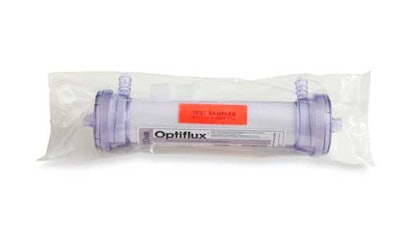
The Flexible Packaging Assn. issued a Gold award to a structure viewed as an innovative packaging solution for dialyzers (A). The multilayer film is manufactured by Pliant Corp., which now operates as Berry Plastics' Specialty Films Div., following Berry Plastics Corp.'s December acquisition of Pliant.
The award was one of 22 packages honored with 23 awards at the 2010 FPA Flexible Packaging Achievement Awards competition. Eighty-five flexible packaging entries (117 competition category entries) were submitted into the 2010 competition. Awards were announced March 10, at a dinner held in conjunction with the 2010 FPA Annual Meeting March 10-12 in Orlando, FL.
The 3.25-mil film for the dialyzer structure is a coextrusion of nylon and polyethylene. Pliant ships the unprinted film in roll form to a large North American-based OEM for flow-wrap packaging. The package encloses a dialyzer, and includes a fin seal and two end seals, according to Ketan Shah, director of sales/medical for Berry/Pliant. These products are used in dialysis equipment in hospitals or in renal dialysis centers.
The package allows the company, which preferred not to be mentioned by name, to switch to “an improved sterilization method that is more preferable environmentally,” says Shah. “It provides economies of scale compared to EO, as well as a shorter sterilization cycle time.
Barrier pouch eliminates need for secondary package
Products that undergo ethylene-oxide sterilization often require two pouches: An inner, open-ended foil pouch that contains the product, and an outer pouch that is sealed prior to sterilization. After the sterilization process, the outer pouch is often opened so that the inner pouch can be removed and sealed.
Oliver-Tolas Healthcare Packaging's Dispos-a-vent™ (B) barrier pouch eliminates this secondary package as well as costs associated with repackaging. The pouch features a disposable DuPont Tyvek® or paper vent for maximum airflow during EO sterilization and a high-barrier film or foil pouch area for easy conversion after sterilization. FPA honored the pouch with a Silver award.
“On one side, the pouch consists of a foil layer that runs the entire width and length of the package,” explains Chris Perry, R&D chemist. “On the other side, another coated or uncoated foil layer covers 75 percent of the package. The remaining 25 percent is Tyvek.” Foil thickness ranges from 2 to 3 mils. Oliver-Tolas uses a variety of foil suppliers. Substrates are either adhesive-laminated or extrusion-laminated, depending on the materials used.
The chevron pouch is heat-sealed on three sides. The foil-foil end is sealed while the Tyvek-foil end remains open so that the customer can insert its product into the pouch. After the pouch is filled, it is sealed at the Tyvek-foil end, allowing for breathability through the vented Tyvek portion during sterilization.
Following sterilization, the pouch is resealed, enclosing the product in the barrier area of the pouch, and the Tyvek portion is cut off. The sealed pouches are puncture-resistant to prevent product breakthrough. They also provide an oxygen barrier for product protection as well as a moisture barrier for prolonged shelf life.
Pouches are available in a range of sizes up to 36 x 36 in. They can be gravure-printed in one to four colors or flexo-printed in one to eight colors.
Phoenix Medical Products, a contract medical device manufacturer, uses the Dispos-a-vent pouches to package breast biopsy marker kits for one of its customers. The company could not disclose the customer's name. The pouches come in two sizes: 6.125 x 22.5 in., and 6.125 x 28.5 in.
“The kits are assembled manually on die-cut chipboard mounting cards and then loaded into the pouches in a cleanroom assembly operation,” says Barry VanDelinder, materials manager. After the pouches are filled, they are heat-sealed and packed into cartons. The cartons are then packed into boxes and shipped to the sterilizer. “When they come back from the sterilizer, we reseal them and trim off the Tyvek,” says VanDelinder. “We then pack them into the end-use shelf cartons and ship them to our customers.”
According to VanDelinder, the Dispos-a-vent's greatest advantage for his customers is the elimination of the secondary pouch. “If it wasn't for this package, our end customer would have us put a pouch in another pouch,” he said.
Custom bags ease transfer of bulk components to aseptic systems
When companies need to transfer a large amount of pharmaceutical packaging components into a barrier isolator or automated filling line, it's imperative that those components do not come into contact with the outside of the transfer bag. To help achieve this goal, Oliver-Tolas Healthcare Packaging's Isotech bag (C) maintains sterility and offers a protective barrier for the easy transfer of products, such as stoppers, caps, and pistons.
The Silver award-winning Isotech bag consists of an inner and outer bag heat-sealed or impulse-sealed together at the handle end. “We make the inner and outer bags separately, seal them individually, and then attach them together,” explains Michael Shellenbarger, Oliver-Tolas' technology project manager. “Bulk components can be heavy, so the seals on the bags are permanent, non-destruct weld seals,” he says.
An HDPE collar is heat-sealed to the opening of the outer bag, allowing the bag to be attached to a barrier isolator port. “The bag can be filled, steam or EO sterilized, and then hooked up to a barrier isolator so it remains sterile,” says Shellenbarger. “The customer can then transfer the components without them touching the outside.” The inner bag containing the product is longer than the outer bag and extends through the opening during product transfer.
Isotech bags are made of 1073B Tyvek with an average thickness of 7.3 mils. They are also available with Tyvek on one side and 3-mil HDPE on the other side, allowing the customer to see the product inside. The bags are puncture-resistant and are custom-made. Printing capabilities and other properties are contingent upon the size and material combinations selected.
By Kassandra Kania, Contributing Editor, and Jim Butschli, Editor
The award was one of 22 packages honored with 23 awards at the 2010 FPA Flexible Packaging Achievement Awards competition. Eighty-five flexible packaging entries (117 competition category entries) were submitted into the 2010 competition. Awards were announced March 10, at a dinner held in conjunction with the 2010 FPA Annual Meeting March 10-12 in Orlando, FL.
The 3.25-mil film for the dialyzer structure is a coextrusion of nylon and polyethylene. Pliant ships the unprinted film in roll form to a large North American-based OEM for flow-wrap packaging. The package encloses a dialyzer, and includes a fin seal and two end seals, according to Ketan Shah, director of sales/medical for Berry/Pliant. These products are used in dialysis equipment in hospitals or in renal dialysis centers.
The package allows the company, which preferred not to be mentioned by name, to switch to “an improved sterilization method that is more preferable environmentally,” says Shah. “It provides economies of scale compared to EO, as well as a shorter sterilization cycle time.
Barrier pouch eliminates need for secondary package
Products that undergo ethylene-oxide sterilization often require two pouches: An inner, open-ended foil pouch that contains the product, and an outer pouch that is sealed prior to sterilization. After the sterilization process, the outer pouch is often opened so that the inner pouch can be removed and sealed.
Oliver-Tolas Healthcare Packaging's Dispos-a-vent™ (B) barrier pouch eliminates this secondary package as well as costs associated with repackaging. The pouch features a disposable DuPont Tyvek® or paper vent for maximum airflow during EO sterilization and a high-barrier film or foil pouch area for easy conversion after sterilization. FPA honored the pouch with a Silver award.
“On one side, the pouch consists of a foil layer that runs the entire width and length of the package,” explains Chris Perry, R&D chemist. “On the other side, another coated or uncoated foil layer covers 75 percent of the package. The remaining 25 percent is Tyvek.” Foil thickness ranges from 2 to 3 mils. Oliver-Tolas uses a variety of foil suppliers. Substrates are either adhesive-laminated or extrusion-laminated, depending on the materials used.
The chevron pouch is heat-sealed on three sides. The foil-foil end is sealed while the Tyvek-foil end remains open so that the customer can insert its product into the pouch. After the pouch is filled, it is sealed at the Tyvek-foil end, allowing for breathability through the vented Tyvek portion during sterilization.
Following sterilization, the pouch is resealed, enclosing the product in the barrier area of the pouch, and the Tyvek portion is cut off. The sealed pouches are puncture-resistant to prevent product breakthrough. They also provide an oxygen barrier for product protection as well as a moisture barrier for prolonged shelf life.
Pouches are available in a range of sizes up to 36 x 36 in. They can be gravure-printed in one to four colors or flexo-printed in one to eight colors.
Phoenix Medical Products, a contract medical device manufacturer, uses the Dispos-a-vent pouches to package breast biopsy marker kits for one of its customers. The company could not disclose the customer's name. The pouches come in two sizes: 6.125 x 22.5 in., and 6.125 x 28.5 in.
“The kits are assembled manually on die-cut chipboard mounting cards and then loaded into the pouches in a cleanroom assembly operation,” says Barry VanDelinder, materials manager. After the pouches are filled, they are heat-sealed and packed into cartons. The cartons are then packed into boxes and shipped to the sterilizer. “When they come back from the sterilizer, we reseal them and trim off the Tyvek,” says VanDelinder. “We then pack them into the end-use shelf cartons and ship them to our customers.”
According to VanDelinder, the Dispos-a-vent's greatest advantage for his customers is the elimination of the secondary pouch. “If it wasn't for this package, our end customer would have us put a pouch in another pouch,” he said.
Custom bags ease transfer of bulk components to aseptic systems
When companies need to transfer a large amount of pharmaceutical packaging components into a barrier isolator or automated filling line, it's imperative that those components do not come into contact with the outside of the transfer bag. To help achieve this goal, Oliver-Tolas Healthcare Packaging's Isotech bag (C) maintains sterility and offers a protective barrier for the easy transfer of products, such as stoppers, caps, and pistons.
The Silver award-winning Isotech bag consists of an inner and outer bag heat-sealed or impulse-sealed together at the handle end. “We make the inner and outer bags separately, seal them individually, and then attach them together,” explains Michael Shellenbarger, Oliver-Tolas' technology project manager. “Bulk components can be heavy, so the seals on the bags are permanent, non-destruct weld seals,” he says.
An HDPE collar is heat-sealed to the opening of the outer bag, allowing the bag to be attached to a barrier isolator port. “The bag can be filled, steam or EO sterilized, and then hooked up to a barrier isolator so it remains sterile,” says Shellenbarger. “The customer can then transfer the components without them touching the outside.” The inner bag containing the product is longer than the outer bag and extends through the opening during product transfer.
Isotech bags are made of 1073B Tyvek with an average thickness of 7.3 mils. They are also available with Tyvek on one side and 3-mil HDPE on the other side, allowing the customer to see the product inside. The bags are puncture-resistant and are custom-made. Printing capabilities and other properties are contingent upon the size and material combinations selected.
By Kassandra Kania, Contributing Editor, and Jim Butschli, Editor