Companies in this article
Insulated systems protect pharmaceutical shipments
Delivering high-value, temperature-sensitive pharmaceuticals quickly around the globe through widely varying climates, while maximizing aircraft space, presents demanding challenges.
Oct 28, 2009
Break out of the ordinary: see what’s new in life sciences packaging
At PACK EXPO Las Vegas, you’ll see machinery in action and new tech from 2,300 suppliers, collaborate with experts and explore transformative solutions. Join us in September to experience a breakthrough for life sciences products.
REGISTER NOW & SAVE!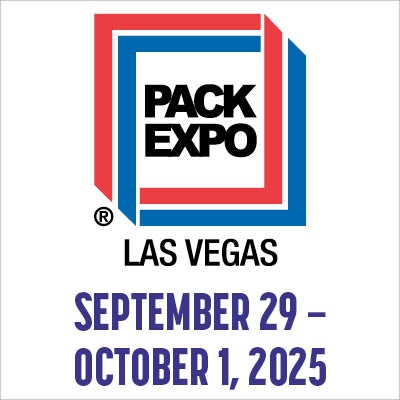
List: Digitalization Companies From PACK EXPO
Looking for CPG-focused digital transformation solutions? Download our editor-curated list from PACK EXPO featuring top companies offering warehouse management, ERP, digital twin, and MES software with supply chain visibility and analytics capabilities—all tailored specifically for CPG operations.
Download Now