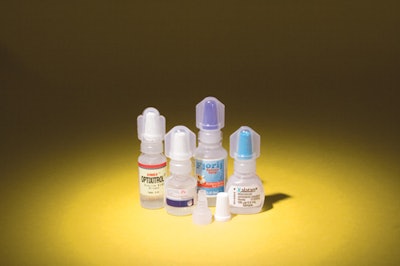
The aseptic blow/fill/seal (B/F/S) process can create a variety of container shapes and sizes used for packaging sterile pharmaceutical liquids. The process is also suited to producing closed aseptic containers, like injectables, that need to be opened under sterile conditions within a clinical environment such as a hospital, as well as sterile products opened by individuals in environments like ophthalmic dropper units.
These products must meet the mandates of drug manufacturers and government regulators that require sterile products that will stay sterile until time of use. Manufacturers also desire the most cost-efficient packaging systems to achieve these ends without any loss of product integrity. One of the more recent improvements in aseptic B/F/S processing that facilitates these goals is the advance in insertion technology.
The latest generation of aseptic B/F/S machines incorporates dedicated isolators adapted specifically for insertion applications. These modular insertion isolators are typically located outside of the classified machine room, separate from but directly connected to the B/F/S unit through a transfer tunnel.
The isolator and tunnel are typically sterilized with vaporized hydrogen peroxide and the Class 100 environment within it is maintained by HEPA filtration. This new addition to the aseptic B/F/S system has not only streamlined the insertion process, but has provided a higher level of sterility assurance for products with tip-and-caps and rubber/silicone stoppers inserted under aseptic conditions.
Insertion in advanced aseptic B/F/S
A critical aspect of B/F/S technology is its pyrogen-free molding of containers and ampoules. B/F/S processing resins, polyethylene and polypropylene, used to produce aseptic containers for injectables, ophthalmics, biologicals, and vaccines, are generally considered inert by the FDA, and many of the blow-molding resins used in B/F/S processing have received international acceptance as suitable for pharmaceutical liquids applications. These inert materials do not contain additives, have low water vapor permeability, and are easy and safe to handle in critical care environments such as hospitals.
Further, temperature-sensitive biological and protein-based products can be processed in advanced B/F/S machines, providing a level of enhanced sterility assurance.
The application of aseptically produced B/F/S containers with inserts has also gained in popularity. Advanced B/F/S machine designs allow the capability to incorporate the addition of premolded, presterilized components (inserts) into the basic container. These inserts, including items such as rubber and silicone stoppers, and tip-and-cap dropper units for eye drop containers (used to deliver a calibrated drop), are attached to the container after the blowing and filling process, prior to final sealing step. The application of inserts has allowed B/F/S technology to advance and expand into product markets such as intravenous drug administration, solution irrigation, and ophthalmic dropper units.
With ophthalmics, the B/F/S insert process enables increased efficiency and sterility control in the processing of expensive drug formations for treatment of glaucoma and other eye diseases. Other types of sterile inserts can be incorporated into the basic B/F/S-produced container as well, such as top geometrics for both bottles and ampoules that can include a multientry rubber stopper or a controlled diameter injection-molded insert, useful where multiple administration of a drug is required. The stopper would typically be an FDA-approved, rubber, or silicone insert that would be placed inside the bottle or parenteral. Then, at the point of delivery the nurse would stick a needle through the stopper and extract the fluid, or if it is a vascular flush, the nurse would insert it into the patient's IV set.
Aseptic B/F/S-produced small-volume parenterals (SVP), such as those used for local anesthetics, vitamins, vaccines, and other standard injectables, can be manufactured with a twist-off-opening feature. They can also be combined with a controlled-diameter form in the top to accommodate needle-less spikes. Luer locks or luer-slip fits can also be provided for making leak-free connections. For 2- to 5-mL small-volume parenterals, syringes can be connected directly to the ampoules without a needle, creating safer packaging.
B/F/S-produced, one piece, plungerless sterile syringes (designed for prefilling) for use in flushing hospital equipment such as catheters, are available for replacing traditional two-piece plunger-type syringes. The B/F/S syringe provides an offset chamber for trapping air, and preventing it from being dispensed during drug delivery.
Advanced B/F/S insertion processes can also incorporate tamper-evident features for multi-dose container closures.
Advanced insertion isolation
The latest generation of B/F/S machines use a modular design, integrating duo Class 100-environment manufacturing processes, and utilizing servo drive controls with system-integrated PLCs (programmable logic controllers). These B/F/S systems address process monitoring, streamlined maintenance, and consolidated machine components for optimum performance.
They feature advanced insertion technology, incorporating the use of a Class 100 environment isolation chamber located outside of the B/F/S unit, but integrated with the B/F/S machine. This process allows the operator to present a presterilized (typically with a gamma or an e-beam process) component (stopper or dropper insert) through a secure sterile pass-through into a Class 100 environment for insertion within the B/F/S filling shroud.
Sterile inserts are loaded into the isolator through a double-locking, sterile rapid transfer port. The inserts are indexed into a special track mechanism that transfers them from the isolator into the nozzle shroud ofthe B/F/S. The filling of the container and the placement of the insert into the container both take place in sequential operations within the nozzle shroud. Each component is inserted into a molded container before the final top closure is formed. The container-insert combination package is then sealed, having given the B/F/S product the intended drug delivery features. The entire operation takes place under Class 100 controlled environment conditions with no human intervention, providing sterility assurance for the final product.
Key factors of this isolation technology include minimizing particles generated through moving components, and controlling the air pressure cascade from the isolator to the nozzle shroud, providing enhanced sterility assurance and thereby achieving regulatory compliance. All of the mechanical features required to get the inserts from the isolator into the B/F/S container are enclosed within a Class 100 environment. A servo-controlled fill and insertion system eliminates the need for hydraulics above the mold.
Servo drives deliver the inserts, so belt and chain mechanisms, which typically require lubrication and can generate nonviable particles, are eliminated. High-speed PLCs provide integrated control architecture for the entire B/F/S machine. All modular functionality, such as with the insertion isolator, the insert-delivery track system and the B/F/S filling processes are integrated for speed and optimum performance. The PLCs receive continuous communication from the B/F/S-isolator system, monitoring the differential air pressure in the B/F/S and isolation systems, as well as ensuring that particle counts are under control.
Conventional liquid aseptic manufacturing, with parenterals for example, requires filling and sealing to be carried out in a Class 100 environment and necessitates considerable validation efforts. Both the B/F/S machine and the insertion isolator do not need to be housed in a Class 100 area because their activities are protected within the machines themselves. This protection considerably reduces the scope of validation requirements.
Sterility and particulate matter are two of the most critical requirements for aseptically produced products, and advanced B/F/S and insertion isolation technology offer advantages over earlier systems. They include maintaining precise control over differential air pressure between the isolator, the insert transport, and the B/F/S nozzle shroud. Both the isolator and the B/F/S system are equipped with HEPA air showers to assure a Class 100 environment under dynamic conditions in the isolator, tunnel and nozzle shroud area.
In the B/F/S process, nonviable particles primarily originate from the electrically heated cut-off knife contacting the molten parison, and that better control of nonviable particulates will provide enhanced sterility assurance for the B/F/S process. More advanced B/F/S systems use additional technology in response to FDA concern over particulate contamination during B/F/S fabrication.
Ultrasonic KleenKut® technology can be used to cut the molten parison at ambient temperature, drastically reducing nonviable smoke particles that are generated by traditional hot-knife cutting.
Expanding use of B/F/S insertion
Advanced aseptic B/F/S containers and ampoules can deliver precise dosing in disposable formats. The incorporation of a sterile tip-and-cap, a rubber stopper, or a multi-entry insert into the B/F/S package offers added flexibility in container design and drug delivery methods, as well as enhanced sterility safety. These benefits are continuing to push the acceptance and use of advanced aseptic B/F/S technology, particularly into injectable product areas and biologics, where proteins and other complex solutions have brought B/F/S technology to the forefront.
The B/F/S process also offers versatility for multiple container designs. A design feature of the ASEP-TECH® B/F/S systems, for example, permits the insertion process to be suspended without requiring significant equipment changeover. This allows the production of standard containers without inserts to be produced on the same machine with a simple recipe and tooling change.
As the use of advanced aseptic B/F/S processes broaden, insertion technology will become more important as drug producers continue to seek new delivery methods for breakthrough drugs.
--By Andrew W. Goll, technical sales manager for Weiler Engineering, Inc., a worldwide provider of aseptic blow-fill-seal custom packaging machinery for pharmaceutical and healthcare applications.