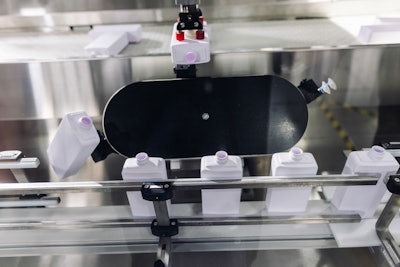
Bottling lines are notoriously chaotic. Empty bottles clatter down conveyors at high speed and in disarray, pointing in every direction but the required orientation for filling. Bringing order to this chaos requires machines and robotics that tackle complex requirements like ultra-high throughput, flexible format changeovers, and soft-touch handling.
Finding an unscrambling system that’s optimized for all three factors has proven difficult for CPGs. So, Pace Packaging, a ProMach Product Brand, set out to solve this dilemma when designing the VersaSort Robotic Unscrambler and BAO-IR Orienter.
“The VersaSort linear unscrambler improves maintenance access, reduces complexity, and offers a more competitive price point with enhanced performance,” says Michael DiGregorio, vice president and general manager at Pace. “This is a win-win-win for our end users.”
Sorting machine design challenges
“Pace’s key differentiator is our ability to work with customers on custom solutions that rapidly unscramble wide ranging bottle and container types,” says Anthony Ferraro, director of engineering at Pace.
Most unscrambling solutions focus on high-volume processing of one or a few specific bottles using belt and hook technology. Another new Pace machine, the OMNI-IR line proves that this technology still provides an ideal option for some applications. The VersaSort, however, targets customers with high SKU counts and frequent format changes, particularly in personal care, cosmetics, and pharmaceutical applications. The system goes a step further by supporting operations that need to handle delicate materials and special finishes.
Rather than relying on traditional tactics, the VersaSort system deploys up to three pick-and-place robots [in the model pictured below, the robots are by ABB]. It also harnesses innovative vacuum transfer and integrated orienter systems designed in-house by engineers at the ProMach Innovation Center (PMIC) in Montreal. It delivers a uniform outfeed via precision conveyance, with the option to add puck-based handling as needed in different packaging applications.
Innovative automation technologies from Beckhoff offer the flexibility and power needed to implement these design features, as DiGregorio explains: “The VersaSort system maintains the reliability that Pace is known for, with machines running over 30 years in the field before needing rework. We updated our product line to offer a solution that fits the challenging demands of today’s packaging industry customers.”The patent-pending in-motion vacuum transfer system designed by engineers at ProMach eliminates mechanical components and accelerates throughput on the VersaSort.© Beckhoff, 2024
The VersaSort features an integrated hopper, with a series of infeed conveyors to begin the unscrambling process. Next, a rotary bumper gently presorts bottles into a single, flat layer. A vision system identifies the bottle types and how they’re oriented, so pick-and-place Delta robots can grab each bottle with vacuum grippers and place it on the paired patent-pending in-motion vacuum transfer system.
“We can run a higher containers-per-minute rate per robotic unit than other descramblers on the market because of our vacuum transfer system,” DiGregorio says. “This technology ensures that the system can handle a wide variety of container types without causing damage, including delicate products with soft-touch finishes.”
The vacuum transfer system places each bottle onto a narrow conveyor, or integrated pucking solution. The ProMach-developed orienter then spins the bottles to ensure a uniform outfeed as they proceed into further stations down the line for filling, capping, cartoning, and so on.
Pace faced several challenges to deliver the necessary flexibility, simplified maintenance capabilities, and pushbutton changeovers.
“We wanted to reduce the number of parts, the complexity for our customers’ operators and maintenance, and the footprint so the machine can fit in plant floor spaces where our competitors’ equipment can’t,” Ferraro says. “We also wanted to reduce the labor that it takes our own production team to assemble the machine.”
The ProMach engineers worked with the automation and packaging industry experts at Beckhoff to check all the boxes in the ambitious machine design. The two companies had recently worked together to update an unscrambler in Pace’s OMNI line to achieve similar goals.
“After already working with the Pace team on the previous unscrambler, we had established great success and were able to replicate that with the new goals they set,” Greg Marsh, Packaging Industry manager at Beckhoff USA. “Everyone wanted to keep up that momentum with the VersaSort project. Our advanced machine controls, drive technology, and EtherCAT networking solutions laid a solid foundation for this powerful new unscrambler.”
New automation tech
The integration of Beckhoff technology has allowed Pace Packaging to offer a more versatile and reliable solution to their customers. The VersaSort relies on a C6025 ultra-compact IPC from Beckhoff as the primary machine controller.Pace built the VersaSort Robotic Unscrambler and BAO Orienter to shrink footprint requirements, minimize maintenance efforts and cost of ownership, and provide the fastest throughput per robot on the market.© Beckhoff, 2024
“Real-time EtherCAT communication and high processing speeds of the industrial PC with dual-core Intel Celeron processors made this possible,” Ferraro says. “Unlike traditional PLC technologies, PC-based automation allows us to handle all automation and control on one device, with the seamless integration across the Beckhoff platform, the robot controller, and vision system.”
Beyond sheer speed, the companies say that EtherCAT provides numerous advantages through its functional principles. EtherCAT’s automatic addressing with no IP addresses, free selection of wiring topology, and up to 65,635 devices on one network ensures a flexible and scalable network for the future.
“For Pace, the advanced diagnostics in EtherCAT provided clear advantages for commissioning and operation,” Marsh says. “In addition, they could leverage a wide range of EtherCAT I/O modules from Beckhoff, both in the DIN rail-mounted terminal and IP67-rated EtherCAT Box form factors, to achieve incredible design flexibility inside and outside of electrical cabinets.”
In addition to standard I/O functionality, Pace leveraged TwinSAFE I/O terminals for functional safety deployed in safety doors, e-stops, etc. TwinSAFE relies on proven Safety over EtherCAT (FSoE) technology to provide “black channel” communication on the standard network, without the cumbersome hardwiring required in legacy standalone safety systems.
The ProMach engineers also used the EP7211 single-channel servomotor box for compact motion control in an I/O format. Along with these EtherCAT Box modules, the AX8000 multi-axis servo system from Beckhoff provides high-precision control for various AM8000 servomotors equipped with AG series gearboxes. The AX8000 drives feature Beckhoff’s AX-Bridge technology to directly connect drive modules without additional cabling or tools. This reduces power supply requirements, simplifies wiring, and accelerates installation times.
“We increased speed and throughput on the VersaSort by eliminating the mechanical grippers with our vacuum transfer system but also through the Beckhoff motion technologies,” Ferraro says.
TwinCAT 3 automation software supplies an end-to-end engineering and runtime platform for packaging machines and fully supports the PackML standard. Integrated into Microsoft Visual Studio, TwinCAT 3 gives engineers the power to program in whichever languages best serve the application, including IEC 61131-3 languages with object-oriented extensions, predefined or custom function blocks, and computer science standards. This also greatly expands the pool of available engineering talent that can work on packaging machines beyond traditional PLC programmers.
“Pace was able to leverage different software packages in TwinCAT for PLC, functional safety, motion control, and HMI,” explains Thomas Lauria, regional sales engineer at Beckhoff USA. “The more intuitive HMI, built with TwinCAT HMI, helps operators obtain advanced diagnostics for preventative maintenance and allow for precise machine adjustments as required.”The VersaSort uses a variety of EtherCAT I/O Terminals from Beckhoff, including yellow TwinSAFE terminals for system-integrated functional safety.© Beckhoff, 2024
A ProMach-branded CP2916 custom Control Panel delivers smartphone-style operation through its multi-finger touchscreen capabilities. The industrial hardened, 15.6-inch display hardware mounts directly into the Plexiglas enclosure so operators can see everything that’s happening as they control the machine. The control panel also features CP-Link 4—the One Cable Display Link—which combines USB, DVI, and power supply via a single cable. This further reduces wiring and installation time.
“The Beckhoff display for the HMI is large and easy to read, and it offers enhanced design and maintenance features,” Ferraro says. “So, plant staff can clearly see trending production data, alarms, and other operational information right on the HMI screen, which ensures user friendliness.”
Today, Pace Packaging says the VersaSort system represents a major technological leap. The versatile, highly efficient solution unscrambles a wide range of container types, including market standard materials and soft-touch variants. It also accommodates container sizes from 10 mL to 9.5 L without tooling changes and shrinks changeover frequency by up to 25% compared to systems with mechanical grippers.
In addition, the EtherCAT-enabled, high-speed motion control, in-motion vacuum transfer system, and scalable robotics integration deliver top-tier throughput. VersaSort provides speeds of 120 containers per minute (CPM) with one robot, 230 CPM with two robots, or 340 CPM with three robots.
“The VersaSort robotic unscrambler offers a higher throughput per robot than comparable systems on the market,” DiGregorio concludes. “On top of that, customers with a high SKU count that need to change container types day to day or shift to shift, can activate automatic changeovers via a simple pushbutton, which reduces the amount of technical experience and training required. All in all, the new VersaSort system makes their work much easier.” PW