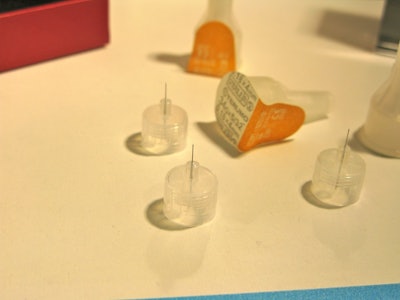
Responsible innovation is partly an effort to bring to healthcare packaging some of the sustainability emphasis that has been so prevalent in food and beverage the past few years. But it’s also about creating value, making decisions that are socially responsible, and ultimately finding ways to create a better world.
At the Sabic booth, for example, there was talk of two new grades of clarified polypropylene that will make it possible to produce lighter syringes. That will make them more economical, so their value proposition will be sound. But because they’ll be lighter, they’ll also add less solid waste going to the landfill, so they’ll be more sustainable and more socially responsible.
At the Sabic booth, Hery Randrianantoandro, Segment Leader Healthcare SBU Polymers, suggested that the spirit of responsible innovation could lead polymer suppliers to ask if they could play a bigger role in solving the ongoing problem of counterfeiting. “Maybe we can do something at the molecular level, for example,” he observed. “There are a lot of resources we bring to bear. We might also play a role in developing the new breed of packaging that will be needed as biologics continue to develop.”
Biologics were also covered in the expansive conference program that is part and parcel of Pharmapack Europe. In his presentation, Christophe Dehan (shown in photo) of Eveon noted that biologics now represent 50% of the drug development pipeline. But because of how difficult it is to rehydrate and administer many of them, they must be administered at point of care rather than by patients themselves in the home. But Eveon has developed Intuity Lyo, a controlled electronic device that allows patients to rehydrate and administer these complex treatments with perfect accuracy in the comfort of their own homes—without professional intervention.
Shortly after Dehan’s presentation, Dr. Elisa Le Floch of Clariant Healthcare Packaging described Tubairless. A combination of an air chamber and a soft plastic pouch sealed within a flexible tube, Tubairless is a dispensing system that helps protect sensitive cream-based formulas from the adverse effects of outside air. Pumpart originally developed and commercialized the concept for use in the cosmetics field. Now Clariant and Pumpart are partnering to bring Tubairless to pharma.
Many medicated creams, ointments, gels, and pastes are susceptible to moisture gain or loss as well as certain types of contamination. The tube’s internal pump prevents air-intake and product flow-back during dispensing, reducing the ingress of unwanted elements that can contaminate the contents. Protection can be further enhanced by integrating multiple protective barrier or active layers into the package.
According to Le Floch, this concept appeals to both healthcare providers and patients. It not only helps address preservation issues as formulators look for ways to reduce or eliminate preservatives from formulations, but it can also improve patient compliance with a user-friendly experience. Among its more attractive characteristics is that it retains its original shape through its useful life.
Among the more energetic presentations of the Thursday sessions was the one given by Bernard Vrijens, Phd, of MWV. Patient adherence was his topic, and he was quite clear that packaging can do a lot to improve it. Smart packaging, specifically, can go a long way, and Vrijens described a number of clinical studies using MWV’s smart packaging system, the MEMSCap. Fitted with integrated microcircuits, the child-resistant MEMSCap records the date and time whenever a patient opens a vial. The MEMSCap offering includes two options, TrackCap® and SmartCap®, both of which wirelessly transfer dosing data when used in conjunction with a MEMSCap reader. SmartCap also features an LCD readout that displays the number of doses taken in the past 24 hours and the hours elapsed since last dosing. Both options work with standard vials in a range of sizes.
The consensus at Pharmapack is that smart packaging technology like this will soon begin moving from purely clinical research to more commercial and consumer-facing applications. A key driver behind this trend will be the simple fact that new drug products now emerging, many of them biologics, will have price points that are simply jaw-dropping. Both the people who make such drugs and the ones who prescribe them are going to want to know if patients are adhering to these prescriptions. Smart packaging that collects and communicates adherence behavior can give them this valuable data.
A key point emphasized by Vrijens is that adherence needs to be managed. “It can no longer be viewed as a patient problem,” he observed. The entire healthcare value chain must step up, and that includes packaging. “Packaging can help with cuing, it can help establish routines,” Vrijens told his Pharmapack audience. “Adherence packaging helps patients in their medication journey.”
And what about helping healthcare professionals administer drugs, parenteral drugs in particular? That was the subject of a presentation by Ralf Kunzi of Neopac AG. Neopac’s Fleximed is a range of transparent, flexible medical tubes that offer an intelligent alternative to glass vials in the area of parenteral packaging. According to Kunzi, drug prep requires seven steps when a syringe is filled from a conventional glass crimp vial. With Fleximed, only four steps are needed.
All materials utilized for manufacturing the new Fleximed® tubes comply with the highest demands of the pharmaceutical industry. Free of silicone oil and tungsten, this primary packaging format was designed specifically for parenteral drugs. All the tubes are produced from a transparent lamination with excellent barrier properties, and they can be gamma-sterilized. They are produced under fully qualified clean room conditions in Switzerland.
One note in closing: Part of the Pharmapack program on Wednesday was the announcement of the annual Pharmapack Awards, first launched in 1997. This year two awards were announced. In the Medical Device for Diagnostics category the winner was Eyeprim, which facilitates biomolecular analysis of ocular surface pathologies. It was developed by Opia Technologies and Groupe JBT. Winning in the Quality of Life category was Nanopass 34, the World’s thinnest pen needle, which was developed by Japan’s Terumo and is notable because it minimizes discomfort or pain caused by injections.