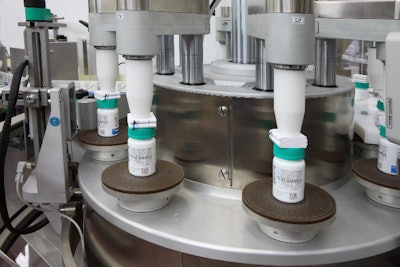
Marchesini Group’s complete track-and-trace line produced for a multinational pharmaceutical enterprise uses flexibility and reliability throughout.
The line, which serves as a model of how to serialize pill containers packaged directly in cases without first putting them into cartons, consists of the rotary labeler model RE 302 and a top-loading case packer, model MCPV 850. Both machines have their own traceability system that continuously monitors the products throughout the entire packaging process.
This line includes vision systems, installed on the vial labeler and on the case packer, which monitor the products from the initial coding phase of the individual unlabeled bottles through to the palletization phase of the filled and sealed cases. The machines operate with “Fail Safe” logic to ensure that all non-conforming products are rejected.
Automatic rotary labeller RE 302 1T
The bottles, fed from the upstream machine are already filled and capped prior to transferred onto a conveyance system made up of two vertical belts on the inlet of the labeling machine. These belts hold the vials by their sides while an ink-jet marker prints a unique 2D service code on their bottom, which is also verified immediately by the first camera.
On the inlet of the main starwheel, the second camera acquires the 2D service code printed previously on the bottom and sends the start signal to the shift register, which acquires the position of each bottle.
The label is printed and the unique 2D code is verified immediately by a third camera. The code comprises a product identification code, batch number, expiry date, and unique serialized number with all data repeated also in readable digits. The camera grades the print quality of the serialized 2D code and scans the readable digits with an OCR/OCV system.
A fourth optional camera reads the Pharmacode on the labels to identify them accordingly.
Once the label has been applied to the vial, a fifth camera scans its unique serialized 2D code and, by means of the shift register, associates it with the unique 2D service code printed on the bottom. The positioning of the label and code in front of the camera is ensured by the top hold down and locating devices that are inherent to the design of the RE labeler. Each unique serialized code printed on the label, graded and correctly applied, is consequently associated with the service code, printed on the bottom of the containers. By matching the two 2D codes, it is possible to trace the vials in the downstream case packer.
Top-loading case packer MCPV850
Good product discharged from the RE302 1T continues downstream to the infeed of the MCPV 850 case packer. Here, they are grouped into layers on a glass surface where the control station is located. With a sixth camera the unique 2D service codes printed on the bottom of the containers of each layer are read. The unique 2D service codes provide an exact match with the unique serialized 2D codes associated with them on each bottle so that they can be acquired.
A pick-and-place unit picks up the layers of containers and places them inside the case, which is subsequently sealed with adhesive tape. At this stage, the full and exact identification of the bottles inside each case is known. A label is then applied on the corner of each case, on which a unique serialized code is printed in real time, which is associated with all the unique serialized codes of the bottles inside the case.
A seventh camera verifies this code printed on the label of the case. This operation starts the aggregation of the individual products inside the cases. Finally, each compliant case is picked up by the pick-up arm of the palletizer Gigacombi unit, which places it on the pallet according to the pattern saved on the machine’s PC. At this stage, the aggregation of the individual cases on the pallet continues, applying another label on the corner, which is verified by another camera, and on which a unique code will be printed in real time that is associated with all the unique codes of the labels of the cases.
Additional benefits
This line is able to satisfy the demands of the marketplace by integrating traceability systems along the entire production process, as explained above, but also due to the use of machinery. All equipment involved is reliable, flexible, and user-friendly.
The labeler RE302 uses not only a track-and-trace”system, but it guarantees all the advantages of the Neri RE range of machines: meaning that they are all accessible and the entire production process is visible. Also, size changeover is quick and straightforward thanks to special digital indicators. Label application is precise, with any noncompliant products rejected automatically.
Other bonuses are versatility and speed: the line is able to process an extensive range of containers with round or rectangular bottoms and is able to process up to 200 containers/min.
What makes the top-loading case packer so versatile and reliable are the robotics developed for the end-of-line part: the pick-and-place head that places the vials in the case and the Gigacombi, a custom-built robot for the palletization zone.