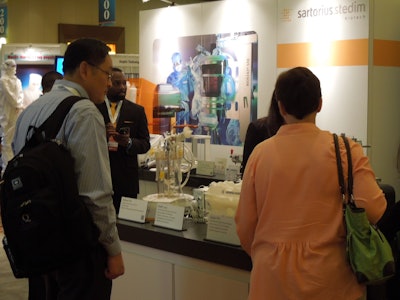
For years we’ve heard about the significance of packagers and their suppliers developing partnerships and building relationships. Apparently there remains work to be done, based on comments made April 15 at the 2013 Parenteral Drug Assn. (PDA) Annual Meeting in Orlando, FL.
During a track on “Innovative Approaches to Sterile Product Packaging,” Robert Swift, senior principal engineer at Amgen, said there was a need to better understand one another’s processes, and for manufacturers to learn about their suppliers and how they work with their commodity vendors. The more communication and understanding of how these processes work, the better. “There’s sometimes a lack of knowledge between packagers and their suppliers,” he believed. “When we don’t have that knowledge, we may not even know what questions to ask.” He urged packagers and suppliers to visit one another’s facilities as a way to improve relationships and business efficiencies.
Much of Swift’s presentation focused on plastic and glass container development for biologic parenterals. Testing methods are used to find defects. He recommended that in fill/finish operations, it’s wise to check if material scratches could be coming from the surface of conveyors in between different packaging machines.
The 2013 PDA Annual Meeting, “Modern Sterile Product Manufacturing—Exploring Best Practices and Seeking New Approaches,” included not only sessions, but also poster presentations and exhibits. An attendee list distributed at the show identified 743 total attendees (including additional exhibitor passes).
Following Swift, F. Andreas Toba, PhD with MEDInstill, addressed the “Correlation between Aerosol Bioburden and Surfact Contamination—Risk Analysis Fundamentals.” His conclusion and implications included the following:
• “The aerosolized bioburden is controlled and maintained after the initial charging of the chamber.”
• “A maintained and controlled aerosolized bioburden allows for correlation between time of exposure and bioburden on system surfaces. This generates and reproduces consistent and comparable data.”