Accelerated aging test tips
There exists "a great deal of misinformation" when it comes to accelerated aging of medical device packaging, said Curt Larsen of Spartan Design Group, LLC (952/380-1458), at the January 28 MD&M (Medical Design & Manufacturing) West Medical Device Packaging Conference in Anaheim, CA.
Feb 14, 2008
Break out of the ordinary: see what’s new in life sciences packaging
At PACK EXPO Las Vegas, you’ll see machinery in action and new tech from 2,300 suppliers, collaborate with experts and explore transformative solutions. Join us in September to experience a breakthrough for life sciences products.
REGISTER NOW & SAVE!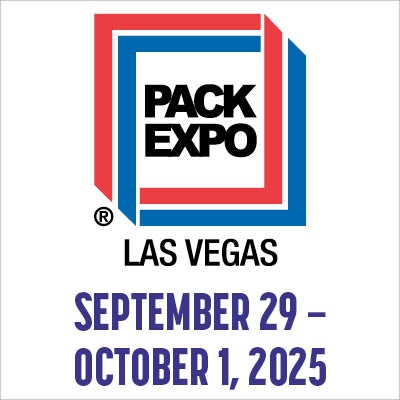
Pharmaceutical Innovations Report
Discover the latest breakthrough packaging technologies shaping the pharmaceutical sector. This report dives into cutting-edge innovations, from smart containers that enhance patient safety to eco-friendly materials poised to transform the industry’s sustainability practices. All from PACK EXPO. Learn how forward-thinking strategies are driving efficiency and redefining what’s possible in pharma packaging.
Learn More