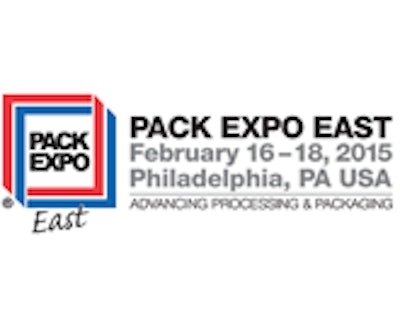
That was the gist of a February 16 presentation by Barry Lynch, Platform Global Marketing Director of GE Intelligent Platforms, at the Innovation Stage at Pack Expo East. Joining Lynch was Christopher Carlins, Senior Applications Engineer for GE distributor AutomaTech in Plymouth, MA.
While the concept of OEE--measuring equipment availability, performance, and quality to come up with a number reflecting a line or plant’s overall efficiency—has been around for a few years, packaging line OEE hovers around the 40-50% range, according to Lynch. World class-OEE can be in the high 80% range.
Many packaging operations are still relying on manually collected data, which is not only prone to operator error, it is also much harder to connect disparate pieces of information to get a clear picture of the root cause of problems.
AutomaTech’s Carlins told the Innovation Stage audience that only by automating the data collection will an organization gain the visibility needed to boost production efficiency, but you have to start small—with one piece of equipment or one line.
A great deal of thought has to go into converting data collection to a fully automated system. Some machines will have everything necessary already built in and it’s only a case of extracting the data through software. Other machines may not be as sophisticated, but an interface can be added where operators can select a choice of reason codes for stoppage, delays or waste, capturing real-time events.
Once you succeed in automating data collection you have the ability to view charts and graphs and further analyze where your operation needs improvement. After a small success with a machine or line, it is far easier to enlist the entire organization into your OEE efforts. Other operators or shifts will want to join in to improve their efficiency. Also, much of the up front work can be carried over to other machines and lines without the same lengthy meetings initially held to get started.
GE’s Lynch was responsible for one of the first-ever OEE installations in the U.K. back in 2002, and he shared some historical metrics from GE’s Proficy Efficiency software package. Companies utilizing automated OEE can potentially see:
• 39% reduction in downtime
• 35% plant improvement
• 5% increase in production yields
• 30% faster new product launches
Employing OEE though GE’s Proficy Efficiency analyzes equipment effectiveness “based on reasons and details to identify root causes and summarize and analyze data in the context of production events such as by equipment, by product or by personnel (hour, shift, and day) for improvement.”
The ultimate goal is a system where you have reports and dashboards available to make real-time production decisions driving maximum efficiency in your packaging operation.
One audience member, from a major pharmaceutical manufacturer, expressed concern about revealing his OEE to upper management. “If world-class OEE is in the high 80s and we come out at 40%, how is that going to look?” he asked.
Lynch cautioned that OEE is all relative, only a temperature taken at any given time, and a number in the 40s would mean there is potentially a lot of low-hanging fruit where success can come a little faster and easier.
“It would be much harder to go from 86% to 87%, “ said Lynch, “where you have already squeezed out that low-hanging fruit.”