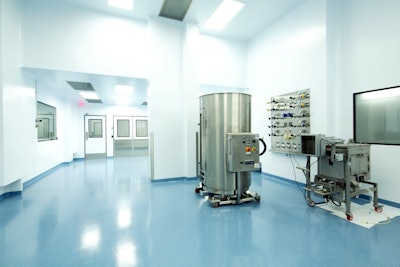
It goes without saying that upgrades during a manufacturing shutdown pose less risk as there are no products being produced, but there are instances when it is critical to expand capacity or modify functionality while maintaining some processing. For example:
-
Manufacturers upgrade certain areas while maintaining process operations on adjacent lines
-
Companies reconfigure equipment or add modular, flexible capabilities for the future
-
New or established manufacturers increase capacity incrementally while keeping supply on the market (and revenue flowing)
As George Wiker, Executive Director at AES Clean Technology, Inc.®, explains, these upgrades are a challenge for a variety of reasons. It is critical to maintain control of production and changes—and demonstrate proof of control—while keeping the involved workers and the products safe.
It is also important to note that a company will need to revalidate any system modified during a facility change, and the extent of the change may also require a re-inspection by the FDA.
1. Anticipate that changes will be implemented in the base building design.
During the master planning and concept design, review a series of conditional (if/then) statements to understand what changes may be required. For example, if a company knows that they will move equipment or change capacity, then they should put in knockout panels early because it is easier upfront. (A knockout panel is a section of wall that can easily be removed without much work or demolition, that can also be quickly reinstalled.) Wiker says to consider the following features:
-
Knockout panels to connect one space to another, or move equipment
-
Removable walls
-
Reconfigurable modules
-
Utility capacity to support the modification of a space
Utility capacity cannot be overlooked during the planning stages. “If you go to expand manufacturing capacity, and you don’t have the utility capacity to support that, you’re in trouble,” he warns, adding that some companies have determined it is worth adding 15-30% capacity to HVAC systems ahead of time, which comes at a very low relative cost.
2. Develop and implement a clean construction plan, including protocol(s) and change control methodology.
Wiker suggests working closely with facility, quality and compliance personnel early in the project to identify the development, and any potential impact to ongoing operations. This is an interactive and iterative process, as comments from different groups need to be reviewed by everyone involved.
Project planning becomes more critical for cleaner spaces, so ISO classification of rooms and adjacent spaces must be considered.
Changes should be implemented according to industry standards on clean construction, including ISO Standard 14644 on Cleanrooms and associated controlled environments (Part 4 covers design, construction and start-up). He suggests that protocols should not be overly complicated, instead having them reference a document like the execution plan that has more granularity. If equipment is being relocated, develop a Moving Protocol to verify that the equipment is currently performing as expected and that it can be disconnected and reconnected reliably and predictably. (A Moving Protocol is an abbreviated Installation Qualification (IQ) and Operational Qualification (OQ), and includes a step-by-step procedure to disassemble the equipment and move to expedite requalification once it is relocated.)
Contractors must be trained on the aspects of clean construction, including quality practices, gowning and what construction functions to avoid. “It’s difficult to get contractors to work in this context. They have to have a different mindset,” says Wiker. “There’s no fabrication in certain areas, tools have to be clean. It’s always a challenge when you think about the people working in this environment.”
Additionally, you should develop a formal monitoring plan and document what changes you will make and how, as well as what materials you will use to mitigate the risks. It takes a considerable amount of planning. Wiker says, “One renovation may take three months, but the planning takes three months, too.”
3. Install methods to maintain control and monitor conditions.
There are various ways to separate manufacturing from the construction area, including plastic barriers like ZipWall® and TuffWrap®. You should also create a negative pressure in the construction area using exhaust fans. These efforts should be monitored with dedicated monitoring devices to ensure conditions remain favorable.
4. Develop a detailed execution and construction logistics plan.
The plan should include documentation of temporary barriers. Personnel access and egress (if impacted) should be clearly explained, as well as access for contractors. Concessions should be made for materials and staging areas, and all involved parties should understand safety factors such as fire safety and suppression. The fire sprinkler system should remain online during renovation, but if you are making modifications that affect sprinklers, you may need to install a firewall to ensure safe operations at all times. Monitoring devices—alarms and security systems—should be closely watched.
It is also important to decide which party is responsible for the barrier integrity once it is installed. In some cases, the contractor sets up the barrier, installs controls and monitoring, and then hands responsibility off to manufacturing or a third-party compliance group.
Wiker suggests hiring certified contractors to build modular facilities. It may not be as important outside the cleanroom, but if you are retrofitting pass-throughs to meet EMA conditions, contractors must gown up. “We’ll often prequalify the contractors,” he says.
Case Study: Cell Therapy CMO
Wiker has seen success implementing changes at a number of pharma and healthcare companies, creating sub-compartments or building additional suites after initial manufacturing had begun.
AES Clean Technology, Inc. recently completed a challenging project for a single-use, continuous processing facility. The client thought they might eventually create a tabletop or more efficient process, so they wanted flexibility to change in the future.
The client, AES Clean Technology, Inc. and G-Con designed a 20,000-sq-ft facility—in essence, a large box—with dedicated pods for steps such as solution preparation, drug product production, etc. The core processes themselves are standardized, and the pods allow the client to have a great degree of control over upstream or downstream changes.
The future of modular processing brings new challenges, such as pods with GMP critical utilities. If a pod with a hot Water for Injection (WFI) system must be relocated, there must be a detailed plan for pulling out the pod and keeping that system up and running. As manufacturing technology evolves, companies will rapidly change systems with utility hookups to meet demands.