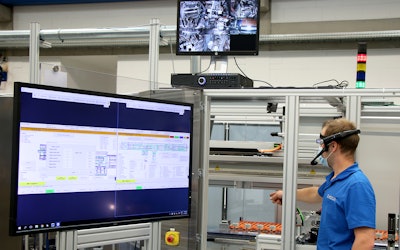
This content was written and submitted by the supplier. It has only been modified to comply with this publication’s space and style.
A new packaging line created by KOCH Pac-Systeme for an international consumer goods manufacturer in the USA is over 98 feet in length. This high-speed system can be rapidly retooled to produce different packaging formats. As travel restrictions prevented the customer’s teams from coming to Pfalzgrafenweiler for the Factory Acceptance Test (FAT), the entire machine acceptance test was carried out virtually–with some 15 participants from 5 different sites.
Digital competence
Two weeks were scheduled to check all the functions and formats of the flexible KOCH packaging line. Though the customer was thousands of miles away, they witnessed the FAT in action as if they were on site – thanks to hardware and modern digital solutions.
This involved installing numerous cameras with a night vision function on the line which the customers could access. Thanks to KOCH’s remote service system, they were able to get a real-time view of the operator interface and see how the individual processes on the line work. Detailed queries could best be clarified using service glasses. To this end, a KOCH service technician wore smart glasses which allowed the participants who had dialed in to see everything “through the eyes” of the expert who could also answer their specific questions.
Time differences are not a problem
Thanks to a special late-shift model set up for employees that participated in the FAT, KOCH could provide customers with FAT support during their regular daytime working hours.
Additional benefits
While virtual FATs were primarily a response to the restrictions caused by the coronavirus pandemic, they nonetheless demonstrate just how much added value digitalization can offer.
“Compared to on-site machine acceptance tests, the virtual alternative enables our customers to save on travel time and costs, while also giving them the flexibility to bring in additional participants, like machine operators who normally do not attend, or component suppliers who would otherwise not be involved,” says Wolfgang Braun, global account manager for consumer applications at KOCH. “However, virtual FATs cannot completely replace the analog tests in the long term, because personal contact with the customers–both during and beyond that required for the actual commissioning phase–is just too valuable. But we can certainly imagine continuing to offer the virtual FATs as an additional or supplementary service option after the coronavirus has passed.”