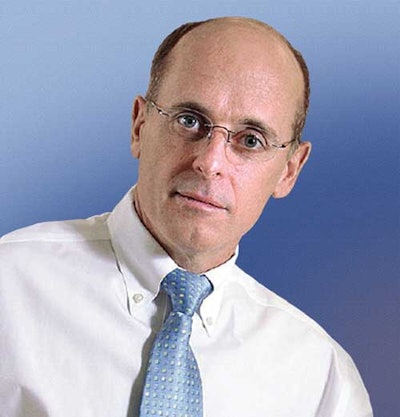
Hyaluron is a contract manufacturer and provider of process scale-up development and aseptic filling services. Its cGMP manufacturing facility/headquarters in Burlington, MA, includes three aseptic filling lines with syringe, vial, and custom container filling capabilities. In this question-and-answer interview, company president Shawn Kinney discusses prefilled syringe developments.
HCP: Explain a bit more about Hyaluron:
Kinney: We take active drug substances and formulate them into a solution. Then we sterilize them and put them into syringes and vials before delivering them back to our clients. These are generally materials that are being used in clinical studies for the investigation of the efficacy and safety of new drugs. They include both liquid and lyophilized products.
HCP: Tell us about the three filling lines:
Kinney: Optima manufactures machinery for various aspects of packaging and filling in the pharmaceutical industry. We work closely with Optima's Inova division that makes equipment that fills liquid into vials and syringes in a sterile environment and maintains the sterility of the product and containers. We have two of their syringe fillers and one of their vial fillers.
The vials and syringes are primarily made of glass, but we use some plastic materials. These are typically COCs (cyclic olefin copolymers). We use a variety of suppliers, including Gerresheimer, Schott, Becton, Dickinson and Co., and OMPI.
HCP: Please describe the filling process:
Kinney: Filling is semi-automated. The syringes come in a nested tub. There is a DuPont Tyvek lid that seals the sterile, ready-to-use syringes inside the tub. They have several layers of wrapping on the outside. We unwrap them and place them into the sterile environment where an operator will then pull off the Tyvek lid. Then the machines will pick up the tray that's inside holding all of the syringes in a precise configuration.
They will set that into a tray or a table on the filling machine, which then moves the syringes under the filling needles for automatic filling and placement of a stopper. The nest of syringes will be picked up and placed back in the tray or tub before exiting the machine. It's an entirely aseptic process, and the operators are gowned, qualified, and trained. All three filling lines are in a shrouded, Class 100 clean room environment.
HCP: Describe the key issues and trends that you see with regard to prefilled syringes.
Kinney: In this industry, prefilled syringes started appearing in the late 1970s. Before that, vials were primarily used. Some of the things that drove prefilled syringes were products that could not be placed or administered from a vial. Some viscous products that are gel-like don't lend themselves well to vials because when you are removing a liquid from a vial, you just put a needle on the syringe, pick it through the stopper and then pull back on the syringe. Then the liquid would flow out of the vial into the syringe. But very viscous products won't flow. A prefilled syringe allows a person to inject the total amount of drug directly into the patient. You can also increase the precision of dosing by using a prefilled syringe. You are not dependent upon a technician, an operator, or a pharmacist to pull the correct amount of liquid out of the vial into the syringe.
HCP: Where are syringes most frequently used?
Kinney: In a doctor's office, hospital, and now more often in the home healthcare market as well. The industry is moving in that direction, where prefilled syringes are becoming more in demand. One example would be for a patient with rheumatoid arthritis trying to manipulate a little vial and pull liquid out into a syringe and then make an injection, and having to change the needle on the syringe. But if you can give them the drug product already in a syringe, in the correct dose, with a needle attached, they can very easily make the injection.
HCP: What are some of the other issues that you see?
Kinney: Technologies are changing in terms of the manufacturing of the drug product, the processes, the filling and stoppering, putting the liquid into the syringe and then placing the stopper on it. The older technology for placing the stopper in a syringe after it was filled was to take the stopper, squeeze it inside a tube, which could fit down inside the syringe and with a rod, push the stopper out of that tube. That left a very large air bubble in the syringe.
The negative to that is when you have an air bubble in a syringe, and you expose that syringe to reduce the atmospheric pressure, as it happens in transport by airplanes, the air trapped inside the syringe expands and the stopper moves. The stopper can move back to a nonsterile part of the syringe. When you return back to ambient atmosphere, the stopper returns back to its original position and can potentially pull contaminated bacteria or a contaminant into the drug product.
HCP: To avoid that, what's being done?
Kinney: There are new processes called vacuum stoppering where a vacuum is pulled on the syringe. The stopper is then placed inside the syringe under vacuum. After the stopper is placed, the vacuum is released. Using that type of a process, one can decrease the bubble size, the headspace in the syringe down to nearly zero. That is the process we are using on the two Optima syringe lines. Vials always have a headspace left in them, but with a vial, the stopper is sealed and held in place by a crimp cap. So even though they are exposed to reduced atmospheric pressure, the stopper can't move.
HCP: On the two syringe lines using this technology, is that a separate unit that's attached to the Optima machinery?
Kinney: On our older filling machines, that was correct. It's an additional piece of machinery that sits next to the Optima machinery and after the syringes are filled, we have to place the syringes in this other machine from Becton Dickinson.
HCP: Any other technologies Hyaluron is now employing for prefilled syringes?
Kinney: Another technology that we are getting into is lyophilizing drug products in a prefilled syringe. There is only one company in the world right now that I am aware of that offers that as a service to other companies. It's a German company called Vetter Pharma Solutions.
Drug products have always been lyophilized in vials. The person administering the drug would have to add a diluent to the vial, shake up the product, dissolve it, and pull it back into a syringe and make the injection. That is a lot of manipulation, with considerable sources for potential errors. They can add too much or too little diluent. After the drug is dissolved, they can move too much liquid or too little liquid for injection into the patient.
If you can put your drug substance directly in the device from which the injection is going to be made, you can ensure that the correct amount of drug substance is injected into the patient, regardless of whether it was reconstituted with a little too much or too little diluent.
HCP: So, is Hyaluron lyophilizing in a prefilled syringe?
Kinney: Yes, we are doing that. We had to get some custom equipment built and made. It's not proprietary equipment. We made it ourselves from a local company that fabricated the devices. We fill the liquid into the syringes just as we normally would, as if we are going to fill just the liquid and not lyophilize it. They are placed into the lyophilizer. We had to build some special holders to hold the tubs and syringes in there. Then we had to design some special devices to hold the sterile stopper immediately above the syringe.
And, we had to create an insertion device because when something goes into lyophilization, it's frozen before a vacuum is pulled to sublimate off all the liquid and lyophilize the product. At the end of the cycle, you place the stopper inside the syringe.
In the early feasibility work we did, we would take the syringes out of the lyophilizer and in our clean room we would place the stoppers inside using the off-line stoppering method. However, this exposed the lyophilized product to ambient atmosphere inside, which has humidity. Generally, with lyophilized products, you want to keep them away from humidity. You are removing water from them because they are not stable in the presence of water. Some of them are very sensitive to humidity. So we needed to find a way to place the stopper inside the syringe while it was still inside the lyophilizer in a dry environment. We designed a means to do that.
Normally when you lyophilize a vial in a vial chamber, you have a stopper that is not pushed down all the way into the vial during the lyophilization process. At the end of the process, the shelves collapse. When they collapse, they push the stoppers down inside the vial to seal it. The vials sit on the shelves, on the floor of the cabinet, if you will. The shelves also have refrigerant flowing through them. That's what helps freeze the product that's placed inside. But at the completion of the cycle, the shelves collapse down on top of one another to push the stopper inside the vial before they are removed.
There are no stoppers made for syringes, so we had to find a means to suspend the stopper immediately above the syringe. We had to design special trays to do that. At the conclusion of the lyophilization cycle we modified our equipment to hold vacuum in the chamber at the completion of the cycle. We push the stopper down inside the syringe while it's still under vacuum. Once the stoppers are in the syringe, we release the vacuum. What you have is a syringe that has a vacuum inside it and as the air rushes in and the syringes are sealed, the air pressure pushes the stopper down inside the syringe.
We can control the height of movement of the stopper. In some cases, we want the stopper to move down so it's immediately next to the lyophilized product in the syringe. In other cases, we maintain some head space in there and control the depth at which the stopper will move in.
HCP: What different syringe sizes do you fill?
Kinney: We have used syringes that range between what is known as 1-mL long through a 10-mL size.
HCP: Does Hyaluron formulate its own products, or products for customers?
Kinney: We receive powders or solids from pharmaceutical and biotech companies. Some of them have their capability to make their own APIs (Active Pharmaceutical Ingredients), and others will outsource the manufacturing of the API to a contract manufacturer. They use us for filling and packaging. Then we ship them back to our clients.
HCP: Tell us about reconstituting the products for lyophilization in prefilled syringes.
Kinney: There are a couple of methods by which you can do that. You can put a needle on the end of the syringe and pull the liquid back into the syringe and reconstitute that way. There are a couple of companies that make reconstitution devices for products that are lyophilized: West and Duoject. Duoject's product is unique in that it allows you to add the liquid to the syringe through the stopper, rather than through the tip.
HCP: Explain a bit more about Hyaluron:
Kinney: We take active drug substances and formulate them into a solution. Then we sterilize them and put them into syringes and vials before delivering them back to our clients. These are generally materials that are being used in clinical studies for the investigation of the efficacy and safety of new drugs. They include both liquid and lyophilized products.
HCP: Tell us about the three filling lines:
Kinney: Optima manufactures machinery for various aspects of packaging and filling in the pharmaceutical industry. We work closely with Optima's Inova division that makes equipment that fills liquid into vials and syringes in a sterile environment and maintains the sterility of the product and containers. We have two of their syringe fillers and one of their vial fillers.
The vials and syringes are primarily made of glass, but we use some plastic materials. These are typically COCs (cyclic olefin copolymers). We use a variety of suppliers, including Gerresheimer, Schott, Becton, Dickinson and Co., and OMPI.
HCP: Please describe the filling process:
Kinney: Filling is semi-automated. The syringes come in a nested tub. There is a DuPont Tyvek lid that seals the sterile, ready-to-use syringes inside the tub. They have several layers of wrapping on the outside. We unwrap them and place them into the sterile environment where an operator will then pull off the Tyvek lid. Then the machines will pick up the tray that's inside holding all of the syringes in a precise configuration.
They will set that into a tray or a table on the filling machine, which then moves the syringes under the filling needles for automatic filling and placement of a stopper. The nest of syringes will be picked up and placed back in the tray or tub before exiting the machine. It's an entirely aseptic process, and the operators are gowned, qualified, and trained. All three filling lines are in a shrouded, Class 100 clean room environment.
HCP: Describe the key issues and trends that you see with regard to prefilled syringes.
Kinney: In this industry, prefilled syringes started appearing in the late 1970s. Before that, vials were primarily used. Some of the things that drove prefilled syringes were products that could not be placed or administered from a vial. Some viscous products that are gel-like don't lend themselves well to vials because when you are removing a liquid from a vial, you just put a needle on the syringe, pick it through the stopper and then pull back on the syringe. Then the liquid would flow out of the vial into the syringe. But very viscous products won't flow. A prefilled syringe allows a person to inject the total amount of drug directly into the patient. You can also increase the precision of dosing by using a prefilled syringe. You are not dependent upon a technician, an operator, or a pharmacist to pull the correct amount of liquid out of the vial into the syringe.
HCP: Where are syringes most frequently used?
Kinney: In a doctor's office, hospital, and now more often in the home healthcare market as well. The industry is moving in that direction, where prefilled syringes are becoming more in demand. One example would be for a patient with rheumatoid arthritis trying to manipulate a little vial and pull liquid out into a syringe and then make an injection, and having to change the needle on the syringe. But if you can give them the drug product already in a syringe, in the correct dose, with a needle attached, they can very easily make the injection.
HCP: What are some of the other issues that you see?
Kinney: Technologies are changing in terms of the manufacturing of the drug product, the processes, the filling and stoppering, putting the liquid into the syringe and then placing the stopper on it. The older technology for placing the stopper in a syringe after it was filled was to take the stopper, squeeze it inside a tube, which could fit down inside the syringe and with a rod, push the stopper out of that tube. That left a very large air bubble in the syringe.
The negative to that is when you have an air bubble in a syringe, and you expose that syringe to reduce the atmospheric pressure, as it happens in transport by airplanes, the air trapped inside the syringe expands and the stopper moves. The stopper can move back to a nonsterile part of the syringe. When you return back to ambient atmosphere, the stopper returns back to its original position and can potentially pull contaminated bacteria or a contaminant into the drug product.
HCP: To avoid that, what's being done?
Kinney: There are new processes called vacuum stoppering where a vacuum is pulled on the syringe. The stopper is then placed inside the syringe under vacuum. After the stopper is placed, the vacuum is released. Using that type of a process, one can decrease the bubble size, the headspace in the syringe down to nearly zero. That is the process we are using on the two Optima syringe lines. Vials always have a headspace left in them, but with a vial, the stopper is sealed and held in place by a crimp cap. So even though they are exposed to reduced atmospheric pressure, the stopper can't move.
HCP: On the two syringe lines using this technology, is that a separate unit that's attached to the Optima machinery?
Kinney: On our older filling machines, that was correct. It's an additional piece of machinery that sits next to the Optima machinery and after the syringes are filled, we have to place the syringes in this other machine from Becton Dickinson.
HCP: Any other technologies Hyaluron is now employing for prefilled syringes?
Kinney: Another technology that we are getting into is lyophilizing drug products in a prefilled syringe. There is only one company in the world right now that I am aware of that offers that as a service to other companies. It's a German company called Vetter Pharma Solutions.
Drug products have always been lyophilized in vials. The person administering the drug would have to add a diluent to the vial, shake up the product, dissolve it, and pull it back into a syringe and make the injection. That is a lot of manipulation, with considerable sources for potential errors. They can add too much or too little diluent. After the drug is dissolved, they can move too much liquid or too little liquid for injection into the patient.
If you can put your drug substance directly in the device from which the injection is going to be made, you can ensure that the correct amount of drug substance is injected into the patient, regardless of whether it was reconstituted with a little too much or too little diluent.
HCP: So, is Hyaluron lyophilizing in a prefilled syringe?
Kinney: Yes, we are doing that. We had to get some custom equipment built and made. It's not proprietary equipment. We made it ourselves from a local company that fabricated the devices. We fill the liquid into the syringes just as we normally would, as if we are going to fill just the liquid and not lyophilize it. They are placed into the lyophilizer. We had to build some special holders to hold the tubs and syringes in there. Then we had to design some special devices to hold the sterile stopper immediately above the syringe.
And, we had to create an insertion device because when something goes into lyophilization, it's frozen before a vacuum is pulled to sublimate off all the liquid and lyophilize the product. At the end of the cycle, you place the stopper inside the syringe.
In the early feasibility work we did, we would take the syringes out of the lyophilizer and in our clean room we would place the stoppers inside using the off-line stoppering method. However, this exposed the lyophilized product to ambient atmosphere inside, which has humidity. Generally, with lyophilized products, you want to keep them away from humidity. You are removing water from them because they are not stable in the presence of water. Some of them are very sensitive to humidity. So we needed to find a way to place the stopper inside the syringe while it was still inside the lyophilizer in a dry environment. We designed a means to do that.
Normally when you lyophilize a vial in a vial chamber, you have a stopper that is not pushed down all the way into the vial during the lyophilization process. At the end of the process, the shelves collapse. When they collapse, they push the stoppers down inside the vial to seal it. The vials sit on the shelves, on the floor of the cabinet, if you will. The shelves also have refrigerant flowing through them. That's what helps freeze the product that's placed inside. But at the completion of the cycle, the shelves collapse down on top of one another to push the stopper inside the vial before they are removed.
There are no stoppers made for syringes, so we had to find a means to suspend the stopper immediately above the syringe. We had to design special trays to do that. At the conclusion of the lyophilization cycle we modified our equipment to hold vacuum in the chamber at the completion of the cycle. We push the stopper down inside the syringe while it's still under vacuum. Once the stoppers are in the syringe, we release the vacuum. What you have is a syringe that has a vacuum inside it and as the air rushes in and the syringes are sealed, the air pressure pushes the stopper down inside the syringe.
We can control the height of movement of the stopper. In some cases, we want the stopper to move down so it's immediately next to the lyophilized product in the syringe. In other cases, we maintain some head space in there and control the depth at which the stopper will move in.
HCP: What different syringe sizes do you fill?
Kinney: We have used syringes that range between what is known as 1-mL long through a 10-mL size.
HCP: Does Hyaluron formulate its own products, or products for customers?
Kinney: We receive powders or solids from pharmaceutical and biotech companies. Some of them have their capability to make their own APIs (Active Pharmaceutical Ingredients), and others will outsource the manufacturing of the API to a contract manufacturer. They use us for filling and packaging. Then we ship them back to our clients.
HCP: Tell us about reconstituting the products for lyophilization in prefilled syringes.
Kinney: There are a couple of methods by which you can do that. You can put a needle on the end of the syringe and pull the liquid back into the syringe and reconstitute that way. There are a couple of companies that make reconstitution devices for products that are lyophilized: West and Duoject. Duoject's product is unique in that it allows you to add the liquid to the syringe through the stopper, rather than through the tip.