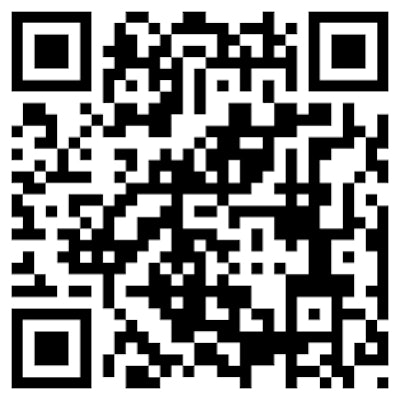
Product integrity pertains to the manufacturer's pack throughout the entire supply chain. Product authentication involves the employment of overt and covert features. Product identification points to serialization at the unit level in order to identify secondary packs for pharmaceuticals. By incorporating these elements, you'll increase the protection of your product.
That overview comes from Jean-Marc Bobeé, Doctor of Pharmacy, Sanofi-Aventis Industrial Affairs, during his Feb. 16 presentation at Pharmapack 2012 in Paris. This article is based on that presentation.
Bobeé explained that pharmaceutical package serialization requires the following two steps:
Step 1: Identification at the lot level. The coding of secondary packs of pharmaceuticals with a Datamatrix ECC 200 containing the product code, batch number, and expiration date. This has been mandated in France since Jan. 2011, and all other European countries must be in compliance by 2017 (except for Belgium, Greece, and Italy, which have until 2023). Canada and Korea are slated to roll out by 2012, while India has already put this into practice.
Five advantages to identifying at the lot level, according to Bobeé, are:
• avoiding dispensing errors
• automatic detection of expired products
• confirmed delivery of the correct product to the proper patient
• delivery traceability to the patient
• easy facilitation of batch recall
Step 2: Identification at the pack level (mass serialization at unit level) with a serial number assigned to each pack. This would give each pack a unique identifier comprised of the product code and the serial number. This serial number may either be included in a Datamatrix ECC 200 code printed directly on the pack, or preprinted on a label to be applied on the pack. If on a preprinted label, the label would need to be provided either by the manufacturer or by the government. There is currently a proposal for Europe to convert to Datamatrix ECC 200 with a style number for each drug and a batch number with expiration date, which happens to be what California plans to adopt for its serialization rollout in 2015.
Two advantages to serializing the packs are:
• preventing counterfeits if the serial number system is controlled
• fighting reimbursement fraud by reimbursing one pack at a time as opposed to the entire lot
The direct printing of a datamatrix code on secondary packs is the preferred means of serialization at this time because it's less complex to implement, less expensive, and provides additional traceability information for increased patient safety. However, both preprinted labels and printing directly on the packaging are currently being employed inItaly, Belgium, Greece, Serbia, China, and Argentina. Meanwhile, Europe (within the scope of ACF European Directive 2017/2023), Turkey, and California (2015) will be using the Datamatrix ECC 200 printing directly on the pack. This labeling will include a serial number, product code, batch number, and expiration date.
There are three different levels of product information controls, which can affect the efficiency of serialization, patient protection, and cost.
Serialization with no systematic control
In the supply chain, this is the most basic control scenario. This level is being used in Italy, Greece, and Brazil, and it's mainly implemented to fight tax and reimbursement frauds. One of the benefits of this system is the ability to use the serial number in the database to investigate a product after delivery. It's also simpler to implement than control at the dispensing point or at the intermediate level of the supply chain, therefore it poses no additional workload for pharmacists or wholesalers.
The cons: There's no real-time protection for the patient and there's no possibility to stop a counterfeit product before it reaches the patient. And, the costs outweigh the benefits since there's significant expense for the manufacturer to serialize, but no real protection for the patient.
Serialization with systematic control at the dispensing point
This is the EFPIA Concept in Europe, which consists of two parts. One is the unified intelligence of pharmaceutical products coded throughout Europe via the implementation of a serialized datamatrix code on secondary packaging for all products sold in Europe. This information includes the product code, batch number, expiration date, and serial number. The second part is the verification of pharmaceuticals at the point of dispensing through serial numbers. This method is efficient at both fighting reimbursement fraud, and improving patient safety by preventing counterfeits.
It is, however, more expensive than post-delivery statistical control. It requires readers and a system in place so that pharmacists can verify the serial number. Also, a database isn't failsafe. It can have more serial numbers than real products. The cost/benefit ratio for this particular solution is high. Yet, it is the most effective serialization solution, said the presenter. While there is an investment for manufacturers to serialize their products, and by pharmacists to verify product information at the dispensing point, this is an extremely effective solution to secure both patients and the drugs.
Control of serial numbers at all levels of the supply chain
Turkey uses this method, employing the parent-child relationship at all levels from unit to pallet. When you establish a parent-child relationship, you have the opportunity to track back to a specific pack, or locate a specific pack. You have the distribution history at a unit level. Another benefit is information of the packs that are contained in any case or pallet, which is useful to avoid or track theft.
But, this system is complex, costly, and difficult to put in place. It requires aggregation between manufacturers, wholesalers, and pharmacists. It can negatively impact the overall equipment effectiveness of the packaging line. Since this level of serialization offers limited added value over systematic control at the dispensing point, it has a limited cost/benefit ratio.
Bobeé said the ideal situation for serialization is a worldwide, unified database, which would increase patient protection and decrease counterfeit activity, yet be nearly impossible to create and implement. Mass serialization on a country-by-country basis, using open standards and technology like the datamatrix code and controlling products at the point of dispensing step toward the goal of increasing patient safety and decreasing counterfeits.
Particularly interesting was Bobée's assertion that full serialization from the unit to pallet levels, and the establishment of a parent-child relationship is too expensive to implement and doesn't have the benefits to back the investment. We hear a lot of information in the United States about track-and-trace capabilities being best for thwarting anti-counterfeiting. According to Bobée, as long as the secondary packaging is serialized with the datamatrix code, there is no need for additional levels of security.