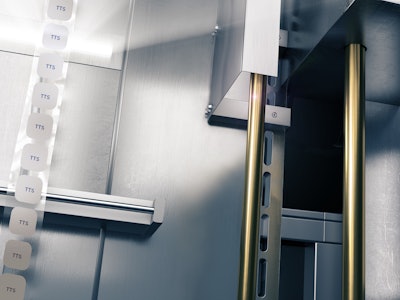
Transdermal patches continue to increase in popularity, due in part to their non-invasive, painless delivery as well as the convenience factor. Research and Markets recently reported that 40 such patches are available on the market and 70 more exist in the clinical pipeline, while Grand View Research noted that the market for transdermal drug delivery systems accounted for $31.6 billion in 2015.
Transdermal therapeutic systems (TTS), also known as active ingredient patches, which administer their active ingredients through skin contact, must undergo robust inspection processes during production.
This week, Germany-based Vitronic has launched its new VINSPEC HEALTHCARE system that offers 100% quality inspection of these products.
According to Vitronic’s Peter Manz, the system inspects at multiple stages during the production process, which includes:
-
The backing layer during the first step of patch manufacturing, where the system can detect contamination as small as 0.1 mm².
-
The quantity and position of the substance after the active ingredient is applied to the backing foil (these figures are then compared with target values). The system also inspects for contamination at this step.
-
The punching and sealed seam of the TTS itself.
-
The printed elements on the surface of the pouch packaging (positioning of the text, print quality including OCR, OCV and barcodes) as well as the sealed seam running around its perimeter.
The system can inspect 200 parts per minute and webfor batch production and 400 parts per minute and web for continuous production. Manz noted that the individual inspection solutions can be flexibly adapted to various product types with short changeover times.