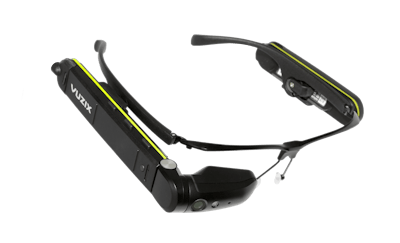
MG America, the U.S. subsidiary of MG2 of Bologna, Italy and a supplier of processing and packaging equipment, has launched a Remote Technical Assist (RTA) program designed to allow line personnel to see and interact with technician specialists for real-time equipment troubleshooting and training. Also designed to reduce machine downtime and operator error, the comprehensive equipment assistance initiative comprises emergency support, line integration, and training sessions.
Performed via secure WiFi, 3G/4G, or ethernet connection, the Remote Technical Assist program should allow line personnel to hear, speak with, and see technicians specially trained in specific MG America packaging and processing equipment; sessions also can include live streaming, instant messaging, file sharing, pics/screenshots, and annotations.
The program should be able to incorporate sophisticated virtual diagnostic tools that allow line operators to share issues with offsite technicians. Footage from endoscopes, microscopes, UV/IR cameras, earscopes, and iriscopes can be transmitted to technicians in real-time, resulting in quick fixes that get production recommenced quickly, says the company.
Akin to having a specialist working shoulder-to-shoulder with line personnel, the RTA program is made to simplify complex tasks via step by step guidance that should diminish production delays and maximize overall line efficiency.
The RTA program is made to simplify complex tasks via step by step guidance that should diminish production delays and maximize overall line efficiency.
“In addition to the obvious advantages of virtual troubleshooting and training, including decreased downtime and enhanced line personnel machine proficiency, the Remote Technical Assist program also diminishes the time and cost involved with in-person maintenance, repair, and training,” says Nick DeSantis, service manager for MG America.