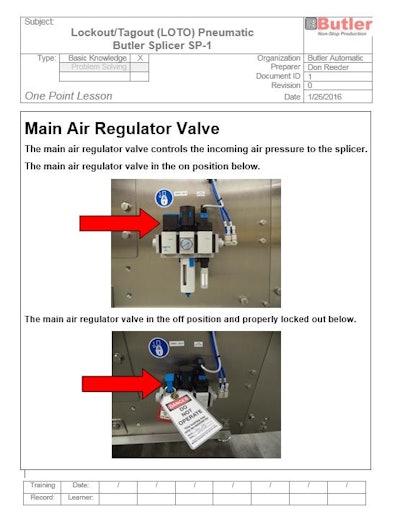
Proper maintenance of packaging equipment is critical to minimizing downtime and keeping costs low. This article will discuss tips for how to best maintain your packaging line machinery. With the right maintenance strategy, an appropriate inventory of spare parts, and timely upgrades in addition to support from an expert vendor, you can drastically reduce unplanned downtime, keeps costs low, lengthen the service life of your machinery, and maximize profits. When best practices are followed, even companies with minimal dedicated maintenance staff can reap these benefits and optimize packaging line operation.
1) Utilize preventative maintenance strategies…
The most basic maintenance advice is to create and adhere to a preventative maintenance schedule. Preventive maintenance tasks are conducted by qualified maintenance personnel, such as those with electrical or mechanical skills, on a preset schedule. Some tasks may need to be scheduled on a monthly, quarterly, or even annual basis, but the most important aspect of a preventative maintenance schedule is adherence to that schedule.
These timed maintenance activities, such as checking and replacing wear components, lubricating machinery, and more, are designed to prevent issues before they even occur. The value of preventative maintenance lies in being able to plan downtime and necessary materials, rather than being caught off guard when a component fails.
These tasks often require a more in-depth set of skills (and often more specialized tools) than possessed by the average machine operator, and so dedicated maintenance personnel should perform them. However, when paired with autonomous maintenance strategies – which I’ll say more about in a moment – a small, dedicated maintenance staff can manage a relatively large packaging operation, because the need for emergency maintenance is reduced and less-skilled, routine tasks are performed by machine operators.
2) …And autonomous maintenance strategies
The best maintenance strategy is one that combines preventative maintenance schedules, as described above, with autonomous maintenance. Autonomous maintenance tasks are checklist-based, and focus on basic cleaning and inspection routines being performed by machine operators. In the kind of world-class manufacturing environments that employ both preventative and autonomous maintenance strategies, machine operators are not just expected to operate their equipment. Operators are the experts about their machinery, and are the first line of defense as far as maintenance is concerned.
In these kinds of environments, operators are trained to understand the machine they’re running to a level where they can conduct basic cleaning and inspection tasks to maintain the equipment. In doing so, they can help the company and specifically, the maintenance team, to diagnose performance issues. An operator is at their own machine consistently, and so if something changes – such as noise, speed, undesirable motion, etc. – they are able to detect issues long before a scheduled maintenance visit would.
Operators have checklists of tasks they are responsible for; typically, these tasks must be performed once a shift, day, or week. They are trained to perform the various tasks with simple visual cues. These training visuals describe exactly what operators are expected to do, often showing the necessary tools and expected outcome. For example, operators who are expected to clean a machine component once a day receive training images with what cleaning supplies to use and what a clean component looks like.
Some lines have both autonomous and preventative maintenance plans in place, and are specifically designed to allow access to critical inspection and cleaning points without the need for tools or specialized skills.
Though preventative and autonomous maintenance tasks are often simple, they can forestall the need for larger, more time-consuming maintenance. Additionally, operators are often able to catch problems before they get out of hand, leading to shorter, less involved and less expensive maintenance or repair.
The best manufacturing and packaging companies in the world make use of the knowledge and skills of maintenance personnel in scheduled, preventative maintenance, and of the experts running each machine in autonomous maintenance, in order to avoid unplanned, costly repairs. The benefits of pairing autonomous and preventive maintenance strategies are an increase in planned maintenance over unplanned, maximized equipment availability, and the ability to forecast production capacities and maintenance budgets with greater precision.
3) Plan to replace wear components and critical spare parts
It is extremely important to have a plan in place to replace wear components, which are expected to wear out from repeated use of the equipment, and critical spare parts, which cause significant downtime when they fail. Ideally, manufacturers have these spare parts as inventory so that they can replace them immediately if they fail. In many manufacturing facilities, the downtime from waiting even a single day for a part can be extremely costly, and so manufacturers should plan to be able to replace highly critical components at any time.
Of course, manufacturers and packagers are also concerned with the funds and space that are tied up in extensive parts inventory. You should consult the manufacturer of your equipment about a list of components that are necessary to keep on hand. Level of inventory required is in part based on the stress on the line, and so each manufacturer’s needs are different. Industry leading manufacturers will continually analyze their customers’ needs for these components, and refine the necessary level of parts inventory for each customer to optimize it for their specific needs. These manufacturers will also maintain strategic inventories of recommended spare parts, so that they can support both planned and emergency component replacement needs.
Leading equipment manufacturers also offer tailored service agreements that synchronize with customers’ preventative maintenance programs in order to ensure maximized line uptime. These service agreements include pre-planned visits from qualified field service technicians, who can inspect equipment, replace any necessary wear components, and train operators and maintenance teams. Making use of manufacturers’ tailored service agreements can help to optimize spare parts inventory, and to ensure consistent, reliable equipment operation.
4) Choose a manufacturer who can help in a pinch
This recommendation factors in to all three of the previous recommendations as well, but is of course important in its own right. When you purchase packaging line equipment from industry-leading manufacturers, you are likely to get the kind of service and support you need to keep your line operating smoothly. Look for suppliers that run robust phone support (ideally 24/7) and field service operation. Some companies have field service technicians strategically located around the world to support the customer base, and are ready to visit manufacturing facilities to address any needs customers may have on an emergency or planned basis.
This is the service most frequently requested by customers, especially those with less robust maintenance strategies or with minimal maintenance personnel, regardless of company size. Support provided includes electrical and mechanical support, emergency service when equipment is down, emergency spare parts provisions when customers don’t have the appropriate inventory, and training. In providing this service, manufacturers help to ensure that customers can maximize production uptime, even in the event of an emergency.
It is also important to choose a manufacturer who can provide installation and training in order to ensure vertical startup of the production line with the new equipment. Field service technicians are ideally integration specialists who are trained to quickly resolve any issue on site during installation, including meeting the training needs of both maintenance and production personnel. Qualified manufacturers also participate in customers’ Factory Acceptance Testing (FAT) and Commissioning, Qualification and Verification (CQV) processes to ensure that they are delivering equipment that leads to a high quality and reliable process.
5) Plan for upgrades
The final key consideration for effectively maintaining a packaging line is to plan to upgrade equipment software and hardware periodically in order to avoid obsolescence. Typically in electronic control and computer systems, both hardware and software become unsupported at some point. When you plan ahead you will not be taken by surprise in the event of component obsolescence or software upgrades. This planning can be integrated into your annual maintenance planning and can be supported by leading manufacturers that continually improve and update their machinery, as well as proactively address the obsolescence issues.
Conclusion
Utilizing a mixture of pre-planned preventative maintenance and operator-level autonomous maintenance strategies will place your manufacturing and packaging lines at the head of the pack where equipment performance is concerned. Additionally, planning a strategic parts inventory, upgrading components when necessary, and relying on a world-class equipment manufacturer for service and support are critical components of a maintenance strategy. Highly effective maintenance strategies can help you to avoid unplanned, costly repairs, increase planned over unplanned maintenance, maximize equipment availability, and increase your ability to precisely predict production capacities and maintenance budgets.