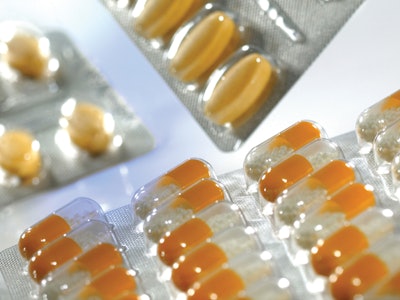
Pharmaceutical packaging film should comply with at least the following set of regulations and also satisfy the criteria outlined in the various guidelines. For example, knowledge of technical attributes of a film, such as moisture vapor transmission rate, carries relevance when satisfying sets of guidelines such as those established by U.S. Pharmacopoeia or CDER, especially with regard to controlling changes. This list presents a starting point for federal, state, and local regulations:
• U.S. Federal Food, Drug, and Cosmetic Act (FDA Title 21 CFR)
--Food additive sections (e.g. § 174, 175, etc.)
--Part 201 Food Allergen Act (21 U.S.C §321)
--Part 211 current Good Manufacturing Practices
• U.S. Generic Drug Enforcement Act of 1992 Section 306 (Debarment Compliance)
--European Regulations and Directives
--1935/2004/EC of October 27, 2004
--2002/72/EC of August 6, 2002
--2002/1/EC of January 6, 2004
--2004/19/EC of March 1, 2004
--2005/79/EC of November 18, 2005
--2007/19/EC of March 31, 2007
--2008/39/EC of March 6, 2008
--The German Consumer Articles Ordinance of December 23, 1997
Resources offering tips and insights for selecting a pharmaceutical blister packaging film include the following:
• U.S. Pharmacopoeia
-- Containers
-- Containers - Permeation (Applies to complete package)
-- Organic Volatile Impurities
--Class VI Biological Reactivity Assay
--European Pharmacopoeia 3.1.11. Materials Based on Non-Plasticized Polyvinyl Chloride for
--Containers for Dry Dosage Forms for Oral Administration
--European Pharmacopoeia 3.1.15. Polyethylene Terephthalate for Containers for Preparations
--not for Parenteral Use
--European Pharmacopoeia 3.2.2. Plastic Containers and Closures for Pharmaceutical Use
--European REACH (Registration, Evaluation, and Authorization of Chemicals) 1907/2006,
--REACH Annex XIII, XIV, & XV Substances of Very High Concern (SVHC), and EC No. 465/2008
--The California Safe Drinking Water and Toxic Enforcement Act of 1986 (Proposition 65)
--“Guidance for Industry, Changes to an Approved NDA or ANDA,” published by U.S. Department of Health and Human Services, Food and Drug Administration, Center for Drug Evaluation and Research (CDER) April 2004, CMC, Revision 1
Technical considerations
The pharmaceutical dosage product and its container closure system act together to serve as an integral unit. The primary packaging of this closure protects the product from outside influences that would otherwise render it useless while allowing the manufacturer of the product to package it using practices that typically involve automated form/fill/seal equipment.
Since films typically run within a thermoforming process in unsupported type web equipment, dimensional stability of the webs allows the process to function properly. A web material that shows a consistent degree of change in dimensions in the cross and machine direction throughout the thermoforming range typically works well. For this reason, the pharmaceutical industry has relied heavily on PVC films since this particular attribute helps a machine maintain good registration throughout the forming, filling, sealing, perforating, and punching operations commonly used in blister packaging. Selecting a film with a degree of cross-directional growth when subjected to thermoforming temperatures represents another attribute that aids in robust processing. Other types of polymers, such as homopolymer and copolymer polyester-based films can also work well in this function.
Thermoforming window
Selecting a film capable of handling a thermoforming temperature range of approximately 30°C typically allows for flexibility in the allowable run conditions of the packaging equipment. In many cases for forming without plug-assist, a film processed at the low end of the thermoforming range will result in partially formed cavities. At the high end of the range, holes will often form in the regions of the geometry known to thin the material most.
Commonly used thermoforming films typically have glass transition temperatures between 70 and 80° C. The materials tend to form well when they reach about 115 to 125°C. After thermoforming, cooling the web to between 30 and 40°C will usually lock it into the final shape but still allow for some stress relief of the material.
Optimizing the cooling of the web beyond thermoforming not only complements the dimensional stability of the film, but also benefits the seal by not overly stressing the adhesive interface between the film and the lid. Consider that any suitable material will demonstrate good stretch behavior and strength while in its semi-solid form to achieve robust thermoforming performance.
Thickness variation
A film with minimal variation in thickness has benefits primarily with regard to the sealing portion of the process. The film industry refers to a roll with minimal variation in the cross direction of the web as one with “good profile.” A film with gauge control of less than 5% in the commonly used gauge ranges of 191-381μm when run with “dedicated” upper and lower thermoforming tools typically helps preserve the flange of the blister card and can deliver post-forming gauge variation of less than
20μm.
Although other factors can influence the result, proper control here helps reduce leaking cavities and channels during vacuum leak tests made on finished packages. Reduced variation in thickness also can help minimize gauge bands in rolls that lead to variation in physical appearance and even how layers may block to one another especially for coated and laminated products that may not have the slip and release of the base layer. Any alternative film should offer gauge control in the area of approximately 5% as to not invite problems solved by the standard choices available in the market.
Sealing
Since in most situations lidstock materials have a heat-seal coating applied to them and the films used in pharmaceutical packaging do not, effective seal performance of a film typically relates to the topics of minimizing residual stress and thickness variation in the flange of the package. Note, however, that as the chemistry of the film changes with selection of the type, this may sometime require changes to the type of heat-seal coating used with it.
In some cases, a suitable combination of heat-seal coating and film contact layer may not exist, therefore necessitating the use of possibly another film or orienting the layers properly in order to make a seal. With regard to processing the materials, when using commonly available materials in the market, most tend to work well together when applying heat through the lidstock to make the heat-seal coating flow while keeping the film cool to preserve its dimension. Most compatible heat-seal coatings tend to flow and make good contact with the film when heated to 150°C with post-seal cooling.
As mentioned before, try to avoid the use of universal or “bell”-shaped forming tools when forming blisters to eliminate many common problems associated with sealing related to web dimensional stability, wrinkling, and stress.
Perforation and punching
Pharmaceutical blister packaging equipment makes cuts in the film in the form of both perforations for tearing and punching to arrive at the final shape of the card. A well-suited material must cut cleanly without angel hair and, in many cases, must actually have a degree of brittleness. The brittleness helps the film to break in a functional way so that the user can remove doses and gain access to the product.
A film with too much brittleness combined with blades, edges, or anvils well beyond their original functioning state can often create undesirable “herringbone” patterns in the film that leads to stress propagation and part failures. Films chosen with too much ductility often just hinge in cases like this, making it impossible for a package to perform its function.
Moisture vapor transmission rates (MVTR)
Many drugs can degrade and lose their efficacy through hydrolysis, or otherwise stated by reacting with water. In a large number of situations, the moisture diffuses from the outside environment through the film and into the product. A package engineer can select a different type of film to create different levels of barrier to guard against water diffusion. Monolayer films, such as those manufactured from PVC, polyester, and polypropylene, offer a basic level of moisture vapor protection. In moisture-sensitive applications, successfully protecting the drug requires some type of multiple-layer structure barrier film. The pharmaceutical industry typically relies on multiple-layer structures made with PVdC coatings or laminations made with Aclar® films.
Coated and laminated films will typically utilize a base film layer of PVC or polyester. The PVC and polyester films allow for successful processing on common Form/fill/seal equipment while the PVdC and Aclar® portions provide the barrier to diffusion. The pharmaceutical industry commonly packages product with several types of barrier films offering varying levels of barrier for use in stability studies in order to determine the effectiveness of the package to prevent hydrolysis from occurring.
Oxygen transmission rates (OTR)
The need for oxygen barrier in packaging has gained more attention recently due to degradation through oxidation. Similar combinations of multiple-layer films exist to fulfill this need as well as those mentioned above for moisture protection. In this case, a PVdC-coated film offers good mid-range oxygen protection. Although more prominent in food packaging, laminated films with an EVOH layer have gained some acceptance in the pharmaceutical markets. These films tend to work well when designed in a manner to protect EVOH from losing its oxygen barrier when its moisture level rises.
Multiple-layer structures that use Aclar® to protect the EVOH from moisture allow EVOH to protect the drug from oxygen. These types of barrier films create a more sophisticated challenge since creating the desired outcome relies on selecting a base film that obeys the principles discussed while utilizing effective layer arrangements to deliver the functionality to prevent degradation of the drug.
Light transmission
Films can deliver varying degrees of light protection based mostly on the UV absorbers and pigments used in either the base film of a multilayer structure or that of the monolayer film. Many brand owners and engineers will default to the information contained in USP to determine a requirement. A film with both a “food-approved” UV absorber combined with an amber pigment will typically meet USP and prevent the percentage of light transmission from exceeding 10% for wavelengths between 290 and 450nm.
Within the many options that pharmaceutical blister packaging presents, the common theme remains the same in that a film must protect the product while possessing the characteristic capable of making automated processing possible. Gaining success in this environment starts by relating regulatory concerns, material attributes, and product needs in an economical way.
--By Daniel Stagnaro, Business Manager, Pharmaceutical Films, Klöckner Pentaplast
• U.S. Federal Food, Drug, and Cosmetic Act (FDA Title 21 CFR)
--Food additive sections (e.g. § 174, 175, etc.)
--Part 201 Food Allergen Act (21 U.S.C §321)
--Part 211 current Good Manufacturing Practices
• U.S. Generic Drug Enforcement Act of 1992 Section 306 (Debarment Compliance)
--European Regulations and Directives
--1935/2004/EC of October 27, 2004
--2002/72/EC of August 6, 2002
--2002/1/EC of January 6, 2004
--2004/19/EC of March 1, 2004
--2005/79/EC of November 18, 2005
--2007/19/EC of March 31, 2007
--2008/39/EC of March 6, 2008
--The German Consumer Articles Ordinance of December 23, 1997
Resources offering tips and insights for selecting a pharmaceutical blister packaging film include the following:
• U.S. Pharmacopoeia
-- Containers
-- Containers - Permeation (Applies to complete package)
-- Organic Volatile Impurities
--Class VI Biological Reactivity Assay
--European Pharmacopoeia 3.1.11. Materials Based on Non-Plasticized Polyvinyl Chloride for
--Containers for Dry Dosage Forms for Oral Administration
--European Pharmacopoeia 3.1.15. Polyethylene Terephthalate for Containers for Preparations
--not for Parenteral Use
--European Pharmacopoeia 3.2.2. Plastic Containers and Closures for Pharmaceutical Use
--European REACH (Registration, Evaluation, and Authorization of Chemicals) 1907/2006,
--REACH Annex XIII, XIV, & XV Substances of Very High Concern (SVHC), and EC No. 465/2008
--The California Safe Drinking Water and Toxic Enforcement Act of 1986 (Proposition 65)
--“Guidance for Industry, Changes to an Approved NDA or ANDA,” published by U.S. Department of Health and Human Services, Food and Drug Administration, Center for Drug Evaluation and Research (CDER) April 2004, CMC, Revision 1
Technical considerations
The pharmaceutical dosage product and its container closure system act together to serve as an integral unit. The primary packaging of this closure protects the product from outside influences that would otherwise render it useless while allowing the manufacturer of the product to package it using practices that typically involve automated form/fill/seal equipment.
Since films typically run within a thermoforming process in unsupported type web equipment, dimensional stability of the webs allows the process to function properly. A web material that shows a consistent degree of change in dimensions in the cross and machine direction throughout the thermoforming range typically works well. For this reason, the pharmaceutical industry has relied heavily on PVC films since this particular attribute helps a machine maintain good registration throughout the forming, filling, sealing, perforating, and punching operations commonly used in blister packaging. Selecting a film with a degree of cross-directional growth when subjected to thermoforming temperatures represents another attribute that aids in robust processing. Other types of polymers, such as homopolymer and copolymer polyester-based films can also work well in this function.
Thermoforming window
Selecting a film capable of handling a thermoforming temperature range of approximately 30°C typically allows for flexibility in the allowable run conditions of the packaging equipment. In many cases for forming without plug-assist, a film processed at the low end of the thermoforming range will result in partially formed cavities. At the high end of the range, holes will often form in the regions of the geometry known to thin the material most.
Commonly used thermoforming films typically have glass transition temperatures between 70 and 80° C. The materials tend to form well when they reach about 115 to 125°C. After thermoforming, cooling the web to between 30 and 40°C will usually lock it into the final shape but still allow for some stress relief of the material.
Optimizing the cooling of the web beyond thermoforming not only complements the dimensional stability of the film, but also benefits the seal by not overly stressing the adhesive interface between the film and the lid. Consider that any suitable material will demonstrate good stretch behavior and strength while in its semi-solid form to achieve robust thermoforming performance.
Thickness variation
A film with minimal variation in thickness has benefits primarily with regard to the sealing portion of the process. The film industry refers to a roll with minimal variation in the cross direction of the web as one with “good profile.” A film with gauge control of less than 5% in the commonly used gauge ranges of 191-381μm when run with “dedicated” upper and lower thermoforming tools typically helps preserve the flange of the blister card and can deliver post-forming gauge variation of less than
20μm.
Although other factors can influence the result, proper control here helps reduce leaking cavities and channels during vacuum leak tests made on finished packages. Reduced variation in thickness also can help minimize gauge bands in rolls that lead to variation in physical appearance and even how layers may block to one another especially for coated and laminated products that may not have the slip and release of the base layer. Any alternative film should offer gauge control in the area of approximately 5% as to not invite problems solved by the standard choices available in the market.
Sealing
Since in most situations lidstock materials have a heat-seal coating applied to them and the films used in pharmaceutical packaging do not, effective seal performance of a film typically relates to the topics of minimizing residual stress and thickness variation in the flange of the package. Note, however, that as the chemistry of the film changes with selection of the type, this may sometime require changes to the type of heat-seal coating used with it.
In some cases, a suitable combination of heat-seal coating and film contact layer may not exist, therefore necessitating the use of possibly another film or orienting the layers properly in order to make a seal. With regard to processing the materials, when using commonly available materials in the market, most tend to work well together when applying heat through the lidstock to make the heat-seal coating flow while keeping the film cool to preserve its dimension. Most compatible heat-seal coatings tend to flow and make good contact with the film when heated to 150°C with post-seal cooling.
As mentioned before, try to avoid the use of universal or “bell”-shaped forming tools when forming blisters to eliminate many common problems associated with sealing related to web dimensional stability, wrinkling, and stress.
Perforation and punching
Pharmaceutical blister packaging equipment makes cuts in the film in the form of both perforations for tearing and punching to arrive at the final shape of the card. A well-suited material must cut cleanly without angel hair and, in many cases, must actually have a degree of brittleness. The brittleness helps the film to break in a functional way so that the user can remove doses and gain access to the product.
A film with too much brittleness combined with blades, edges, or anvils well beyond their original functioning state can often create undesirable “herringbone” patterns in the film that leads to stress propagation and part failures. Films chosen with too much ductility often just hinge in cases like this, making it impossible for a package to perform its function.
Moisture vapor transmission rates (MVTR)
Many drugs can degrade and lose their efficacy through hydrolysis, or otherwise stated by reacting with water. In a large number of situations, the moisture diffuses from the outside environment through the film and into the product. A package engineer can select a different type of film to create different levels of barrier to guard against water diffusion. Monolayer films, such as those manufactured from PVC, polyester, and polypropylene, offer a basic level of moisture vapor protection. In moisture-sensitive applications, successfully protecting the drug requires some type of multiple-layer structure barrier film. The pharmaceutical industry typically relies on multiple-layer structures made with PVdC coatings or laminations made with Aclar® films.
Coated and laminated films will typically utilize a base film layer of PVC or polyester. The PVC and polyester films allow for successful processing on common Form/fill/seal equipment while the PVdC and Aclar® portions provide the barrier to diffusion. The pharmaceutical industry commonly packages product with several types of barrier films offering varying levels of barrier for use in stability studies in order to determine the effectiveness of the package to prevent hydrolysis from occurring.
Oxygen transmission rates (OTR)
The need for oxygen barrier in packaging has gained more attention recently due to degradation through oxidation. Similar combinations of multiple-layer films exist to fulfill this need as well as those mentioned above for moisture protection. In this case, a PVdC-coated film offers good mid-range oxygen protection. Although more prominent in food packaging, laminated films with an EVOH layer have gained some acceptance in the pharmaceutical markets. These films tend to work well when designed in a manner to protect EVOH from losing its oxygen barrier when its moisture level rises.
Multiple-layer structures that use Aclar® to protect the EVOH from moisture allow EVOH to protect the drug from oxygen. These types of barrier films create a more sophisticated challenge since creating the desired outcome relies on selecting a base film that obeys the principles discussed while utilizing effective layer arrangements to deliver the functionality to prevent degradation of the drug.
Light transmission
Films can deliver varying degrees of light protection based mostly on the UV absorbers and pigments used in either the base film of a multilayer structure or that of the monolayer film. Many brand owners and engineers will default to the information contained in USP to determine a requirement. A film with both a “food-approved” UV absorber combined with an amber pigment will typically meet USP and prevent the percentage of light transmission from exceeding 10% for wavelengths between 290 and 450nm.
Within the many options that pharmaceutical blister packaging presents, the common theme remains the same in that a film must protect the product while possessing the characteristic capable of making automated processing possible. Gaining success in this environment starts by relating regulatory concerns, material attributes, and product needs in an economical way.
--By Daniel Stagnaro, Business Manager, Pharmaceutical Films, Klöckner Pentaplast