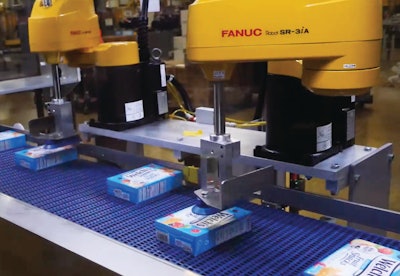
Producing fruit snacks 24/7 and operating now since November 2021, Mogul Line 5 at PIM Brands requires some serious packaging equipment to cope with the volume of fruit snacks it generates. So for primary packaging the Somerset, N.J., firm lined up eight combination scales from Multipond each paired with a vertical form/fill/seal twin bagger from GEA.
“It’s a direct feed from processing to packaging,” says engineering manager Chris Greco. “That means we don’t bulk off the product and then move it to packaging. In fact we don’t touch the product at all. It comes off the mogul [the term used in the confectionery industry for the machinery that makes shaped candies] into finished product conveying and then continues straight through to packaging. So as we evaluated the equipment we wanted on the new line, speed and footprint were two priorities. That’s where the Multipond/GEA stack-ups come in. Each pair pushes out about 360 bags per minute with each bag weighing 0.8 ounces.”
Packaging begins on an overhead level, where finished product is directed onto one of two long vibratory conveyors from Layton Systems. Running perpendicular to each of these conveyors are four smaller vibratory conveyors each leading directly to a Multipond scale. Product flows through these vibratory conveyors based on which scales are calling for it.Shown here are three of the eight twin-bagger discharge stations that deposit 0.8-oz bags of gummies onto the conveyor that carries them to a cartoning operation.
All of the Multipond scales are the Model MP-36-400-400-J2. Product falls into 36 buckets whose load cells register how much product is in each bucket. The weights are communicated to a central processor that then picks which combination of buckets contains 0.8 oz of product. Those buckets then release product down the twin tubes leading to pouch forming and sealing, which is where the GEA Smartpacker Twintube C machines come in. All eight of them pull roll-fed metallized film up over a forming mandrel and down into the sealing and filling station. The sealing jaws produce the top of the exiting bag and the bottom of the next bag. Why the Welch Foods graphics on bags and cartons? Because PIM Brands produces the fruit snack gummies under a licensing arrangement with Concord, Mass.-based Welch Foods, Inc.
Mounted on each of the GEA baggers is a SmartDate X30 thermal-transfer printer from Markem Imaje that imprints lot and date code information.
Return to overhead level
At this point the 0.8-oz pouches are down at floor level. But they need to return to the overhead level to reach the infeed of the combination scale that delivers them to a floor-level cartoner directly below. They make this return to the overhead level by way of a bucket incline conveyor from Wiese. “We like the Wiese equipment because it doesn’t use a chain to drive the buckets,” says Greco. “It’s a rubber-coated cable instead. By eliminating that metal-to-metal contact of chain on sprockets, you minimize wear. Also part of the Wiese system is storage capability that holds about 10 minutes of production so we can keep our baggers running if anything downstream goes down.”One floor above the twin baggers are eight 36-bucket combination scales that drop gummies down into the form/fill/seal baggers.
The unique combination scale above the cartoner is from Yamato (for more, see sidebar below). Directly beneath the Yamato scale is a TT-400 continuous-motion top-load cartoner from Tishma Technologies. A rotary picking device picks a flat carton blank from a magazine and places it into one of multiple pockets that move along an elliptical track. After bottom flaps are glued by a Nordson hot melt adhesive unit, the carton arrives under the Yamato scale’s dispensing bucket, which has been filled with the correct amount of pouches. Once pouches have been dropped into the carton, it advances to a station where top flaps are glued shut. At that point it’s on to case packing, though each carton first passes through a metal detector/checkweigher from Loma.
“We like the flexibility of this cartoner, which is the third we’ve installed from Tishma,” says Greco. “We’re able to run anywhere from a 10-count to a 160-count carton on it, though the two sizes we run on it most frequently are 22-count at 110 cartons per minute and 40-count at 70 cartons per minute. Servo motors make changeover quick, too.” The servos and overall controls package are from Rockwell.The case packer includes a pair of robots that quickly and efficiently orient cartons into the patterns required.
Before exiting the Tishma system, each carton runs past a laser coder from Markem-Imaje that delivers date code information. Cartons then are conveyed into end-of-line equipment from Schneider that includes case packing, palletizing, and stretch wrapping. “We installed a Schneider machine around seven years ago on a different project,” says Greco. “We got good service, the equipment is robust, and so we stuck with them since. Of course for this project we went out and got competitive bids, but once again when we factored in footprints, delivery times, performance, and cost, everything pointed to Schneider.”
The horizontal case packer includes a pair of Fanuc SCARA robots that perform an important carton rotating function. “Some cartons coming off the cartoner aren’t in the correct orientation for placement into the RSC case,” says Greco. “So these robots use a vacuum cup grip to turn a carton 90 degrees or 180 degrees, or they do nothing if the carton is correctly oriented.”
Integrated into the case packer is a 1580 ink-jet coder from Videojet as well as a ProBlue 7 hot melt glue system from Nordson. Also notable is the inclusion of two Schneider features:Case blanks are automatically erected, cartons are inserted, flaps are closed by way of hot melt adhesive, and finished cases are ready for palletizing.
• ProAdjust automatic changeover system, which utilizes a series of electric and air-driven power packs to reposition machine components when changeover is needed. It allows changeover from one product to the next in a matter of minutes instead of hours, and it’s done at the push of a button. Currently, two case formats predominate: either six 40-count cartons per case or six 22-count cartons per case.
• Intelligent Illumination, which proactively cues operators where attention is needed with customizable colors. Task lighting illuminates the machine where operators need good visibility to perform maintenance. This also allows operators to perform basic upkeep without even having to consult the HMI.
Versatile robotic palletizer
Next in line is a Schneider palletizer notable for the variety of tasks it performs. First, a five-high stack of empty pallets is conveyed into the system, and as soon as it’s in place the palletizer’s Fanuc robot uses built-in end-of-arm tooling to pick the top pallet and place it where it needs to be. That tooling then folds up and, for all practical purposes, disappears so that vacuum suction cups that are also part of the end-of-arm tooling can pick a paperboard slip sheet and place it on the pallet. The same vacuum suction cups are used to pick corrugated cases and place them on the pallet. When a pallet load is complete, the robot picks a paperboard slip sheet and places it on top of the load. The finished load then proceeds on floor-mounted roller conveyors until it reaches a WCA-Smart stretch wrapper from Wulftec, a Duravant company.In addition to placing cases on a pallet (shown), the end effector on the robotic palletizing arm can also pick and place an empty pallet into the case-loading station or pick a corrugated slip sheet and place it on top of a finished pallet just before it’s conveyed to a stretch wrapper.
“PIM Brands was a good partner in making sure we worked through all of the accumulation, safety, and shut-down considerations for the equipment,” says Schneider applications engineer Kevin Helinger. “That included such things as bypass options so that manual case packing or palletizing could be done if maintenance is needed on the equipment. It also included the placement of operator HMIs, E-stops, and disconnects in just the places where the PIM Brands operators need them.”