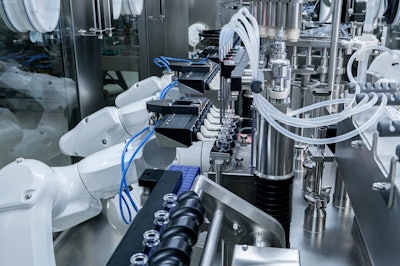
This content was written and submitted by the supplier. It has only been modified to comply with this publication’s space and style.
Steriline, a company highly specialized in filling solutions for the aseptic processing of injectable products, will present a new Robotic Nest Filling Machine at Interphex 2023 (Booth 2537), from 25th to 27th April in New York.
Steriline's robotic systems provide a high level of efficiency, safety and flexibility for the production of toxic and non-toxic drugs, reducing the risk of human error and improving overall quality. The company's technologies are designed to meet the needs of key pharmaceutical sectors, such as the cell and gene therapy market, where quick turnaround of high-value product is critical.
Steriline's fully isolator-based robotic systems have a small footprint and are equipped with advanced technologies, including fully disposable fill paths, 100% in-process check-weighing combined with a “zero-loss philosophy”.
Steriline's solutions are compatible with various primary containers such as vials, ampoules, cartridges, syringes and bags. The systems can handle products in both liquid and powder form and can be equipped with Laminar Air Flow (LAF), Open and Closed Restricted Access Barriers (oRABs, cRABs) and Isolator Barrier Systems (ISOs) to ensure air monitoring and compliance with FDA regulations and current Good Manufacturing Practices (cGMPs).
"Steriline introduced robotic applications into the aseptic processing market in 2014, one of the first players," said Federico Fumagalli, chief commercial officer at Steriline. "Since then, we have been continuously adapting our technologies to address all the fill/finish operation needs of the pharma industry, including Cell & Gene Therapies, where the demand for quick turnaround of high-value product is critical."
James Rorke, vice president of North American operations at Steriline, added: "When a batch is only a few liters of product and worth tens of thousands of dollars or more, our customers expect the highest yield from their fill/finish systems. Showing that we can deliver practically every drop of product into a vial or syringe, without product losses, and having the data to prove every single container has been filled to the optimal volume has been a game-changer for our customers."