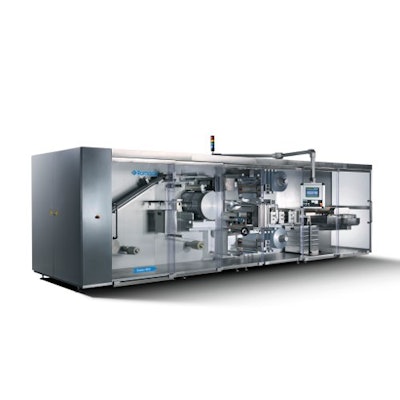
Romaco has developed the first Siebler StripTabsTM line for Indian contract manufacturer ANKUR Drugs and Pharma Ltd. This new technology is used to manufacture and package pharmaceutical orally dissolving strips. This innovative drug delivery system offers alternatives for pain treatment and hormone therapy.
Romaco has developed the first Siebler StripTabsTM line for Indian contract manufacturer ANKUR Drugs and Pharma Ltd. The system's innovative design was specially created for the production and packaging of pharmaceutical film tablets. For the first time, this novel drug delivery system will contain active pharmaceutical ingredients (API). Taken orally, the wafer-thin StripTabs™ dissolve on the tongue in seconds. This type of medication, which is based on a starch and polymer solution, is used in pain and hormone therapies, as well for treating erectile dysfunction. StripTabs™ are currently being considered as a carrier for over 600 different APIs.
“Our customers are very interested in taking the user-friendly film tablets,” says Purnandu Jain, Chairman of the Supervisory Board and CEO of ANKUR Drugs and Pharma Ltd., in explaining the reason for the manufacturer's considerable investment in StripTabs™ technology. “This innovative pharmaceutical dosage form has the potential to dramatically change and expand the landscape of traditional dosage forms.”
Close cooperation between ANKUR and Romaco
With three locations in Baddi and Daman, ANKUR Drugs and Pharma Ltd. has been one of India's leading contract manufacturers since 2003. The company, which was founded in 1997, currently produces and packages more than 400 different medications for the Indian, Asian, and African pharmaceutical markets. Its ongoing expansion in production capacity is also reflected in the close working relationship the company has had with the Romaco Group for the last five years. Currently, the Indian provider of pharmaceutical services is using more than 50 blister and strip packaging lines, cartoners, tube fillers, as well as aseptic powder filling lines made by the Karlsruhe packaging specialists.
The joint development of the Siebler StripTabs™ line marks the latest high point in the collaborative relationship between the two companies. “As a partner, we rely on Romaco's expertise in the area of pharmaceutical technology and manufacturing systems engineering,” explains Jain in Mumbai. “Our close collaboration during the design and construction of the StripTabs™ line showed us just how seriously our technological specifications were being taken and how successfully they were implemented.”
Innovative manufacturing and coating processes
Customized manufacturing and packaging processes are needed to handle the thumb-sized strip dosage forms, which are only 60 to 100 micrometers (μm) thick. First, the active pharmaceutical ingredient suspension is prepared using a homogenizing process on a vacuum processing unit made by Romaco FrymaKoruma. Directly blending in the APIs, right at the beginning of the process, results in extremely high dosing accuracy with extremely low active ingredient tolerances.
Using a complex coating process, the liquid is then applied with a thickness tolerance of only one micrometer to a high-precision substrate film. After being conveyed through several drying units, the coated strips can be wound into rolls. The rolled material with widths of up to 240 millimeters is transferred to a Siebler HM 2/500 heat sealing machine for further processing.
No cutting tolerances due to seamless die-cutting
The cutting and primary packaging of the StripTabs™ in peelable packages sealed on all four sides is done on the Siebler HM 2/500 machine. After unrolling, the coated substrate strips are first conveyed through the unit's precision cutting station. Here the film tablets are cut by a cylindrical cutting tool to the required dimensions of 20 by 30 millimeters leaving the carrier material intact. The use of this seamless die-cutting process results in zeropercent cutting tolerances. The process also ensures that the calculated product loss turns out to be comparatively low at below five percent. In the next step, the cut strips are pulled over a sharp-edged dispensing tongue where they become separated from the substrate film and are conveyed as individual units to the sealing area.
A shuttle system carries the individual film tablets onto the primary packaging film with a sealing width of up to 500 millimeters. The StripTabs™ processed in this way come to the HM 2/500's ten-line sealing process, which can reach a maximum packaging speed of 1,500 strips per minute. Sealed in light- and moisture-proof soft aluminum foil pouches, the StripTabs™ have a shelf life of up to three years.
Romaco has developed the first Siebler StripTabsTM line for Indian contract manufacturer ANKUR Drugs and Pharma Ltd. The system's innovative design was specially created for the production and packaging of pharmaceutical film tablets. For the first time, this novel drug delivery system will contain active pharmaceutical ingredients (API). Taken orally, the wafer-thin StripTabs™ dissolve on the tongue in seconds. This type of medication, which is based on a starch and polymer solution, is used in pain and hormone therapies, as well for treating erectile dysfunction. StripTabs™ are currently being considered as a carrier for over 600 different APIs.
“Our customers are very interested in taking the user-friendly film tablets,” says Purnandu Jain, Chairman of the Supervisory Board and CEO of ANKUR Drugs and Pharma Ltd., in explaining the reason for the manufacturer's considerable investment in StripTabs™ technology. “This innovative pharmaceutical dosage form has the potential to dramatically change and expand the landscape of traditional dosage forms.”
Close cooperation between ANKUR and Romaco
With three locations in Baddi and Daman, ANKUR Drugs and Pharma Ltd. has been one of India's leading contract manufacturers since 2003. The company, which was founded in 1997, currently produces and packages more than 400 different medications for the Indian, Asian, and African pharmaceutical markets. Its ongoing expansion in production capacity is also reflected in the close working relationship the company has had with the Romaco Group for the last five years. Currently, the Indian provider of pharmaceutical services is using more than 50 blister and strip packaging lines, cartoners, tube fillers, as well as aseptic powder filling lines made by the Karlsruhe packaging specialists.
The joint development of the Siebler StripTabs™ line marks the latest high point in the collaborative relationship between the two companies. “As a partner, we rely on Romaco's expertise in the area of pharmaceutical technology and manufacturing systems engineering,” explains Jain in Mumbai. “Our close collaboration during the design and construction of the StripTabs™ line showed us just how seriously our technological specifications were being taken and how successfully they were implemented.”
Innovative manufacturing and coating processes
Customized manufacturing and packaging processes are needed to handle the thumb-sized strip dosage forms, which are only 60 to 100 micrometers (μm) thick. First, the active pharmaceutical ingredient suspension is prepared using a homogenizing process on a vacuum processing unit made by Romaco FrymaKoruma. Directly blending in the APIs, right at the beginning of the process, results in extremely high dosing accuracy with extremely low active ingredient tolerances.
Using a complex coating process, the liquid is then applied with a thickness tolerance of only one micrometer to a high-precision substrate film. After being conveyed through several drying units, the coated strips can be wound into rolls. The rolled material with widths of up to 240 millimeters is transferred to a Siebler HM 2/500 heat sealing machine for further processing.
No cutting tolerances due to seamless die-cutting
The cutting and primary packaging of the StripTabs™ in peelable packages sealed on all four sides is done on the Siebler HM 2/500 machine. After unrolling, the coated substrate strips are first conveyed through the unit's precision cutting station. Here the film tablets are cut by a cylindrical cutting tool to the required dimensions of 20 by 30 millimeters leaving the carrier material intact. The use of this seamless die-cutting process results in zeropercent cutting tolerances. The process also ensures that the calculated product loss turns out to be comparatively low at below five percent. In the next step, the cut strips are pulled over a sharp-edged dispensing tongue where they become separated from the substrate film and are conveyed as individual units to the sealing area.
A shuttle system carries the individual film tablets onto the primary packaging film with a sealing width of up to 500 millimeters. The StripTabs™ processed in this way come to the HM 2/500's ten-line sealing process, which can reach a maximum packaging speed of 1,500 strips per minute. Sealed in light- and moisture-proof soft aluminum foil pouches, the StripTabs™ have a shelf life of up to three years.
Companies in this press-release