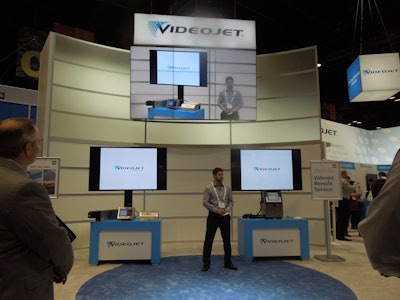
For the pharmaceutical industry, perhaps the most pressing topic is supply chain traceability, and the role serialization and DSCSA play.
At PACK EXPO Intl. 2016, Tim Kearns, Pharmaceutical and Medical Device Sales Manager, said the focus on serialization and track-and-trace has been on the transactional data between trading partners. “Supply chain traceability is paramount to preserving the integrity of pharmaceutical products and ultimately patient safety,” he noted. “But what about within the walls of your plant?”
Specifically, he referred to brite stocking, sterilization, refrigerated storage, and other internal processes that can cause breaks in the product flow, noting that many pharmaceutical operations do not have a continuous flow from bulk product to final packaging on a wrapped pallet. “You need to match physical flow of products with information associated to that drug to ensure product integrity. This is called ‘Internal Traceability’.’”
Kearns used the challenges of vial traceability within an organization. He said, “For injectable products in vials, the USP’s directive does not allow for visible print on the overseal cap (the most practical place to put a traceability code), it only allows for cautionary statements critical for medical practitioners, like ‘paralyzing agent’ or ‘dilute before use.’”
He says patient safety is a key objective here. Kearns asked, “So, how do manufacturers code vials in a practical way that can be used throughout their traceability process if it cannot be a visible code on the cap?”
One way to accomplish the task is to print on the ferrule side or skirt of the overseal, where Videojet has implemented lasers to mark the aluminum skirt, for example. Said Kearns, “The challenge with marking the skirt of the vial comes when you need to verify the product code. Inline verification, typically done at the packaging line, would require a multiple camera solution or a very special lens, but still a viable option.”
But the invisible ink option on the cap of the vial was the focus of Kearns’ presentation. This approach involves the use of Continuous Ink Jet (CIJ) printers and solvent-based inks. He said Videojet has two UV-fluorescing inks under development for this application.
Kearns described a customer application in which Videojet’s customer was using internal vial traceability codes. To meet the need for higher resolution, Videojet used the invisible that can be applied to vial caps and then read by a UV light for code verification.
“The objective of the project was to prevent product mix-up between the filling of the vial and the packaging line, as there was a break in the process for sterilization,” said Kearns “Working closely with our customer, there were tests performed offline, then online, before sterilization, after sterilization, and then finally at the packaging line where the reject/scrap was occurring. The results were better than expected. Our customer, using the 240x240 DPI code, was able to decrease reject rates.”