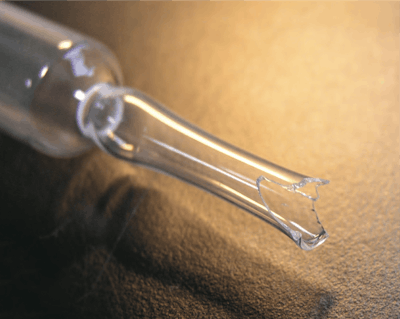
Patient safety is a primary concern for all who are involved in developing pharmaceuticals, their packaging components and their handling. There are many insights as to where safety can be improved; however, there are many variables that can impact product quality and, in turn, product safety. Recurring issues around product quality have been reported, with disputes between pharmaceutical manufacturers and packaging suppliers as to who is at fault. There are many factors that contribute to product quality, including particles, extractables/leachables and human factors. Yet, primary packaging defects are the more frequently cited causes, raising issues between the two parties. These defects are being classified differently on a global scale from company to company, creating major discrepancies within the pharmaceutical industry during quality decision-making processes. There is a clear need to identify and classify standard defects on a more uniform basis.
As product quality regulations become more and more stringent, pharmaceutical companies and their suppliers will have to expand collaborative efforts to achieve uniform and quality-based criteria for classification of defects. The pharmaceutical companies are ultimately accountable to regulatory authorities; however, the suppliers will also be held to the same expectations in ensuring the quality of their packaging materials by the pharmaceutical companies. The ultimate goal would be a situation in which packaging components do not require inspection when received by the pharmaceutical company, but rather, are subject to inspection once the pharmaceutical products are filled.
There are many elements that support meeting quality requirements, such as sampling plans, compendia, acceptance quality limits and other standards; however, a standardized quality criteria would be a building block to guide both pharmaceutical manufacturers and packaging suppliers to achieve the highest levels of quality. A clear guideline on classification of defects would help bring an aspect of the quality concerns to light. A regularly updated library of consensus-based classifications of defects by pharmaceutical manufacturers and suppliers would help reach conformance specifications and allow for organizations to better meet regulatory expectations. Although this is an ideal scenario, it is always imperative to consult with the appropriate regulatory authorities for agreement on strategies to identify and classify defects. Collaboration between the two parties should focus on increasing patient safety and meeting product and regulatory requirements on both ends. Quality agreements that are developed from consensus-based decisions between regulatory agencies, pharmaceutical manufacturers and suppliers can only improve the overall quality of the pharmaceuticals being developed. Small steps to improve the collaboration between parties involved in pharmaceutical development can lead to large enhancements within our industry.
Recognizing the need to provide consensus-based best practices for the identification and classification of elastomeric component and aluminum seal nonconformities, a PDA task force developed Technical Report No. 76 Identification and Classification of Visible Nonconformities in Elastomeric Components and Aluminum Seals for Parenteral Packaging. This report presents an approach to a quality decision-making process and provides consistent and standardized quality criteria that can be used by pharmaceutical and medical device manufacturers for the visual inspection of incoming elastomeric components and aluminum seals, and by suppliers for outgoing inspection.
In addition, PDA Technical Report No. 43, Revised 2013, Identification and Classification of Nonconformities in Molded and Tubular Glass Containers for Pharmaceutical Manufacturing: Covering Ampules, Bottles, Cartridges, Syringes and Vials, provides a foundation for developing an overall specification for molded bottles, vials and tubular glass containers. It presents best practices for identification and classification of visual nonconformities for glass containers.
For more information on these Technical Reports, please visit www.pda.org/bookstore.