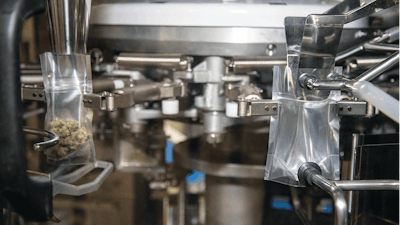
Since it was founded in 2011, Harvest Health and Recreation Inc. has grown steadily to become one of the leading growers and producers of cannabis products in the U.S. Headquartered in Tempe, Ariz., it currently grows approximately 80% of the cannabis it sells, and has production facilities and retail outlets in eight states, with plans to be in 13 states by the end of 2020.
This strong growth has coincided with dramatic changes that have taken place in the cannabis products industry itself over the same time period. What is now viewed as a significant industry grew out of what was essentially a widespread loose collection of informal businesses. The industry now seems to stand at a turning point, waiting for federal regulatory approval on one hand and even more consistent social acceptance of both its medical and recreational products on the other.
Meanwhile, as happens when markets change dramatically, some companies rise faster than others, often due to their commitment to meeting the demand of the changing marketplace. Growing rather quickly from a small to a large operation meant Harvest had to make critical decisions, including about integrating automated systems to benefit from the advantages the new equipment could offer. Investments based on continuing growth can be risky. Harvest based its investment on considerable research into getting the equipment that would do exactly what it needed given the challenges of the products it was processing and packaging.
Cannabis handling and packaging challenges
Cannabis plants present specific handling challenges. The full plants come directly from growing fields or greenhouses to Harvest facilities. They have a high moisture content that prevent them being processed immediately, so the first stage in processing is to dry the plants. This is done much the way it was done at earlier home-based cannabis operations, by hanging the plants by their roots. After some degree of drying, the flower, also called buds, are harvested from the plants and placed in food-grade 5-gallon buckets. They are kept in a dry environment to dry further, until they reach an acceptable level of moisture content.
The first step following harvesting the buds is to pass them through a trimming process to remove small leaves and create a more attractive-looking bud. Depending on product quality, volume, and other factors, this may be done by hand. But for the volume of buds that will be machine-packaged, Harvest uses a trimming machine.
The packaging process begins with adding cannabis buds to the Eriez infeed conveyor to the weigher.
Trimmed buds then go through an additional drying process, called a “perfing” step, once again in 5-gallon drums in a humidity-controlled room to achieve the exact desired level of moisture. It is at this point that another challenge arises: the dried buds are very light in weight and (as natural products often do) vary widely in size from plant to plant and even within each plant. Now, Harvest has to prepare them to be packaged in consistent weights from package to package.
The “processing” of the cannabis buds consists of sorting them by size and weight, and, when necessary, trimming the larger buds to obtain package consistency both in weight and number of buds. Once this is done, buds are packaged in pre-labeled transparent flexible plastic pouches, which means the buds will be visible to the customer and must look fresh and appealing, like any packaged natural product.
Finding an option to hand sorting and filling
Until 2019, these parts of the operation–sorting and weighing the buds, then packaging them in pouches–was done manually. From nine to 12 employees sitting around a large table would sort the buds, handling them gently, then weigh and place them in the pre-labeled flexible pouches for sealing and case packing. This process would go on five days a week to meet market demand. As demand varied, the number of workers might vary, but only slightly.
As the wider packaging industry had experienced early in its own development, manual labor has two critical limitations: it is slow and produces inconsistent packaging results.
Over the years it was in business, the cannabis industry began to evolve from a diverse, small-producer collection of operations into a more centralized industry. This has magnified manual labor’s limitations for Harvest. New forces came into play as demand grew and productivity became more essential. It became clear, for example, that a mature cannabis industry would face stricter regulation, especially with potential federal involvement.
In the summer of 2019, Shawn Sabo, Harvest Vice President of Manufacturing, began putting Harvest’s plan to automate its production operation into action by exploring equipment options for parts or all of its sorting and packaging process.
“We shared a detailed brief of what we wanted to accomplish with Denver-based equipment supplier and integrator Right Stuff Equipment, who we had worked with previously and who knows our operation well. They researched a variety of the types of equipment we would need and identified the systems they thought would offer the most effective solutions. Then we visited a number of packaging facilities where we could see that equipment in real-time action. From those systems, we chose what we felt would work best for our specific needs.”
The multi-head Ishida weigher accurately weighs buds before dropping them to the pouch filler.
Automating the pouching operation
The resulting automated system, now operating at the Harvest facility in Flagstaff, Ariz., consists of an Eriez infeed conveyor and an Ishida multihead weighing system positioned on a mezzanine above a General Packer GP-M3000 automatic pouch filling and sealing system provided by Massman Automation Designs LLC, General Packer’s exclusive distributor in the U.S.
“The advantage that the Ishida weigher gives us,” says Dennis Schum, Harvest’s Senior Director of Extractions, “is that its 14 weighing heads can handle the variability of the bud weights more quickly and more accurately than our manual workers, and deliver more consistent weights to each pouch, all while handling the buds gently.”
Once weighed, the buds are dropped into open pouches held in the GP-M3000 system below, which indexes through ten steps as it fills and seals the pouches.
“This is the heart of the system,” Sabo says. “The GP-M3000 packages the buds smoothly and quickly, and gives us the package weight consistency we need.”
Preprinted branded pouches enter the system, are opened, filled, and then shaken by vibrators to settle the lightweight buds into the pouches. In the final steps, air is Nitrogen-flushed from the pouches and they are heat-sealed, cooled, and discharged from the system. The 10 stages of the GP-M3000 include several “spare” steps that provide for future production expansion or the addition of new functions. The filling system can fill from 15 to 65 pouches/min, depending on bag size and product volume.
A Harvest full color brand label has been applied to each pouch before it enters the system, covering the front face of the pouch and carrying the brand identity, individual product flavor, and weight for the product. As Arizona regulations allow, the back of the pouch remains clear, letting shoppers see the buds.
Once filled, pouches go to an offline ADCO case packer, where they are packed in paperboard cartons that are prelabeled with brand identity and have windows that enable the product pouches to be seen. Cartons then go into corrugated cases that convert to displays in Harvest’s retail outlets.
This automated operation has now been operating successfully at the Harvest Flagstaff facility for approximately six months. Sabo has been doing a comparative analysis to determine the benefit of investing in the machine system versus continuing to fill pouches by hand.
“I am continuing to weigh the relative costs,” he says, “but what the numbers show so far is that running the automated system only one day a week with three employees is more cost-effective than doing manual filling with an average of nine people working five days a week, even when we include machine operating costs and maintenance.”
“And,” he adds, “while the investment in the machinery is a finite cost, the labor cost is open-ended and would be likely to increase as volume increases.”
Future growth
The efficiency of the automated production line operating in Flagstaff provides significant room for increased production. In addition, Schum points out that the system was designed with an oversized mezzanine, allowing space to fill a future jar packaging line that would sit beside the current GP-M3000, increasing the capacity for jar packaging. Harvest has also installed a similar GP-M3000 pouch filling line in its Maryland facility to replicate the Flagstaff packaging benefits there. That line is not yet commissioned, but is expected to come online in 2020.
Dennis Schum, Harvest House's engineer, with a sealed branded pouch of buds.
The cannabis products industry is still early in its evolution into an established, thriving industry. There is an air of expectancy in the plans and investments that many companies are making. Should federal regulatory approval be forthcoming, for example, the entire industry structure could change virtually overnight.
But in the meantime, as with Harvest, individual companies in the industry cannot stand idle as current product demand increases and more efficient automated product handling and packaging systems are clearly going to be required to meet new production quotas. Those that will thrive in this changing industry will likely be those that decide to invest in equipment that will both enable them to meet current demand and simultaneously lay the groundwork for a successful future in a mature industry. PW