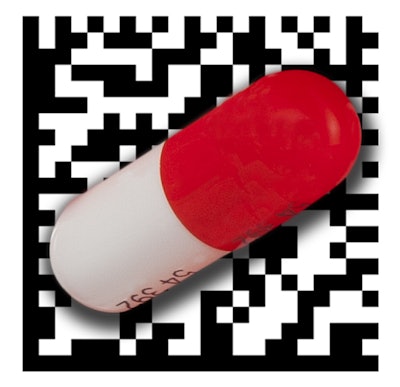
HCP: Serialization is complex and affects the entire organization, even outside supply chain partners. What are some of the most challenging aspects of implementing a serialization strategy?
Allard: That's why Optel Vision, from the get go, demands the entire team be invited to the table, from label control, validation, packaging machinery, IT, logistics, etc.
I would start first with the label control department. Many labels and cartons have enough space for lot number and expiration date but the blank area space is not sufficient for adding a unique serial number or a 2D bar code.
You might even have to change the print zone location. For example, when the cartons are packed in a case, the carton face that is still visible is the one on which, ideally, the serial number is printed. This way, one can clearly see and read the codes. With aggregation you want no assumptions, you need to be 100% certain the right cartons have been placed in the case.
Sometimes these artwork changes can take up to six months to be approved.
HCP: What about packaging machinery challenges?
Allard: Often we have to add a good six feet of conveyor to fit inspection cameras, reject station, even a print and apply for packaging levels that were not labeled prior to serialization (eg., bundle). Sometimes you might have to employ a robot solution to reduce the footprint and to enable a 90-degree flow direction change. We ask for the autocad layout files to determine what we can do to make the necessary room needed.
HCP: I have heard serialization guarantees a drop in OEE, this must be devastating for a packaging line.
Allard: Contrary to what you have heard, sometimes serialization can be the "kick in the pants" for an organization to upgrade-maybe a new cartoner, because the 12-year-old machine does not allow for a camera to be placed where it can record cartons in the case. Yes, an extra step like a print and apply or auto-reject zone could potentially slow line efficiency, but if you approach it as a whole system, you can often find opportunities to improve OEE as well.
The main challenge to maintain the OEE and also the operating costs is to avoid any new human interventions. Where a human is performing a task, the new operation needed for serialization must be well thought. For example, if an operator now needs to scan the cases prior to placing them on a pallet, the scanner is fixed, always reading, and is located in the trajectory that the operator used to move the case.
HCP: What about validation?
Allard: With serialization you have an all-interconnected system. There are strategies to properly consider every use case with this inter-system communication.
On a line with three new stations you could be looking at two, three, four weeks of downtime. You really want to prepare in advance and have each station validated 90% of the way prior to shutdown, and only have to do the final validation when everything is connected. Whether it's a reject station or a camera, make it self-contained and validate as much as you can in advance to minimize downtime.
HCP: Finally, let's examine IT considerations. The cloud is growing in IT, and just beginning to make inroads in factory automation. But I do hear it specifically mentioned when it comes to serialization.
Allard: The main advantage with the cloud is you are outsourcing just like you would for payroll. And you are paying only for what you use. So you can ramp up slowly over time and not have to pay for servers you are not currently using.
There are serialization software packages-Optel Vision has one-that will insure that, across all the plants, serial number will only be assigned once. We offer a serial number provider module, a repository module, and then you build on this for California e-Pedigree, or for Turkey's centralized database.
HCP: Finally, the end game for serialization, as I see it, is a Doctor without Borders or parents at home pointing their phone at a code and authenticating the malaria medication is not water, or the pediatric fever reducer is the only bottle in existence with that serial number. Will that day ever come?
(Editor's Note: At this point, Optel Vision's president Louis Roy joins the conversation.)
Roy: Let me say that while I cannot predict the future, when a pharma company adopts global serialization, the way has been prepared for this scenario to happen. All the pieces are in place to allow it.
I can see early adopters setting up a "Product Assurance" portal where consumers would be encouraged to check their medicines for authenticity. This would be a great marketing tool.
Optel Vision develops, manufactures, and supplies vision inspection and track-and-trace solutions for the pharmaceutical, nutraceutical, and cosmetics industries. Optel Vision will host a webinar on Serialization Challenges November 13, 2012. Register here to attend.