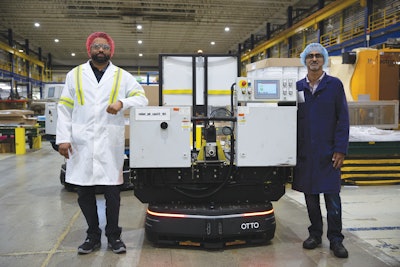
Mauser Packaging Solutions is a global packaging supplier with more than 180 facilities worldwide. At its 206,000-sq-ft Langley, British Columbia, Canada location, the company manufacturers pails and accompanying lids from 1 to 13 gal in size, among other packaging supplies. Large, branded food CPG customers, including Stahlbush Island Farms in Oregon and Saputo Cheese in Illinois, among many others, use these pails for food product applications.
But Mauser’s existing, traditional autonomous guided vehicle (AGV) system didn’t meet the required uptime and throughput to run a 24/7 production.
“The main issue with the legacy AGV system was a weak battery system that was operating using two sealed marine batteries, and an antiquated control/navigation system with scales and obsolete replacement parts,” says Wojciech Tymczak, corporate automation engineer for Mauser Packaging Solutions/North America Small Pack Division.
So, the company turned to autonomous material handling technology by way of an autonomous mobile robot (AMR) to trial at the 140- employee Langley facility. Mauser selected an OTTO 1500 AMR, by OTTO Motors, for this application in part because the unit features a long battery life that runs continuously for 13 hours on a single charge.
“OTTO came to mind because of safety concerns [with traditional forklifts] that we’ve had in the past. Plus, finding people has been very difficult because we’re a 24/7 operation,” says Dinesh Naidu, plant manager at Mauser’s Langley location. “When the OTTO was first introduced to the Langley facility, it was the first opportunity for us to get into something that probably nobody’s ever done before.” At the Langley facility, Dinesh Naidu, plant manager (left) and Dilip Bhulabhai, technical manager, saw immediate production and safety improvements. Mauser Packaging has since expanded the program to include its Oakville, Ontario facility.
Two major selling points were the vehicle’s 1500-kg payload and the battery system based on the latest LiFePO 4 lithium ion chemistry. The battery monitoring system (BMS) enables the vehicles to operate for up to 13 hours. on a single charge. Without going into technical details, Tymczak says the rapid charger makes the charging cycles transparent to operations.
“Mauser values innovation because we want to be the leader in the plastics manufacturing industry,” adds Dilip Bhulabhai, technical manager at Mauser. “The OTTO arrives to the [pack] station, connects with the pack station and transfers the package onto [the OTTO], and then drives back to the drop-off station where it transfers onto the wrapper/strapper line.”
The entire communication system for the new AMRs was designed, built, and integrated using Banner wireless sensors and controllers. The system integrated flawlessly with the OTTO Fleet Manager and the plant infrastructure utilizing the plant’s existing secure WiFi network
Programming and validation took approximately 12 weeks, including training of the key personnel across all production shifts. The new system was integrated into the production system utilizing the existing pack-out station from the legacy system, making the training more straightforward for the operators already familiar with the tasks surrounding the preparation of the loads and interaction with the autonomous vehicles, according to Tymczak.
And after introducing the OTTOs, Mauser leadership didn’t have to worry as much about people getting hurt on the job.
“In the last few years, it became apparent to us how important that was,” Naidu says. “And the job that the OTTO’s doing now is basically the work of three people, plus an additional two forklifts. It definitely helps us out to have that money spent somewhere else… Now, OTTO delivers safety, reliability, and productivity, 24/7.”
Bhulabhai was pleasantly surprised by the ease of use with the system, finding that it was easy to understand and navigate. And because the units worked so well in Langley, Mauser decided to expand and bring the OTTO units to its Oakville, Ontario, Canada plant in 2021.
Today, Mauser employs OTTO 1500 AMRs at both its Langley and Oakville facilities. While supporting Mauser’s 24/7 operation, OTTO AMRs now safely work alongside human operators to move plastic rigid containers from the conveyor to the stretch wrapper. The results speak for themselves, Mauser leadership says. At the Langley facility, three laborers were re-allocated to higher value-added roles, two additional forklifts were obviated, and the location enjoys improved safety by reducing manual forklift traffic. A pallet of pails are transported toward stretch wrapping operations. Mauser Packaging’s Oakville facility saw a 600% throughput improvement with the new AMRs over legacy AGVs, largely thanks to the OTTO’s fast, long-lasting charge.
Meanwhile, the Oakville facility was able to improve uptime, and enhanced throughput by a whopping 600%.
“The 600% throughput increase reflects the increase in the number of missions the new system completes vs the legacy,” Tymczak says. “The decommissioned AGV system completed about three to four tasks before going to the charging station, where it spent 25 to 30 minutes to charge enough to complete another three to four assignments. The OTTO system can run continuously for up to 13 hours. The single vehicle can complete up to 36 missions (three hours of run time) before going to the charger at about 70% of the charge. The legacy system completed only three to four tasks before dropping to 15% of the battery level. So, the 600% figure is based on the number of total missions a vehicle completes before going to the charger during regular operation and not the OTTO’s max 13 hours run time.
“No other AGV or AVR offered us the same uptime and productivity,” concludes Tymczak, who advises that a dedicated plant team working closely with the OTTO deployment group is key to a successful deployment. PW