero downtime.