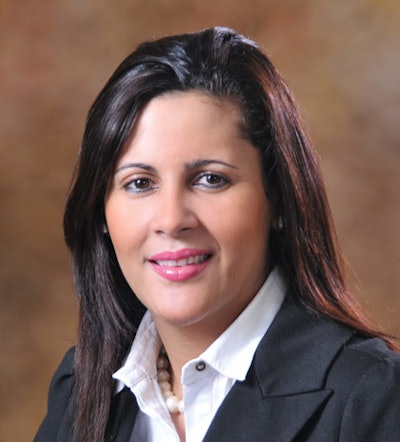
These requirements provide adequate guidance to perform validations, such as Installation Qualification (IQ), Operational Qualification (OQ), Test Method Validation (TMV), and Performance Qualification (PQ). Active engagement and cross-functional support are required to effectively execute these validations. Another important aspect is process assessment to understand critical packaging equipment parameters.
During the planning of required validation activities, a recommended practice is to standardize the approach. Different tools are available in the market, such as DMAIC (Define, Measure, Analyze, Improve and Control) and PDCA (Plan, Do, Check, Act). In addition to these tools, a structured and documented plan of deliverables, resource commitments, target dates, and performance metrics is essential to monitoring execution against planned activities. Regular reviews ensure cross-functional collaboration/inputs, technical support, adequate support, consistent progress, and management oversight.
Key elements and clear scope position a team for success. A team with clear process and product specifications, adequately defined targets, proper leadership and guidance, resources, and technical support are placed under conditions to achieve expected results. Identifying essential validation work content maps the need for and engages the different subject matter experts. A robust plan builds a cross-functional agreement to satisfy both internal and external customer requirements.
Process assessment understands and characterizes the packaging process and identifies critical parameters and operating ranges (this is a critical step within process validation activities). Developing a process map unmasks the differences in process steps, and critical inputs and outputs. Examples of some tools commonly used include Supplier Inputs Process Outputs (SIPOC) and Critical to Quality (CTQ) from the process perspective. The output of these tools determines uncontrolled variables (noise of the process) and control variables for variable range management.
Prior to validation and process assessment, test methods must be verified using statistically valid techniques, such as R&R Studies to confirm adequate gage discrimination. Test method assessments assure high reliability (repeatability and reproducibility) and consistency.
Process ranges also include establishing the appropriate and necessary upper and lower processing limits, as well as the expected normal operating conditions; equipment calibration tolerance needs to be considered for process parameter development (equipment manual is a reference to assess the equipment capability). Some of the process parameters that are evaluated may include, but are not limited to: temperature, pressure, vacuum, and dwell time. One of the recommended tools that can be used for this assessment is the Design of Experiments (DOE). As an example, using as a critical output of a sealing process the seal strength and adequate adhesive transfer should be at a minimum to select the optimal process window for validation. Essential parameters will be selected such that they will produce consistent seals meeting pre-determined criteria.
During process validation execution, challenges can include different production runs and adequate sampling to demonstrate process consistency of run variability and reproducibility across runs. Duration of the production runs should account for the different variables identified previously, such as: machine settings, different operators, breaks, shift changes, material lot differences, etc. Results of the process validation demonstrate capability of yielding sterile barrier systems and packaging systems to meet specifications.
After the packaging process is in place and successfully released, critical process parameters must be routinely monitored and documented to sustain consistent performance. Monitoring ensures variation remains stable and potential sources of variation are in control, thus maintaining adequate process performance. Examples of sustaining metrics include statistical control charts, such as: I-Chart, X-Bar, etc. These different control charts are required to be in place to monitor and verify adequacy of the process.
Always remember, packaging knowledge and skills are very specific. Therefore, experience in the appropriate packaging tools and training in the different packaging processes are important considerations for those individuals included as part of the packaging process validation efforts. Selecting the appropriate personnel to participate, assess, develop, plan and execute these actives will provide the packaging areas to have the appropriate process in place that will ensure sustainability over time.
Change is constant. As packaging professionals in this field, we need to regularly update our knowledge base in the latest regulations/standards and continuously challenge the processes to assure compliance.
Linnette Torres Puig is a Quality Director at Edwards Lifesciences. For more information on IoPP, visit iopp.org.
Editor's note: This article appears in Packaging World magazine as a monthly contributed column, "IoPP Professional Perspective."