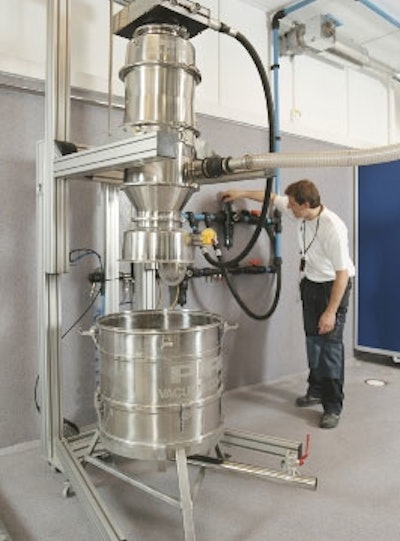
Compressed tablets are still the most popular dosage form for pharmaceuticals. More than 75% of pharmaceutical products are sold in solid dosage form. Strong growth is predicted for compressed tablets due to the explosion of the nutraceuticals market, especially in the United States.
The potential for growth in tablet manufacturing is high. However, several challenges and trends are threatening the profit potential. Today, pharmaceutical manufacturers are challenged to evolve their production processes in order to survive and excel in an increasingly competitive industry. While product quality has always been of paramount importance, strenuous economic times and continually inflating drug prices are heightening consumer demand for lower-priced prescriptions. Tablet manufacturers are more than ever seeking new ways to automate their lines to speed and streamline production.
By automating the conveying process, vacuum technologies can improve productivity and enhance quality. In addition, selecting a vacuum technology that is maintenance-free and energy efficient can allow tablet manufacturers to cut costs and meet challenging consumer demands for quality pharmaceuticals and lower prices.
Offering a safer environment
In general, reducing manual labor through automated vacuum conveying can improve working conditions by reducing heavy lifting. In addition, American manufacturers must abide by Safety, Health and Environment (SHE) regulations enforced by the U.S. Dept. of Occupational Safety & Health Administration. In Europe, the European Foundation for the Improvement of Living and Working conditions (Eurofounda) oversees the improvement of industrial working conditions.
Heat, dust, and noise are all pollutants in the working environment that detract from worker safety and the stringent sanitation demands for pharmaceutical and chemical production. Tablet manufacturers can greatly reduce manual labor and diminish exposure to environmental irritants with the installation of vacuum conveying equipment that moves dry powder products through dedicated pipe systems. These systems fully contain the powders to minimize dust and also generate less heat. To ensure the highest standard of worker safety, the conveyors should also have few moving parts, and be easily assembled and disassembled to reduce worker strain.
Increasing uptime
Given the 24/7 production runs in pharmaceutical manufacturing, automation technologies must be reliable. There is no time for line stoppages or ongoing maintenance. Additionally, changeovers can add costs and downtime. A vacuum conveyor must facilitate changeover or risk negating the gains realized through automation.
Simple solutions can effectively combat the erosion of productivity caused by line stoppages, maintenance, or changeover. Vacuum technologies with few moving parts are not only safer; they are maintenance-free and can reduce downtime. Conveyors that are easily handled by workers are more quickly assembled and disassembled, reducing the time it takes for equipment adjustments between batches and during cleanings. Machines containing fewer components also help minimize part mix-ups and help to prevent line stoppages.
Other vacuum conveyor benefits include the following:
• Cost-effective, easy cleaning. In addition to aiming to reduce changeover time, tablet manufacturers must also prevent cross-contamination of the product. A vacuum conveyor that is easily disassembled for quick cleanup is a cost-efficient way of averting cross-contamination.
• Reduced energy consumption. As energy costs soar, the reduction of energy usage is a strategic step to trim expenses from pharmaceutical manufacturing operations. In addition, reducing energy consumption is good for sustainability efforts. Conveying systems powered by decentralized vacuum technologies are more energy-efficient than their centralized counterparts. While a centralized vacuum system puts more distance between the source of the power and the point of use, a decentralized vacuum system uses multistage ejector technology to apply the vacuum where needed. This way, no additional energy is expended to compensate for the extra distance.
• Optimized automation. Automating the tablet-handling process affords many advantages and conveniences to pharmaceutical manufacturers, including increased productivity and reduced staff injury. However, poorly designed automated conveying systems can cause segregation and tablet breakage. Simple precautions can be taken to avoid incurring the costs of product waste as a result of either event.
• Prevent segregation. Particle separation prior to tablet compression, known as segregation, can threaten the integrity of drug dosages and jeopardize the uniformity of a batch. Segregation can occur during tablet production as a result of gravity and particle characteristics, and due to external factors such as airflow and vibration. When implementing vacuum conveying, segregation risk can be reduced by handling the material at a controlled speed to ensure that the materials stay blended.
• Prevent tablet breakage. Tablets can also break due to exposure to friction and shock during or after the manufacturing process. A broken tablet is susceptible to contamination, rendering it useless. As a result, product waste can accumulate and cause production delays. To prevent breakage, tablet manufacturers can employ an accommodating vacuum conveying system. To start, the conveying system should have an adaptable feed rate to enable the system to be sped up or slowed depending on the size or volume of the tablets being handled. Also, the vacuum conveyor's tubing and piping specifications along with couplings can be designed to reduce speed and avoid product damage. The tubing and piping should have soft curves to avoid tablet breakage.
In conclusion, vacuum automation technologies can play a key roll in streamlining tablet production. By taking the right precautions in installing a reliable, efficient vacuum conveying system, manufacturers can increase their productivity, reduce energy usage, and improve their work environments. As companies harness vacuum technology to advance tablet production, more efficient conveying systems will translate into cost savings, helping tablet manufacturers stay competitive by enabling them to produce more affordable prescriptions.
-By Häla El Sheemy
References:
1. http://www.pharmafocusasia.com/knowledge_bank/articles/dem_solutions.htm
2. http://www.reuters.com/article/pressRelease/idUS162213+11-Mar-2008+MW20080311
Häla El Sheemy is the business unit manager Pharma & Chem, for PIAB, a developer and manufacturer of vacuum pumps, vacuum accessories, vacuum conveyors, and suction cups for automated material handling and factory automation processes.
SIDEBAR STORY:
Contract manufacturer Surepharm Services reaps benefits
In one example of the benefits of vacuum conveying technology, Surepharm Services Ltd., a Staffordshire, U.K.-based contract manufacturer specializing in tablet production, improved its working environment by reducing the amount of heavy lifting and manual labor performed by its employees. The company replaced its manual loading operation with three PIAB C-Series vacuum conveyors to transfer powder products to blending and tableting machinery. As a result, the company saved up to 30 hours of labor per week, reduced dust, with the lightweight conveying equipment quickening the cleaning process by reducing the physical demand on the workers.
In the past 15 years, Surepharm has enjoyed study growth. Steve Wood, the company's production services manager, says, “Automated systems will improve the working environment in our facility by reducing manual loading and dust in the atmosphere.” Beyond those two benefits, Surepharm recognized the need for a more ergonomic setup in its tableting process.
The application Surepharm assessed involved various veterinary formulations that are
prepared, blended, and loaded into drums before being formed into tablets. “With manual loading in place, there were concerns about potential injuries among operators. We wanted to be sure that we were both following regulations as well as maintaining the optimum fill levels for each tablet produced,” he says.
Surepharm chose to install three C-Series conveyors to transfer powder products to blending and tableting machinery. Powered by pneumatically driven vacuum pumps, these enclosed stainless-steel systems can safely and quietly transport up to one ton of powder per hour. “The compact nature of the conveyors and the ease of loading and cleaning have proved invaluable,” Wood notes.
“Our long-term customer relationships are forged on technical expertise, quality, reliability, and efficiency. It is natural for us to look for these attributes in a partner as well,” says Wood. “The PIAB solution simplified and improved the operator environment, and increased productivity by saving us 25 to 30 hours of labor per week. We now have a more reliable solution and far superior equipment and support than offered ever before.”
The potential for growth in tablet manufacturing is high. However, several challenges and trends are threatening the profit potential. Today, pharmaceutical manufacturers are challenged to evolve their production processes in order to survive and excel in an increasingly competitive industry. While product quality has always been of paramount importance, strenuous economic times and continually inflating drug prices are heightening consumer demand for lower-priced prescriptions. Tablet manufacturers are more than ever seeking new ways to automate their lines to speed and streamline production.
By automating the conveying process, vacuum technologies can improve productivity and enhance quality. In addition, selecting a vacuum technology that is maintenance-free and energy efficient can allow tablet manufacturers to cut costs and meet challenging consumer demands for quality pharmaceuticals and lower prices.
Offering a safer environment
In general, reducing manual labor through automated vacuum conveying can improve working conditions by reducing heavy lifting. In addition, American manufacturers must abide by Safety, Health and Environment (SHE) regulations enforced by the U.S. Dept. of Occupational Safety & Health Administration. In Europe, the European Foundation for the Improvement of Living and Working conditions (Eurofounda) oversees the improvement of industrial working conditions.
Heat, dust, and noise are all pollutants in the working environment that detract from worker safety and the stringent sanitation demands for pharmaceutical and chemical production. Tablet manufacturers can greatly reduce manual labor and diminish exposure to environmental irritants with the installation of vacuum conveying equipment that moves dry powder products through dedicated pipe systems. These systems fully contain the powders to minimize dust and also generate less heat. To ensure the highest standard of worker safety, the conveyors should also have few moving parts, and be easily assembled and disassembled to reduce worker strain.
Increasing uptime
Given the 24/7 production runs in pharmaceutical manufacturing, automation technologies must be reliable. There is no time for line stoppages or ongoing maintenance. Additionally, changeovers can add costs and downtime. A vacuum conveyor must facilitate changeover or risk negating the gains realized through automation.
Simple solutions can effectively combat the erosion of productivity caused by line stoppages, maintenance, or changeover. Vacuum technologies with few moving parts are not only safer; they are maintenance-free and can reduce downtime. Conveyors that are easily handled by workers are more quickly assembled and disassembled, reducing the time it takes for equipment adjustments between batches and during cleanings. Machines containing fewer components also help minimize part mix-ups and help to prevent line stoppages.
Other vacuum conveyor benefits include the following:
• Cost-effective, easy cleaning. In addition to aiming to reduce changeover time, tablet manufacturers must also prevent cross-contamination of the product. A vacuum conveyor that is easily disassembled for quick cleanup is a cost-efficient way of averting cross-contamination.
• Reduced energy consumption. As energy costs soar, the reduction of energy usage is a strategic step to trim expenses from pharmaceutical manufacturing operations. In addition, reducing energy consumption is good for sustainability efforts. Conveying systems powered by decentralized vacuum technologies are more energy-efficient than their centralized counterparts. While a centralized vacuum system puts more distance between the source of the power and the point of use, a decentralized vacuum system uses multistage ejector technology to apply the vacuum where needed. This way, no additional energy is expended to compensate for the extra distance.
• Optimized automation. Automating the tablet-handling process affords many advantages and conveniences to pharmaceutical manufacturers, including increased productivity and reduced staff injury. However, poorly designed automated conveying systems can cause segregation and tablet breakage. Simple precautions can be taken to avoid incurring the costs of product waste as a result of either event.
• Prevent segregation. Particle separation prior to tablet compression, known as segregation, can threaten the integrity of drug dosages and jeopardize the uniformity of a batch. Segregation can occur during tablet production as a result of gravity and particle characteristics, and due to external factors such as airflow and vibration. When implementing vacuum conveying, segregation risk can be reduced by handling the material at a controlled speed to ensure that the materials stay blended.
• Prevent tablet breakage. Tablets can also break due to exposure to friction and shock during or after the manufacturing process. A broken tablet is susceptible to contamination, rendering it useless. As a result, product waste can accumulate and cause production delays. To prevent breakage, tablet manufacturers can employ an accommodating vacuum conveying system. To start, the conveying system should have an adaptable feed rate to enable the system to be sped up or slowed depending on the size or volume of the tablets being handled. Also, the vacuum conveyor's tubing and piping specifications along with couplings can be designed to reduce speed and avoid product damage. The tubing and piping should have soft curves to avoid tablet breakage.
In conclusion, vacuum automation technologies can play a key roll in streamlining tablet production. By taking the right precautions in installing a reliable, efficient vacuum conveying system, manufacturers can increase their productivity, reduce energy usage, and improve their work environments. As companies harness vacuum technology to advance tablet production, more efficient conveying systems will translate into cost savings, helping tablet manufacturers stay competitive by enabling them to produce more affordable prescriptions.
-By Häla El Sheemy
References:
1. http://www.pharmafocusasia.com/knowledge_bank/articles/dem_solutions.htm
2. http://www.reuters.com/article/pressRelease/idUS162213+11-Mar-2008+MW20080311
Häla El Sheemy is the business unit manager Pharma & Chem, for PIAB, a developer and manufacturer of vacuum pumps, vacuum accessories, vacuum conveyors, and suction cups for automated material handling and factory automation processes.
SIDEBAR STORY:
Contract manufacturer Surepharm Services reaps benefits
In one example of the benefits of vacuum conveying technology, Surepharm Services Ltd., a Staffordshire, U.K.-based contract manufacturer specializing in tablet production, improved its working environment by reducing the amount of heavy lifting and manual labor performed by its employees. The company replaced its manual loading operation with three PIAB C-Series vacuum conveyors to transfer powder products to blending and tableting machinery. As a result, the company saved up to 30 hours of labor per week, reduced dust, with the lightweight conveying equipment quickening the cleaning process by reducing the physical demand on the workers.
In the past 15 years, Surepharm has enjoyed study growth. Steve Wood, the company's production services manager, says, “Automated systems will improve the working environment in our facility by reducing manual loading and dust in the atmosphere.” Beyond those two benefits, Surepharm recognized the need for a more ergonomic setup in its tableting process.
The application Surepharm assessed involved various veterinary formulations that are
prepared, blended, and loaded into drums before being formed into tablets. “With manual loading in place, there were concerns about potential injuries among operators. We wanted to be sure that we were both following regulations as well as maintaining the optimum fill levels for each tablet produced,” he says.
Surepharm chose to install three C-Series conveyors to transfer powder products to blending and tableting machinery. Powered by pneumatically driven vacuum pumps, these enclosed stainless-steel systems can safely and quietly transport up to one ton of powder per hour. “The compact nature of the conveyors and the ease of loading and cleaning have proved invaluable,” Wood notes.
“Our long-term customer relationships are forged on technical expertise, quality, reliability, and efficiency. It is natural for us to look for these attributes in a partner as well,” says Wood. “The PIAB solution simplified and improved the operator environment, and increased productivity by saving us 25 to 30 hours of labor per week. We now have a more reliable solution and far superior equipment and support than offered ever before.”