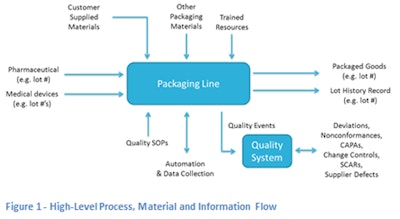
Pharmaceutical manufacturing is typically divided into primary formulation and secondary packaging. These phases are like two children that are polar opposites. Primary pharmaceutical manufacturing is a combination of batch continuous processes. The same drug formulation is made over and over and deviations in the process are undesirable and can cause a large batch of ingredients to be scrapped. Even one lost batch adds up to a sizeable loss and these losses are easily visible.
Secondary packaging is a batch discrete operation with many starts and stops. Strict compliance to Standard Operating Procedures (SOPs) for things like line clearance activities are essential to operations. Bills of materials are constantly changing. There are new boxes, inserts, bottles, caps, anti-counterfeit labeling, tamper-resistant packaging, etc. With regulated packaging there is the constant of continual change.
There is a night and day difference when you compare the number of deviations and nonconformances that occur in primary vs secondary pharmaceutical manufacturing. The many small losses in packaging add up financially and are akin to dying by a thousand little cuts. When you try to grab all of the losses in packaging in your hands, it is like sand pouring out through your fingers. It is the reason why many pharmaceutical companies outsource their packaging operations to expert contract packagers.
Packaging operations live in the busy intersection of operational efficiency and change management. With the pervasive use of contract packaging, it is important for contract packagers to have solid automation for quality management to match the automation of their packaging lines. Their established quality systems must satisfy the quality needs of every one of their customers, and balance the needs of regulatory compliance with operational efficiency. Manual collection and manipulation of quality event data using paper-driven systems causes supply chain delays and drives up packaging costs. Worse, manual quality systems prevent the contract manufacturer from adding value to the customer's supply chain. (Figure 1 illustrates the process, material, and information flow for a packaging operation. )
Packaging operations must manage the incoming pharmaceutical or medical device products as well as all of the packaging materials that protect the purity of the enclosed products. Additionally, there are other supplier products that are less critical but can provide challenging issues if they do not work (i.e., labels that don't stick to the package because the glue was not sufficient). Contract packagers have to manage customer-supplied materials and help troubleshoot when those supplied materials have quality issues. This can range from broken tablets to damaged inserts or cartons. The packaging operation is where everything comes together in a hurry.
From Figure 1, the packaging operation creates three products. One is physical while the other two are either paper or electronic. Second, the packaging operation must provide a lot history record (LHR). It must record everything about how the pharmaceuticals or medical devices were manufactured. The lot history record must be complete and consistent with the master lot history file. Errors and omissions on the LHR cause can cause deviations and nonconformances, which in some cases may require costly repackaging or worse, destruction of materials.
Third, the packaging operation must provide a thorough review of all quality incidents, deviations, nonconformances, open CAPAs, and change controls that impact this lot of product. This third area is covered by a quality management system. A paper quality system cannot operate in real-time. As the product volumes grow, so must the shadow quality team that keeps all of the systems, supplier materials, packaging, and LHR
processes in compliance.
Enterprise Quality Management Systems (EQMS) enable packaging operations to:
• Communicate to primary manufacturing regarding product quality issues (e.g., dimensional issues, broken products, etc.)
• Communicate to suppliers regarding poor quality materials (e.g., inserts with ripped or missing pages, incorrect quantities, bottle and cap dimensional issues, etc.)
• Quickly prove all packaging resources have been trained to package material XYZ
• Keep track of historical LHR issues and errors
• Keep track of historical and significant packaging line downtime, scrap, and rework issues
• Easily communicate with customer quality departments using standard reports regarding open deviations, CAPA, change controls, and nonconformances
• Assist customer supply chain departments to create supplier corrective action requests (SCARs) and communicate the context of the issues regarding the SCAR (e.g., recurring issue with low glue content on stickers for lot ABC)
EQMS provides a competitive advantage to packaging operations. Instead of trying to capture packaging losses and issues in your hands, an EQMS allows you to use a sifter instead of your hands.
Packaging lines are becoming more and more automated. Losses are becoming more related to the input materials and thus an EQMS helps the packaging operations team work more collaboratively with their customers and suppliers to make sure the input materials are right first time.
--Article written by Mike Cudemo, director of customer success at Sparta Systems
Secondary packaging is a batch discrete operation with many starts and stops. Strict compliance to Standard Operating Procedures (SOPs) for things like line clearance activities are essential to operations. Bills of materials are constantly changing. There are new boxes, inserts, bottles, caps, anti-counterfeit labeling, tamper-resistant packaging, etc. With regulated packaging there is the constant of continual change.
There is a night and day difference when you compare the number of deviations and nonconformances that occur in primary vs secondary pharmaceutical manufacturing. The many small losses in packaging add up financially and are akin to dying by a thousand little cuts. When you try to grab all of the losses in packaging in your hands, it is like sand pouring out through your fingers. It is the reason why many pharmaceutical companies outsource their packaging operations to expert contract packagers.
Packaging operations live in the busy intersection of operational efficiency and change management. With the pervasive use of contract packaging, it is important for contract packagers to have solid automation for quality management to match the automation of their packaging lines. Their established quality systems must satisfy the quality needs of every one of their customers, and balance the needs of regulatory compliance with operational efficiency. Manual collection and manipulation of quality event data using paper-driven systems causes supply chain delays and drives up packaging costs. Worse, manual quality systems prevent the contract manufacturer from adding value to the customer's supply chain. (Figure 1 illustrates the process, material, and information flow for a packaging operation. )
Packaging operations must manage the incoming pharmaceutical or medical device products as well as all of the packaging materials that protect the purity of the enclosed products. Additionally, there are other supplier products that are less critical but can provide challenging issues if they do not work (i.e., labels that don't stick to the package because the glue was not sufficient). Contract packagers have to manage customer-supplied materials and help troubleshoot when those supplied materials have quality issues. This can range from broken tablets to damaged inserts or cartons. The packaging operation is where everything comes together in a hurry.
From Figure 1, the packaging operation creates three products. One is physical while the other two are either paper or electronic. Second, the packaging operation must provide a lot history record (LHR). It must record everything about how the pharmaceuticals or medical devices were manufactured. The lot history record must be complete and consistent with the master lot history file. Errors and omissions on the LHR cause can cause deviations and nonconformances, which in some cases may require costly repackaging or worse, destruction of materials.
Third, the packaging operation must provide a thorough review of all quality incidents, deviations, nonconformances, open CAPAs, and change controls that impact this lot of product. This third area is covered by a quality management system. A paper quality system cannot operate in real-time. As the product volumes grow, so must the shadow quality team that keeps all of the systems, supplier materials, packaging, and LHR
processes in compliance.
Enterprise Quality Management Systems (EQMS) enable packaging operations to:
• Communicate to primary manufacturing regarding product quality issues (e.g., dimensional issues, broken products, etc.)
• Communicate to suppliers regarding poor quality materials (e.g., inserts with ripped or missing pages, incorrect quantities, bottle and cap dimensional issues, etc.)
• Quickly prove all packaging resources have been trained to package material XYZ
• Keep track of historical LHR issues and errors
• Keep track of historical and significant packaging line downtime, scrap, and rework issues
• Easily communicate with customer quality departments using standard reports regarding open deviations, CAPA, change controls, and nonconformances
• Assist customer supply chain departments to create supplier corrective action requests (SCARs) and communicate the context of the issues regarding the SCAR (e.g., recurring issue with low glue content on stickers for lot ABC)
EQMS provides a competitive advantage to packaging operations. Instead of trying to capture packaging losses and issues in your hands, an EQMS allows you to use a sifter instead of your hands.
Packaging lines are becoming more and more automated. Losses are becoming more related to the input materials and thus an EQMS helps the packaging operations team work more collaboratively with their customers and suppliers to make sure the input materials are right first time.
--Article written by Mike Cudemo, director of customer success at Sparta Systems