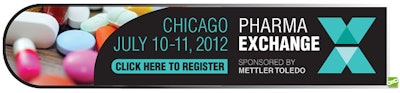
The complexity of serialization and its total impact on an organization was the focus of today's Pharma Exchange, a free, two-day seminar put together by Mettler Toledo.
(Editor's Note: With a small tabletop area and no sales pitch at the podium, this was a first-class networking event.)
"No doubt the U.S. is behind," said Elliot Abreu of Xyntek, Inc. "But lagging behind has its privileges. We have let the others pay the price to sample approaches and find what works."
What is true now, however, is if you have not started, you are going to miss deadlines for California-or be superseded by some Federal regulations. Either way, starting now with available standards, assessing and planning strategy, pilot testing, rolling out, and validating is a move that will position you for success in the global market.
Remember, California is the catalyst, but creating your own global supply chain serialization program is going to pay off with visibility into your operation like you have never had before.
"IT is the blood and heartbeat of any serialization project," said Abreu. The management of data tracked across an enterprise requires standards, methodologies, project ownership, and management from every discipline.
You have multiple, complex technology platforms-PLCs, vision, sensors, encoding, inspection and verification systems, all feeding information to complex IT layers-at device, line, plant, and enterprise levels.
Serialization requires input both at the planning stage and at execution including team members from IT, Engineering, Quality, Marketing, Label/Package Design, Supply Chain, and all partners. And training, offsite, totally focused on all possible impact points. is a terrific challenge.
Planning a complex project, in a complex environment, involving complex processes must have a structured approach incorporating program governance and project management where all stakeholders are in from the beginning.
Standardized policies, procedures-even standard information dashboards-communicate clearly stated goals to measure progress, allow for flexibility and change. You must balance resource allocation internally, define ROI, manage procurement and contracts, define scope and schedule events throughout life cycle.
Supply chain partners, CMOs, and CPOs must understand compliance is mandatory. If a warehouse has to buy a special scanner to read the new Japanese government mandated code*, they are going to have to make the investment to keep the business.
*Japan has recently updated its serialization requirements to replace the 2D data-matrix data carrier with the DataBar (a stacked linear bar code). This allows lower cost and more widely available linear scanners to be used. Many life sciences companies have focused on the data matrix and may not be prepared to support a variety of data carriers. (Editor's Note: This "hot off the presses" update comes from Bill Fletcher [email protected]).
One contract packager worried aloud about making the investment to allocate and aggregate serial numbers. (This is all that should be happening at the plant level, most agreed, the rest is an IT information challenge at the MES level.) But if they are not equipped with any electronic communication framework they will have to turn to Cloud providers who are offering these data packages.
Engineering, operations, and maintenance will not be happy to hear turning on a line set up for serialization will result in an initial 10% drop in OEE. It will eventually stabilize near 4%, but you never are as efficient.
Operators have to understand they can no longer take a carton off the floor to complete a case. Quality can no longer come out, grab a few samples, and disappear back into the lab. Rework stations have to be set up.
A pilot test has to be "end-to-end" and provide an assessment for improvement before rollout. It's a process.
There was much discussion about IT maintaining a sandbox-extra cameras, extra control systems-to test upgrades, emergency fixes, etc. Some even said you can't do a pilot on an existing line because you cannot take it out of production for the time required, so a sandbox with a whole line is advisable.
Change parts and maintenance are issues because the new camera supports a different software platform, not the one the serialization system was designed around.
Even facilities have to be altered in 20% of the cases to accommodate serialization-related space, according to Mark Hollowell, Director Barry-Wehmiller Design Group.
Hollowell said you know when a project is in trouble during the initial assessment phase where you meet resistance at the plant level where people basically tell you they are not interested in doing anything differently. Here management's buy-in and the realization that serialization is a wide-impact corporate challenge goes a long way.
Imagine having dozens of lines with dozens of pieces of equipment, from dozens of suppliers. Just getting those drawings is an 80-hour exercise. Who has the time? What else are they NOT doing now that they have been assigned to the serialization? You may have to hire extra personnel.
You even have to factor in return logistics. There are times where product is damaged and not readable. Who destroys what and where, how do you put an end to the "pedigree?"
Clearly, the IT challenge is enormous. No wonder pharmaceutical companies have put it off for years. Older pilots now may be obsolete.
If you are not planning right now, you will pay a higher and higher price for delay.
(Editor's Note: With a small tabletop area and no sales pitch at the podium, this was a first-class networking event.)
"No doubt the U.S. is behind," said Elliot Abreu of Xyntek, Inc. "But lagging behind has its privileges. We have let the others pay the price to sample approaches and find what works."
What is true now, however, is if you have not started, you are going to miss deadlines for California-or be superseded by some Federal regulations. Either way, starting now with available standards, assessing and planning strategy, pilot testing, rolling out, and validating is a move that will position you for success in the global market.
Remember, California is the catalyst, but creating your own global supply chain serialization program is going to pay off with visibility into your operation like you have never had before.
"IT is the blood and heartbeat of any serialization project," said Abreu. The management of data tracked across an enterprise requires standards, methodologies, project ownership, and management from every discipline.
You have multiple, complex technology platforms-PLCs, vision, sensors, encoding, inspection and verification systems, all feeding information to complex IT layers-at device, line, plant, and enterprise levels.
Serialization requires input both at the planning stage and at execution including team members from IT, Engineering, Quality, Marketing, Label/Package Design, Supply Chain, and all partners. And training, offsite, totally focused on all possible impact points. is a terrific challenge.
Planning a complex project, in a complex environment, involving complex processes must have a structured approach incorporating program governance and project management where all stakeholders are in from the beginning.
Standardized policies, procedures-even standard information dashboards-communicate clearly stated goals to measure progress, allow for flexibility and change. You must balance resource allocation internally, define ROI, manage procurement and contracts, define scope and schedule events throughout life cycle.
Supply chain partners, CMOs, and CPOs must understand compliance is mandatory. If a warehouse has to buy a special scanner to read the new Japanese government mandated code*, they are going to have to make the investment to keep the business.
*Japan has recently updated its serialization requirements to replace the 2D data-matrix data carrier with the DataBar (a stacked linear bar code). This allows lower cost and more widely available linear scanners to be used. Many life sciences companies have focused on the data matrix and may not be prepared to support a variety of data carriers. (Editor's Note: This "hot off the presses" update comes from Bill Fletcher [email protected]).
One contract packager worried aloud about making the investment to allocate and aggregate serial numbers. (This is all that should be happening at the plant level, most agreed, the rest is an IT information challenge at the MES level.) But if they are not equipped with any electronic communication framework they will have to turn to Cloud providers who are offering these data packages.
Engineering, operations, and maintenance will not be happy to hear turning on a line set up for serialization will result in an initial 10% drop in OEE. It will eventually stabilize near 4%, but you never are as efficient.
Operators have to understand they can no longer take a carton off the floor to complete a case. Quality can no longer come out, grab a few samples, and disappear back into the lab. Rework stations have to be set up.
A pilot test has to be "end-to-end" and provide an assessment for improvement before rollout. It's a process.
There was much discussion about IT maintaining a sandbox-extra cameras, extra control systems-to test upgrades, emergency fixes, etc. Some even said you can't do a pilot on an existing line because you cannot take it out of production for the time required, so a sandbox with a whole line is advisable.
Change parts and maintenance are issues because the new camera supports a different software platform, not the one the serialization system was designed around.
Even facilities have to be altered in 20% of the cases to accommodate serialization-related space, according to Mark Hollowell, Director Barry-Wehmiller Design Group.
Hollowell said you know when a project is in trouble during the initial assessment phase where you meet resistance at the plant level where people basically tell you they are not interested in doing anything differently. Here management's buy-in and the realization that serialization is a wide-impact corporate challenge goes a long way.
Imagine having dozens of lines with dozens of pieces of equipment, from dozens of suppliers. Just getting those drawings is an 80-hour exercise. Who has the time? What else are they NOT doing now that they have been assigned to the serialization? You may have to hire extra personnel.
You even have to factor in return logistics. There are times where product is damaged and not readable. Who destroys what and where, how do you put an end to the "pedigree?"
Clearly, the IT challenge is enormous. No wonder pharmaceutical companies have put it off for years. Older pilots now may be obsolete.
If you are not planning right now, you will pay a higher and higher price for delay.