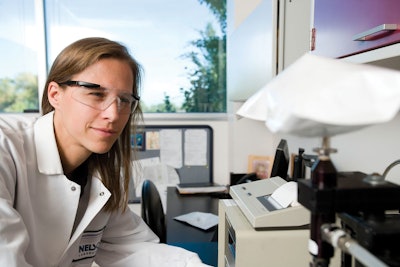
Headquartered in Montreal, Quebec, Canada, Medicom manufactures self-sealing sterilization and heat-sealing pouches for dental and medical applications, as well as dental instruments and medical products, such as surgical gowns and masks.
According to Jason Ludvig, Medicom’s product development manager, the majority of the company’s pouches are sold to the dental industry. “The main product we sell is a Kraft paper sealed to polyester-polypropylene film,” he says. “A self-sealing adhesive strip goes across the top, which is peeled off and sealed over by the end user after they load their instrument into the pouch.”
Finished pouches are produced via a laminating process and range in size from approximately 2.25 x 4 in. to 18 x 22 in., with the smallest pouches being used for dental instruments, such as burs or drill bits. Four-color printing takes place offline, and process indicators for ethylene oxide (EO) and steam sterilization are applied to the material prior to the pouches’ formation.
Although much of Medicom’s pouch testing is done in-house, the manufacturer also relies on the lab facilities at Nelson Laboratories in Salt Lake City for testing surgical masks and gowns. “When we want to submit to regulatory agencies, we need to have good laboratory practices in place,” explains Ludvig. “We don’t have that facility set up, so we do testing at Nelson Labs to supplement the testing we do.”
Medicom also turned to Nelson Labs when the company started manufacturing its pouches in-house rather than relying on a third-party supplier. “I approached Nelson Labs with the pouch program when we wanted to submit our own 510(k),” says Ludvig. Medicom’s products are classified as Class I and Class II medical devices, he explains, most of which require 510(k) submissions.