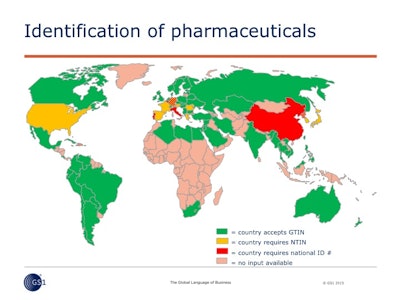
When it comes to serialization, "it’s never as easy as it sounds,” Unither Pharmaceutical’s Corporate Serialization Project Manager, Silvère Duchemin told the Pharmapack Europe crowd.
And, from his company’s perspective as a CMO with four plants in France and one in the U.S., he should know.
With 130 clients, more than 1,000 products distributed to 85 countries, Unither has serialized more than 40 million boxes, and have launched successfull serialization lines for China in 2012, Turkey in 2013, and Korea in 2014.
“I can tell you from the start, China’s barcode requirements, printed on line, create a lot more rejects than the 2D code,” he said.
Unither now has three lines dedicated to serialization, and Silvère came to share real-life experiences implementing serialization projects, from IT constraints and requirements, to partner selection to measuring economic impact to building a project team, as well as special insights on aggregation.
As a contract manufacturer, Unither faces a matrix of IT possibilities. Will serial numbers be generated by government authority or by the client? Maybe it will be partially provided by client but completed by the CMO with a randomization algorithm? It could be generated by CMO with a customer-specified format. In China they come from the government.
Will there be aggregation, and to what level—unit, bundle, case, or pallet?
And what about data transmission? Which format using which interface? Will it be encrypted and who will be the recipient? And when will the data be transmitted—at the moment of shipment, 24 hours later?
Duchemin mentioned one product that could not be accepted at the warehouse because data had not been transmitted yet and the warehouse receiving system did not recognize the newly commissioned serial numbers!
“All plants have existing equipment and IT systems,” said Duchemin. “And every authority has different regulatory constraints linked to products distributed in that market.
“You must be aware of your capacity and the cost to integrate a new client or new product into a new country,” he added.
The key to Unither’s success is flexibility, and being independent from a partner’s IT infrastructure. “What you will do, do by yourself,” told the audience.
“How accurate is serialization without aggregation?” he asked.
While the U.S., Turkey, and China require it, the EU does not. But regarding client or QA requirements, can we do without aggregation?
Beyond samples pulled from the line for testing, as well as rejects, you have damage when a case packer jams and destroys several cases.
These serial numbers still exist in the database. If you are running multiple shifts, how can you be sure the line worker will scoop up every carton and account for it by scanning and decommissioning it?
And again in the warehouse, you can have pallets and cases destroyed by forklifts. So reality does not equal what is in the database.
While aggregation may not be mandatory, physically a lot of things can happen. You end up with numbers for non-existent product. So how much of a gap is acceptable to you or your client?
When there is a gap between total serial numbers commissioned and your remaining physical goods, do you do nothing or only justify it?
Duchemin underlines that you are still complying with EU directives in that there is no way a counterfeit product can arrive without detection. But authorities, QA, or clients may have a different opinion and require to reduce or cancel a gap.
The first option would be to manually decommission all related products. But you need to understand the consequences of a mistake.
Without aggregation, imagine having 100,000 cartons and 100,001 serial numbers? You must now open every pallet, every case, and scan every carton.
Aggregation guarantees that after you scan your goods, the serial numbers missing do not exist anywhere.
So while it may cost two to three times more than non-aggregation, aggregation could be the most accurate and appropriate way to satisfy clients, regardless of EU directives.
There is an economic impact to starting up the serialized line. While you have no product loss, because it can be recovered and reworked, you do lose cartons, and they cost money, too.
Failures can include local ones like devices and machines, but you can have substantial loss because of IT virus, data loss, availability of the network, etc.
Here you must have root cause understanding of slowdowns and stoppages. If you do not, you have to start at the beginning and work though labeling, vision, etc.
For China’s 1D barcode, printed on line, Duchemin estimates a two percent loss due to bad code. So that’s a two percent loss on cartons.
Manpower and training cost as well when ramping up a serialization line. Decommissioning, rework, cost to reprocess, IT, maintenance, QA, supervisors—you may have to employ more workers, pay to train them, and they may have to be higher-skilled workers.
Further costs can come from retrofitting or buying new machinery and devices. Perhaps packaging and labeling will need to be changed. Perhaps new software is required? And you must negotiate with your partners on who maintains software, interfaces, machines, and your vision network.
As you begin, are you looking at your partner’s capacity to anticipate IT system interfaces, aggregation in the future, and what will be the impact on warehouse management systems?
Will your be flexible enough to anticipate future regulations, technological progress—adjusting for switching from Windows XP to Windows 7, for instance. One of the most difficult parts of managing aggregation is when a bottle or smaller package requires a temporary or helper code.
And for aggregation, with cases of more than one layer, you must retrofit cameras into the push plate of the cartoner, and all labels must be oriented outward.
“You may think there is no benefit to the CMO to implement serialization,” said Duchemin. “But there is one benefit in that your line is now connected to ERP and you no loner have to choose a label, manually type in batch number or expiry date. The software sends all the data to printers, checkers, and scanners, meaning less human error risk and more time savings—regardless of whether you are serializing or not."
Unither operates at about 70% OEE and Duchemin estimates a 5% loss of OEE due to serialization, but feels positive they can recover some of it. Unither chose to buy all new cameras, and there are action plans to make the cameras immovable, establishing stricter parameters.