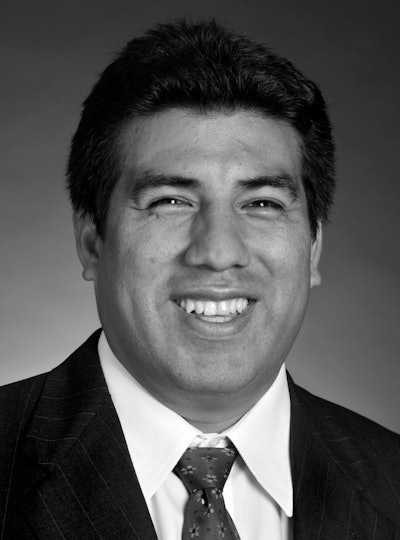
Ambient profiles must be a true representation of the temperature a shipping container experiences during transit from origin to destination sites. Failure to capture realistic temperature conditions in the supply chain will create inefficiencies and increase the risk.
Ambient profiles are defined by three elements: temperature, time and logistics steps. These elements (i.e. building blocks) are usually recorded in two groups (temperature and time and logistics steps and time). The first group, temperature and time, is recorded by an external temperature monitor while the second group, logistics steps and their start and end times (date and time), are usually compiled by the freight forwarder with the help of all the carriers and handling agents.
Today there are many suppliers of temperature monitors and adding temperature monitors to each shipping container is not only a common but also a recommended practice. Shipping containers may include one or multiple internal and external monitors depending on the objectives defined in the temperature monitoring strategy. The external monitor provides the first data group (temperature and time). The internal temperature monitor also records the temperature data using a predefined interval time and does not provide details about the logistics events (limited data) but it confirms the product stayed within the established temperature range.
Figure 1 shows an example of the temperature-time plot recorded by an external temperature monitor attached to the shipping container.
Note that the following assumption is made: the temperature that the monitors and the shipping container were exposed to is the same and to verify this assumption more than one shipping container and multiple monitor locations must be tested. Variations in temperature in different areas of the cooler or carrier’s vessel and variations in handling agents could lead to differences between temperatures of the external monitors. Also note that the ambient temperature recorded by the external monitor is not the reported weather data.
The logistics steps are usually defined in the routing or shipping route. The routing is the series of storage and distribution activities taking place during the transportation from origin to destination and which maintain a specific temperature range. Each logistics step has a start and end time as well as a maximum and minimum temperature associated to it. The second data group compiles the logistics step and the time but will not provide the temperature associated to each step.
Figure 2 shows an example of a routing.
When the results of the temperatures/time and logistics steps/time information are combined, a new graph is rendered, as shown in Figure 3.
The new graph shows the logistics steps and the temperature and time associated to each step. Temperature spikes (high or low temperature) are now linked to each step and can be managed to reduce the spikes. Figure 3 shows the temperature spikes are happening during the aircraft loading (i.e. tarmac time).
Understanding each routing is critical to building a profile because each logistics step has a potential impact on the temperature found during distribution.
For example, if a shipper has cargo to be moved from San Francisco to Milan (Italy) and tenders its cargo, the Freight Forwarder may present multiple routings for the same origin—destination lane.
Four routings for this origin-destination lane are: San Francisco to Milan via Amsterdam (SFO-AMS-MXP), San Francisco to Milan via Los Angeles (SFO-LAX-MXP), San Francisco to Milan via New York (SFO-JFK-MIL) and San Francisco to Milan via Dubai (SFO-DXB-MXP).
Each routing may have different logistics steps, duration, and external temperature based on the carrier’s cold chain program (facilities, operating procedures, etc). There is also a variation of weather temperature and depending on the time of the year the shipment is made, the routing will show different spikes. The better managed routing will show an ambient temperature less dependent on the weather temperature.
In my experience, I have found some the following practices to be useful:
1. Avoid the pre-conceived thought that summer and winter temperatures are the worst times for shipping. This statement had its origin in the assumption that the ambient temperature is the same as the weather temperature. Before making this assumption, one may test multiple shipments and carriers. The better control the carrier has, the less dependency between ambient and weather temperatures is found.
2. Long haul destinations are not necessarily the worst-case temperature scenarios. The worst case is defined by those lanes with less controlled logistics steps. Carriers have an opportunity to provide a service that will add value to the supply chain and can become a differentiator from their competition.
3. The profile should be based on the routes that are used most of the time (regular destinations). One-time events may be uncontrolled and create a profile with extreme spikes that could lead to an over-designed package.
4. If the Freight Forwarder decides to base the routing on cost or transit time alone, then routings will most likely change from shipment to shipment. These multiple routings with varying amounts of control might show inconsistencies with the data. One must manage the cold chain routes before deciding to build a profile and this requires a higher collaboration with the freight forwarder and carriers.
5. Rather than use the industry profile (e.g. ISTA) or a profile provided by a shipping container supplier, one should take the time to collect his/her own data and create his/her own profile. A profile with a small sample is better than a third-party profile.
6. Collecting ambient data does NOT need to be a time-consuming or an expensive project as it is often assumed. An over-designed container created without the correct data will be more costly in the long run or can induce temperature excursions due to the excessive amount of frozen gel packs.
7. A common practice is to extend the profile time till failure and collect data beyond the regular transit time. In my opinion, this practice adds very little value because it creates an over-designed container and will not only cost more but increase the risk of temperature excursions. If there is a delay in the routing, and a delay of more than six hours is expected, then the product should be placed in the controlled temperature warehouse.
The profile must be as accurate as possible and the first step is to build an accurate profile is to understand the logistics steps (routings). The logistics manager must collaborate with the freight forwarder, carriers, and consignees to put together a comprehensive routing. The next step is to measure and manage the ambient temperature to ensure the high risks areas are controlled. Finally, the shipping container design with the realistic ambient profiles can be executed. Creating ambient profiles is not a one-time event and they must be reviewed on a periodic basis as carriers and other logistics partners are making changes that will affect the ambient profile.
--Carlos Castro will speak at the Cold Chain Global Forum taking place in Sept. 30 – Oct. 4 in Chicago. Please download the brochure to learn more the event.