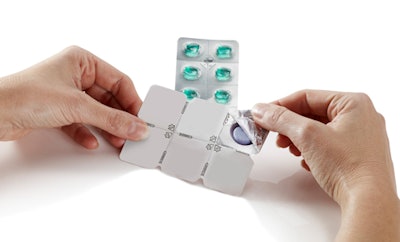
Joe Wittemer is the product development manager for Amcor Flexibles (www.amcor.com) Pharma-Americas, which focuses on flexible pharmaceutical plastic film, aluminum foil, and paper products. Amcor converts these materials into blister and strip packs, cold form laminates, and dosage cup lidding.
Healthcare Packaging (HCP): What are you hearing from your customers regarding sustainable packaging?
Joe Wittemer (JW): In general, pharmaceutical companies are looking to reduce the size of the package, the footprint of the package, and to address potential issues regarding package toxicity and safety. Some companies have initiatives to look at PVC (polyvinyl chloride)-free or BPA (Bisphenol A)-free alternatives. There is some discussion about recyclability, but the focus has mostly been on reducing the footprint of the package. From our perspective, we have developed considerable infrastructure related to sustainability and product stewardship. Our R&D and sustainability teams are dedicated to working with customers in managing the implications of their packaging material choices and using a systematic approach to look at the carbon footprint and determine how renewable, reusable, or recyclable the packaging materials are. At the engineering and product development levels, we are tasked to reduce the amount of packaging used for the customer's application.
There's another side to sustainability, though, that we cannot ignore, and that is the sustainability of supply. What happens when an upstream supplier moves, closes, or stops making a product? Managing this change upstream is a piece of the puzzle that can pose significant distribution implications and issues with regard to procedures, product safety, and regulatory matters. It's a huge challenge and one that we take very seriously. It is critical that any flexible packaging company fully respect the needs of pharmaceutical companies regarding change management or risk. I think that this is turning into one of the most dominant issues faced because so many suppliers are consolidating. Some of those companies are going out of business, merging, or having other events occur that affect supply. There are risks involved, and at times companies are seriously challenged to manage risk when changes are mandated. Pharmaceutical companies typically don't want many alternate suppliers because it presents risks to their supply chain stability and safety. Companies also have to be wary of supply that may be very low cost, but not produced in line with Code of Federal Regulations (CFR) expectations.
HCP: What are the current issues pertaining to compliance/adherence packaging?
JW: We're exploring technologies such as creating a defined area in the packaging material that permits easy opening locally, such as a push-through blister in one location on the package only. The other thing we are looking at making it easier to remove product from the individual blister-pack cavities while maintaining the necessary barrier properties. Special printing or coating techniques can also be employed to address compliance, track-and-trace, and senior-friendly issues. Some graphics can make the package active in nature in that you could use the package to report whether or not the patient is taking the product. The idea of active packaging offers many options regarding compliance.
We have also been challenged to meet the tremendous threat of counterfeit drugs in the marketplace. We have been able to support our pharmaceutical customer base globally with three supply sites and offer a variety of technologies that are based on integration of overt, covert, and forensic security features, with our core technologies in printing, laminating, extruding, and coating flexible materials.
HCP: Costs and technology-related issues can prevent some of these ideas from reaching the market, correct?
JW: Oh sure, but technologies like active packaging could be particularly helpful to improve the patient experience, for example aiding the elderly to ensure compliance. Many of the possibilities with active packaging haven't been embraced. Some reasons for this may be because change in pharmaceutical packaging is complicated due to issues such as validation and regulatory matters, or possibly an alternative to flexible packaging seems a more reasonable approach for the application. [HCP]
Healthcare Packaging (HCP): What are you hearing from your customers regarding sustainable packaging?
Joe Wittemer (JW): In general, pharmaceutical companies are looking to reduce the size of the package, the footprint of the package, and to address potential issues regarding package toxicity and safety. Some companies have initiatives to look at PVC (polyvinyl chloride)-free or BPA (Bisphenol A)-free alternatives. There is some discussion about recyclability, but the focus has mostly been on reducing the footprint of the package. From our perspective, we have developed considerable infrastructure related to sustainability and product stewardship. Our R&D and sustainability teams are dedicated to working with customers in managing the implications of their packaging material choices and using a systematic approach to look at the carbon footprint and determine how renewable, reusable, or recyclable the packaging materials are. At the engineering and product development levels, we are tasked to reduce the amount of packaging used for the customer's application.
There's another side to sustainability, though, that we cannot ignore, and that is the sustainability of supply. What happens when an upstream supplier moves, closes, or stops making a product? Managing this change upstream is a piece of the puzzle that can pose significant distribution implications and issues with regard to procedures, product safety, and regulatory matters. It's a huge challenge and one that we take very seriously. It is critical that any flexible packaging company fully respect the needs of pharmaceutical companies regarding change management or risk. I think that this is turning into one of the most dominant issues faced because so many suppliers are consolidating. Some of those companies are going out of business, merging, or having other events occur that affect supply. There are risks involved, and at times companies are seriously challenged to manage risk when changes are mandated. Pharmaceutical companies typically don't want many alternate suppliers because it presents risks to their supply chain stability and safety. Companies also have to be wary of supply that may be very low cost, but not produced in line with Code of Federal Regulations (CFR) expectations.
HCP: What are the current issues pertaining to compliance/adherence packaging?
JW: We're exploring technologies such as creating a defined area in the packaging material that permits easy opening locally, such as a push-through blister in one location on the package only. The other thing we are looking at making it easier to remove product from the individual blister-pack cavities while maintaining the necessary barrier properties. Special printing or coating techniques can also be employed to address compliance, track-and-trace, and senior-friendly issues. Some graphics can make the package active in nature in that you could use the package to report whether or not the patient is taking the product. The idea of active packaging offers many options regarding compliance.
We have also been challenged to meet the tremendous threat of counterfeit drugs in the marketplace. We have been able to support our pharmaceutical customer base globally with three supply sites and offer a variety of technologies that are based on integration of overt, covert, and forensic security features, with our core technologies in printing, laminating, extruding, and coating flexible materials.
HCP: Costs and technology-related issues can prevent some of these ideas from reaching the market, correct?
JW: Oh sure, but technologies like active packaging could be particularly helpful to improve the patient experience, for example aiding the elderly to ensure compliance. Many of the possibilities with active packaging haven't been embraced. Some reasons for this may be because change in pharmaceutical packaging is complicated due to issues such as validation and regulatory matters, or possibly an alternative to flexible packaging seems a more reasonable approach for the application. [HCP]