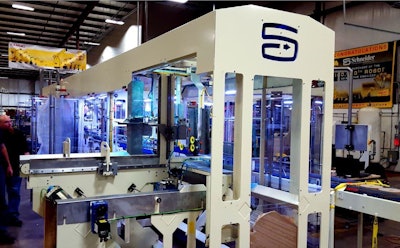
The idea is to use multicolor LED lighting inside the framework of a machine—here it happens to be a case packer--to cue end user personnel on the plant floor as to the condition of the packaging equipment for which they are responsible. Blue is one of the colors involved. Schneider calls it Schneider blue, but just five days removed from a rather memorable baseball game in Cleveland, I’m quite certain it’s Cubbie Blue. In any event, blue lighting signifies that the machine is purring along the way it’s supposed to. But what if the magazine holding knocked-down corrugated case blanks is running low? Or suppose the roll of tape that the machine applies to close the cases is running out? Or maybe a misshapen case has caused a jam. When any one of these things occurs, sensors detect it and signal the machine’s main controller. Immediately the controller signals an LED light bar at the precise location where the issue has surfaced. Voila, the light bar turns to amber. This allows the operator to go quickly and directly to the point of the machine that requires attention. There’s no need to consult the HMI or anything. The operator can go where he or she is needed without hesitation and address the issue. One other feature of Intelligent Illumination is that the minute the operator arrives at the problem spot and opens the guard doors, LED task lighting is automatically switched on so the job of fixing whatever it is that needs fixing can be performed in ideal conditions from a visibility standpoint.