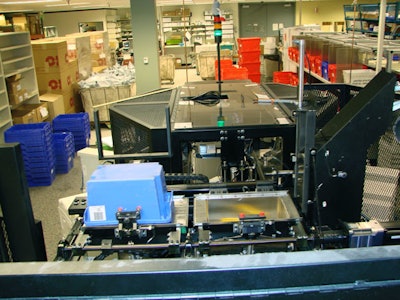
Providing quality healthcare while holding the line on costs continues to be a priority throughout much of the life sciences industry. Watching expenses is a critical task at Group Health as well, where the companys Seattle facility handles mail-order prescriptions and serves as a central fill location for its 26 pharmacies located in both Washington and Idaho. Since adding a Maverick Enterprises UPM B/T (Universal Packaging Machine with Bottle and Tote infeed), Group Health has reduced its labor needs, improved efficiency within its confined 7,000 sq area, and readied itself to handle growing sales volume. In turn, those benefits help to hold down Group Health member costs.
Marking its 60th year, Group Health Cooperative is an innovative, consumer-governed, nonprofit health care system that integrates care and coverage.
We used to produce 95-percent of our work for pharmacist orders from our Group Health centers, Colleran says, with 5-percent mail-order prescriptions. Now, its 55-percent mail-order and 45-percent for our central filling of prescriptions. We do about 10,000 prescriptions a day, and the trend to more mail-order prescriptions continues.
That trend is understandable, given that mail-order scripts are typically mailed directly to a patients home, so theres no need to drive to a pharmacy. Thats especially appealing when gasoline prices are high. Its also an option for those who may be transportation-challenged. And purchasing mail-order drugs often allows patients to order 90-day quantities, something that may not always be possible at their local pharmacy.
The challenge of fulfilling mail-order prescriptions, Colleran explains, is that they require more printing and packaging than is necessary for scripts picked up by patients at the pharmacy. As we moved more to mail orders, technicians at our facility had to print more patient information and put in literature and leaflets that they didnt need to do much of before, so it slowed down our process and required more people. Another challenge: Mail orders require more physical space to store materials and pack them.
Following the process
Prescriptions are filled upstream of the Maverick machine on an AutoMed OptiFill Gen IV. It takes an order from our Pharmacy system, labels it, and fills the product into a white high-density polyethylene bottle, from O-I . The bottle is then routed to a pharmacist for verification.
In the past, a packaging technician would scan the bar code on the bottles to verify accuracy and completeness of the order. This would generate a packing label for the bag, and any paperwork needed. The technician would then put these items into the bag with the package label on it, scan the packing label to complete the process, and place the package onto a Dornerbelted conveyor. The conveyor carries the package downstream where workers sort packages for mail-order shipment or distribution to one of Group Healths 26 pharmacies.
Before adding the Maverick machine, Group Health had one technician at each of eight manual packing stations. Each person could do about 90 packs an hour. With the mail-order business growing, says Colleran, We believed that this was an area that was right for automation because it was a totally manual process and had been a bottleneck.
We didnt have a large-enough tote volume just to have a totes-based system, he adds. We also didnt have a large-enough volume for a bottle-only system. It wasnt until Maverick developed an integrated product for both bottles and totes that it made sense for us to move in that direction. The Maverick system became operational at Group Health by July, 2006.
The Maverick process
Group Healths system is unique in that it handles both multi-order bottles as well as totes filled with unit-of-use products or combination orders. The pharmacy computer system sends order information to the Maverick database and the packaged products are conveyed to the Maverick UPM B/T packaging machine.
Once bottles and totes arrive (at two different areas on the machine), bottles are packaged first. The Maverick system reads each bottles unique vial identification bar code with a scanner positioned just upstream of the UPM. The machines software interfaces with the pharmacys software to determine what packaging label information and/or patient-specific printed material, including FDA medical guides are required with the prescription. The pharmacys software transmits that data to the Maverick, which stages the information for printing. Material for staged orders is printed six orders in advance of packaging using four high-volume paper printers.
Bottles are then conveyed past another bar-code scanner that reconfirms each bottles bar code against printed literature, thermally printing the customer label and bar code on the outside of the bag. This label includes the customer address for the mail order or the store information for a central fill. Literature is folded and inserted into the bag. A bottle chute opens and drops the bottle and literature into the bag, which is automatically heat-sealed. Sealed bags are then sorted into either mail-order or central-fill orders and conveyed to shipping.
For totes, the process is similar, beginning with totes leaving the pharmacist verification station. From there, they pass through a transfer station that sorts order types and directs totes appropriate for the Maverick packaging machine to a bar-code reader, where each tote is scanned. The order-specific information is then transmitted from the pharmacy software to the Maverick system. The information is staged and prioritized with the bottle-only orders. When the printed literature is complete and inserted into the waiting bag, the totes are mechanically flipped with products automatically inserted into the waiting bag. Bags are then sealed and sorted. Finished product is again conveyed to downstream shipping.
The Maverick is a packing system that replaces manual packers, explains Colleran. It prints paper, verifies that the paper goes with the order, verifies that the drugs go with the order, prints the packing information onto the bag, whether its for a pharmacy or the customers mailing address. It puts the items or bottles into the plastic bag and seals the package.
Determining return on investment (ROI)
Colleran estimates that the Maverick can accommodate up to about five bottles per 14.5x16 bag. The Maverick is a totally automated solution, he says. One part of determining our ROI on purchasing it was that we had no more space. This machine allowed us to actually consolidate some of our space. The other part is we were able to reduce the number of packagers [people] that we need.
We had two positions open that we didnt need to fill, and we were able to move one of our other technicians to another job, he continues. That was possible as a result of investing in the machine. We had an agreement with management that the machine would reduce three people, and by now, we would have needed a fourth, Colleran adds.
Instead of eight packing stations, Group Health now has four, but typically only uses one or two.
Beyond labor savings, the Maverick provides 500 packs-per-hour speed. And it doesnt care whether we are filling for our centers or mail orders, Colleran says.
We have been pretty happy with it, he notes. We were buying this machine for the future. We bought more capacity than we currently had in the system. So it isnt an automatic payback right now, even though Group Health usually looks for a two-year payback on equipment.
Group Health always has to watch its economic line, and not just for internal purposes. The advantage in
this packaging equipment also extends to our members as it helps us keep our rates as low as possible, says Colleran.