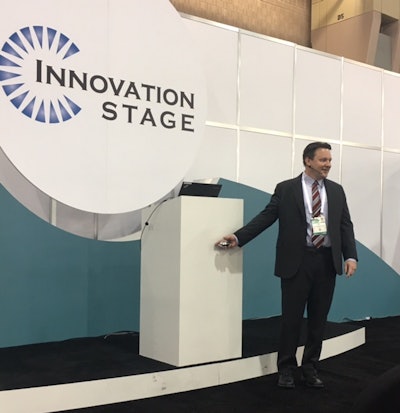
It’s still rare to hear about successful container returns in healthcare, but the Reusable Packaging Association (RPA) is helping a number of industries—including healthcare—make strides. While most picture pallets or large crates when they think of transport packaging, the effort includes primary, secondary and tertiary packaging. “Transport packaging is no longer just B2B. With e-commerce, it’s going directly to the front door,” said Tim Debus, President of the RPA, in his talk today at the Innovation Stage at PACK EXPO East in Philadelphia.
“With a reusable system, the idea is to build a finite pool of containers you can continuously use for transport and maximize the uses of that container,” he explained. When items are damaged, they should be repaired or remanufactured to prevent them from ending up at the landfill or recycler. “Recycling is considered the last resort in a circular economy.”
Debus noted that the term “disposable society” is certainly accurate, and brought up the following stats:
-
1.3 billion tons of solid waste are generated each year worldwide.
-
The U.S. generates approximately 20% of this waste, despite accounting for only 5% of the world’s population.
-
Approximately 30% of solid waste is attributed to consumer and transport packaging.
So is this a concept of how to manage waste? “No, this effort is all about preventing waste in the first place,” he said.
With the traditional linear economy, the people involved in making packaging were never the people throwing it away. Even now, the two groups don’t necessarily communicate with each other, or have visibility into the financial effects of this waste. But there are many industry groups, manufacturers and even governments working on shifting from a linear to a circular economy, and bolstering reuse of packaging.
Debus credits many technologies with enabling the reuse (and financial feasibility) of transport packaging, including sensors that monitor conditions/usage over time and the rise of networks and data-sharing. He identified four essential components (he credited Phillips for coming up with them as enablers):
-
A business model that looks at asset management and recovery
-
Product design that emphasizes durability for longevity in reuse
-
Collaboration between parties and partners in the supply chain
-
Reverse logistics processes
Debus highlighted the importance of a life cycle analysis to determine ways to save on costs, energy usage, product waste and more. He mentioned a scenario in which reusable strawberry containers were designed to maximize ventilation, which end up saving on overall cooling costs. In another case, Walmart switched to reusable transport packaging for fresh eggs, and prevented 37 million eggs from being thrown out in the first year.
Of course, healthcare packaging is (typically) a different ballgame compared to foods and consumer packaged goods. But Debus is optimistic about sterilization technologies and the ways that the healthcare packaging community can incorporate reusable transport containers and reverse logistics into operations.
He encouraged manufacturers to reach out to the RPA for guidance, as part of their mission is to spur innovation through best practices, process optimization and technology awareness. They also validate the impact of reuse through research, data modeling and case studies. Debus’ concluded with advice to review the critical variables for reusable packages:
-
Volume (trips)
-
Pool speed (cycle time)
-
And turns (reuse over time)
“Ideally you want the containers moving, not sitting in inventory. How many turns per year will help you calculate how many containers you need,” Debus said. He also emphasized the importance of cost reduction. “It could be a great solution for the environment and for the customer, but if it loses money instead of saving, it won’t work.”