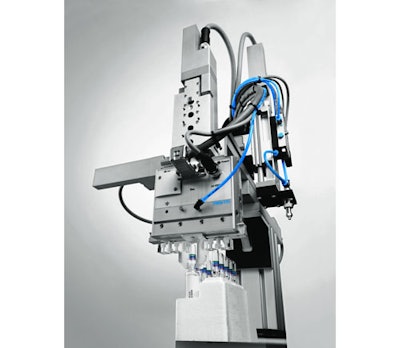
Festo is a worldwide supplier of automation technology and provider of industrial training and education programs. The company aims to maximize productivity and competitiveness for machinery builders, engineering firms, and packaging equipment end-users.
Healthcare Packaging (HCP): Sam and Craig, please tell us about your respective groups within Festo.
Sam Stoney (SS): Within Festo, the Medical Lab Automation team focuses on specialized components for medical devices, as well as standard components related to medical packaging, laboratory automation, and clinical diagnostics.
Craig Correia (CC): Festo's process automation group focuses on the area of fluid control. One important subsegment is biotech and pharmaceutical manufacturing and packaging.
HCP: What is important to your customers? What are you hearing?
CC: There is a major trend underway to develop flexible plants capable of producing multiple products in smaller batches, rather than building a plant based on a single blockbuster drug. The need for modularity and flexibility changes the way customers use automation, and also the solutions Festo must develop for the market. An example of this trend is the growth in the single-use bioreactor market. A bioreactor is a stainless-steel vessel in which the chemical reaction occurs--the heart of a biological manufacturing plant. Traditionally, large biotech companies would build bioreactors as large as 20,000 liters dedicated to a single product. As an alternative, single-use reactors are becoming more prevalent today because their primary benefit of fast changeover makes the plant more flexible. Whether in drug development phase or a multi-drug manufacturing plant, a single-use reactor allows the plant to change drugs in hours or days, instead of weeks.
This trend impacts everything around the company's floor plan. It might start around the reactor but continues all the way through final packaging. This change can put more demand on packaging (OEMs) in terms of the end-user specification demands. Festo helps OEMs meet these requirements by offering highly configurable products, as well as providing custom-built controls.
HCP: How do Festo products fit into this equation?
CC: With modular components and configurable systems. Companies have to rethink the way they do things to accommodate rapid and frequent product changes. In the drug manufacturing area, Festo offers a complete range of process control valves, I/O devices and engineered control cabinets that facilitate the control of the field devices and feed the data back to the end user's distributed control system (DCS). The market is constantly demanding products that communicate on more efficient and reliable networks such as EtherCAT, Profibus DP or EtherNet/IP, and we make sure our products can work with the newest network software as well as legacy networks. Festo is able to offer single-point diagnostic information (like distinguishing between a short circuit and a broken wire) and communicate it to the DCS with clear descriptive messaging. These technical advancements increase reliability and allow equipment to be scaled up or down in size for different products.
The same trends exist on the packaging end, except plants and machine builders utilize a wider range of our products. Festo manufacturers components: electrical and pneumatic actuators and controls, touchscreens with SCADA integration, and sensors, all designed to integrate together with a minimum of design and commissioning. Packaging OEMs must design equipment to handle products and batch sizes that can change frequently and easily; designing with Festo intelligent networked products gives their customers the flexibility to adjust with software and a minimum of mechanical changes.
HCP: How do the Festo control and automation products fit into the overall plant automation process or products?
CC: If you look at the controls of the manufacturing portion of a biotech or pharmaceutical plant, you have a distributed control system (DCS) from a company such as Emerson or Siemens controlling the plant and the recipe at the very top level. At the field level there are many different devices including flow and pressure sensors and diaphragm valves. Festo products operate right in between these two levels. Festo offers its FED touchscreens for operator interface, industrial PC-based controllers for local processing, pneumatic pilot valves, and CPX analog and digital I/O modules that collect the data from the field devices. By linking I/O devices to the DCS through an intelligent bus system, Festo eliminates a lot of wiring that in turn reduces installation and validation during start up, as well as reducing maintenance costs throughout the life of the equipment.
Packaging is more diverse in its use of automation and our product portfolio is much larger. Festo also has visual inspection systems, electromechanical and pneumatic handling systems, and we design and specify complete air preparation systems to meet ISO or NFPA standards. These products are used in areas ranging from dosing and filling to labeling and packaging.
HCP: Can you provide a specific packaging-related example?
CC: Yes: A capper machine, to be used towards the end of a packaging line. The trends mentioned create significant new challenges for the OEM design engineer: in addition to throughput and FDA compliance, the equipment must handle a wider range of products and batch sizes to meet market needs--this requires both mechanical and software flexibility. The capper may need to be controlled by upstream equipment, or provide production data through an end user-specified network. Modern equipment increasingly needs to go longer between maintenance cycles or, better yet, be able to indicate when maintenance is required--before there is an operational failure. Today, a more versatile product is needed at multi-drug production facilities. Festo meets this need in multiple ways: by developing standard handling units that can be scaled up and down for different cap sizes by changing parameters in the program. Networking everything together allows changes to be made from the top-level DCS or controller, as well as receiving internal diagnostics from downstream equipment, and this helps to minimize unplanned downtime.
SS: Correct me if I am wrong, Craig, but the big difference between the packaging and the process end is that the process end can be somewhat more proprietary. The tooling is generally more one-off on the process end, whereas on the packaging end, you are typically dealing with an assembly of turnkey machines that often have received prior device FDA approval from another company.
CC: You are right, Sam. I wouldn't say the process equipment is proprietary, but the product recipe is. The FDA is deeply involved with the product consistency, measurements, and the processes in drug manufacturing. On the packaging side, if you want to bottle something you can get a standard machine from the market. The FDA is still involved with validating the packaging lines and the processes but standard equipment and processes are often used. There are many companies that will integrate the cartoning, bottling, labeling, the weighing, and inspection equipment.
HCP: What are your customers seeing or anything changing with regard to packaging in this area?
SS: In medical packaging, a key issue will always be flexibility. Companies want to be able to reconfigure components and assemblies for different products, sometimes on a daily basis. Lines may have to be made to accommodate many different bottle sizes, or product shapes, or may have to track and handle different literature inserts or labeling for different markets. Being able to configure all the components of a line from a single interface can require that all the machines on the line sit on a common network and the same software.
CC: One other thing you will notice is there is a general trend towards standardization. In the past when a major drug company started a new project, there was little consideration about automation or standardization on the packaging side. They purchased standard equipment and didn't put much emphasis on the automation components inside.
We see a trend where companies are trying to cut costs by looking at the total cost of production and equipment over the life of a drug. For the past 15 to 20 years, the biotech and pharmaceutical industry was primarily concerned with getting a product to the market at any cost, but that has changed dramatically in today's economy. They are now spending more time looking for ways to reduce total cost of production. In response, most large engineering firms are offering value-added engineering programs aimed at reducing total cost of ownership. They are requesting that packaging OEMs use the same software, components, and services so that end users reduce cost of ownership by lowering spare parts, training, and maintenance costs. Festo initiatives in product engineering and support are delivering on the need for lowest total cost of ownership. --
By Jim Butschli, Healthcare Packaging Editor
Healthcare Packaging (HCP): Sam and Craig, please tell us about your respective groups within Festo.
Sam Stoney (SS): Within Festo, the Medical Lab Automation team focuses on specialized components for medical devices, as well as standard components related to medical packaging, laboratory automation, and clinical diagnostics.
Craig Correia (CC): Festo's process automation group focuses on the area of fluid control. One important subsegment is biotech and pharmaceutical manufacturing and packaging.
HCP: What is important to your customers? What are you hearing?
CC: There is a major trend underway to develop flexible plants capable of producing multiple products in smaller batches, rather than building a plant based on a single blockbuster drug. The need for modularity and flexibility changes the way customers use automation, and also the solutions Festo must develop for the market. An example of this trend is the growth in the single-use bioreactor market. A bioreactor is a stainless-steel vessel in which the chemical reaction occurs--the heart of a biological manufacturing plant. Traditionally, large biotech companies would build bioreactors as large as 20,000 liters dedicated to a single product. As an alternative, single-use reactors are becoming more prevalent today because their primary benefit of fast changeover makes the plant more flexible. Whether in drug development phase or a multi-drug manufacturing plant, a single-use reactor allows the plant to change drugs in hours or days, instead of weeks.
This trend impacts everything around the company's floor plan. It might start around the reactor but continues all the way through final packaging. This change can put more demand on packaging (OEMs) in terms of the end-user specification demands. Festo helps OEMs meet these requirements by offering highly configurable products, as well as providing custom-built controls.
HCP: How do Festo products fit into this equation?
CC: With modular components and configurable systems. Companies have to rethink the way they do things to accommodate rapid and frequent product changes. In the drug manufacturing area, Festo offers a complete range of process control valves, I/O devices and engineered control cabinets that facilitate the control of the field devices and feed the data back to the end user's distributed control system (DCS). The market is constantly demanding products that communicate on more efficient and reliable networks such as EtherCAT, Profibus DP or EtherNet/IP, and we make sure our products can work with the newest network software as well as legacy networks. Festo is able to offer single-point diagnostic information (like distinguishing between a short circuit and a broken wire) and communicate it to the DCS with clear descriptive messaging. These technical advancements increase reliability and allow equipment to be scaled up or down in size for different products.
The same trends exist on the packaging end, except plants and machine builders utilize a wider range of our products. Festo manufacturers components: electrical and pneumatic actuators and controls, touchscreens with SCADA integration, and sensors, all designed to integrate together with a minimum of design and commissioning. Packaging OEMs must design equipment to handle products and batch sizes that can change frequently and easily; designing with Festo intelligent networked products gives their customers the flexibility to adjust with software and a minimum of mechanical changes.
HCP: How do the Festo control and automation products fit into the overall plant automation process or products?
CC: If you look at the controls of the manufacturing portion of a biotech or pharmaceutical plant, you have a distributed control system (DCS) from a company such as Emerson or Siemens controlling the plant and the recipe at the very top level. At the field level there are many different devices including flow and pressure sensors and diaphragm valves. Festo products operate right in between these two levels. Festo offers its FED touchscreens for operator interface, industrial PC-based controllers for local processing, pneumatic pilot valves, and CPX analog and digital I/O modules that collect the data from the field devices. By linking I/O devices to the DCS through an intelligent bus system, Festo eliminates a lot of wiring that in turn reduces installation and validation during start up, as well as reducing maintenance costs throughout the life of the equipment.
Packaging is more diverse in its use of automation and our product portfolio is much larger. Festo also has visual inspection systems, electromechanical and pneumatic handling systems, and we design and specify complete air preparation systems to meet ISO or NFPA standards. These products are used in areas ranging from dosing and filling to labeling and packaging.
HCP: Can you provide a specific packaging-related example?
CC: Yes: A capper machine, to be used towards the end of a packaging line. The trends mentioned create significant new challenges for the OEM design engineer: in addition to throughput and FDA compliance, the equipment must handle a wider range of products and batch sizes to meet market needs--this requires both mechanical and software flexibility. The capper may need to be controlled by upstream equipment, or provide production data through an end user-specified network. Modern equipment increasingly needs to go longer between maintenance cycles or, better yet, be able to indicate when maintenance is required--before there is an operational failure. Today, a more versatile product is needed at multi-drug production facilities. Festo meets this need in multiple ways: by developing standard handling units that can be scaled up and down for different cap sizes by changing parameters in the program. Networking everything together allows changes to be made from the top-level DCS or controller, as well as receiving internal diagnostics from downstream equipment, and this helps to minimize unplanned downtime.
SS: Correct me if I am wrong, Craig, but the big difference between the packaging and the process end is that the process end can be somewhat more proprietary. The tooling is generally more one-off on the process end, whereas on the packaging end, you are typically dealing with an assembly of turnkey machines that often have received prior device FDA approval from another company.
CC: You are right, Sam. I wouldn't say the process equipment is proprietary, but the product recipe is. The FDA is deeply involved with the product consistency, measurements, and the processes in drug manufacturing. On the packaging side, if you want to bottle something you can get a standard machine from the market. The FDA is still involved with validating the packaging lines and the processes but standard equipment and processes are often used. There are many companies that will integrate the cartoning, bottling, labeling, the weighing, and inspection equipment.
HCP: What are your customers seeing or anything changing with regard to packaging in this area?
SS: In medical packaging, a key issue will always be flexibility. Companies want to be able to reconfigure components and assemblies for different products, sometimes on a daily basis. Lines may have to be made to accommodate many different bottle sizes, or product shapes, or may have to track and handle different literature inserts or labeling for different markets. Being able to configure all the components of a line from a single interface can require that all the machines on the line sit on a common network and the same software.
CC: One other thing you will notice is there is a general trend towards standardization. In the past when a major drug company started a new project, there was little consideration about automation or standardization on the packaging side. They purchased standard equipment and didn't put much emphasis on the automation components inside.
We see a trend where companies are trying to cut costs by looking at the total cost of production and equipment over the life of a drug. For the past 15 to 20 years, the biotech and pharmaceutical industry was primarily concerned with getting a product to the market at any cost, but that has changed dramatically in today's economy. They are now spending more time looking for ways to reduce total cost of production. In response, most large engineering firms are offering value-added engineering programs aimed at reducing total cost of ownership. They are requesting that packaging OEMs use the same software, components, and services so that end users reduce cost of ownership by lowering spare parts, training, and maintenance costs. Festo initiatives in product engineering and support are delivering on the need for lowest total cost of ownership. --
By Jim Butschli, Healthcare Packaging Editor