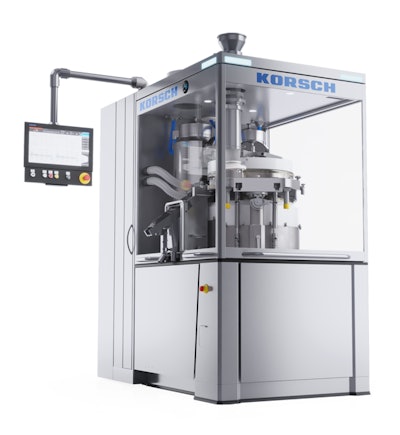
This content was written and submitted by the supplier. It has only been modified to comply with this publication’s space and style.
KORSCH America—the U.S. subsidiary of KORSCH AG, a provider of tablet press technology offering solutions for product development, scale-up, high-speed production, multi-layer, mini-tablet, and WIP/high-containment applications—is set to debut its X 5 Tablet Press, which increases single-sided output while maintaining KORSCH’s hallmark flexibility and fast change design.
This single-sided rotary press features a turret segment capability that increases the number of punch stations, and offers an output capability more than 50% higher than the company’s flagship XL 400, despite a slightly larger footprint.
The X 5 comes in two versions: the X 5 SFP provides dedicated single-layer capability, while the X 5 MFP offers flexible single-layer, bi-layer, and tri-layer flexibility. Both models share a common turret and interchangeable product contact parts for maximum efficiency and flexibility in high-speed, high-volume production environments. The segmented turret technology and increased output is leveraged for every tablet format.
The X 5 features an integrated electrical cabinet, torque drive, fully sealed design, and unsurpassed accessibility for cleaning, changeovers and maintenance. Installation options include a conventional in-room layout or through-the-wall mounting. The X 5 offers a range of product containment configurations, including a dry containment execution (DryCon) for OEB 3 and OEB 4 applications, and a wash-in-place execution (WipCon) for OEB 4 and OEB 5 applications. For all containment projects, KORSCH provides a fully integrated and turnkey system, including support documentation and SMEPAC testing.
Operational Efficiency
Of note, the X 5’s exchangeable turret technology affords extremely fast transition between products, and the ability to produce tablets of any size and shape. The segmented turret design simplifies and streamlines product changeovers by replacing conventional dies with three (3) segments that easily can be installed. For precision tablet weight control at the highest press speeds, the X 5 features a long filling length and configurable power feeder that permits both 2-chamber and 3-paddle chamber executions. With variable speed control and a wide range of feeder paddle options, the X 5 is geared for high-output manufacturing. For changeovers, superior compression zone access, smooth surfaces and minimal fast change parts yield an expedited process for maximized machine uptime.
Large windows provide excellent visibility and ample access to the compression zone for streamlined changeover and turret exchange. A multi-function column with two separate compartments houses the electrical components and the main dust extraction connection, while the water-cooled chiller serves both the torque drive and heat exchanger. The result is a fully sealed machine with no heat transfer to either the press’ compression zone or the compression room. This closed design also eliminates potential contamination in the machine base or electrical cabinet.
The X 5 also minimizes both noise and vibration. A carrier plate supporting the proven KORSCH compression columns is mounted on pneumatic dampers—a patented design that fully isolates vibration from the head piece and machine base. The result is significantly reduced operating noise (<80dB) and elimination of vibration transmission. The pre- and main compression columns are fixed on the carrier plate, and feature an innovative retractable design to facilitate expedited cleaning and turret exchange.
Industry 4.0 Features
Pharma 4.0 ready with smart metrics-monitoring features, the X 5 provides a deeper understanding of the compression process. The unit’s onboard diagnostics and data-to-dashboard capabilities serve as the basis for manufacturing optimization through anticipated servicing and activity analysis, helping maximize both quality and overall output.
The KORSCH control system’s open architecture yields easy integration with central networks, and offers domain authentication, central recipe management and central batch report archiving. A standard OPC UA Server permits press parameters to be passed to a SCADA or Historian system in real time, and advanced capabilities further leverage data through secure cloud solutions for OEE assessment and predictive maintenance. Data can be shared with external systems through Cloud or VPN connection.
KORSCH America will debut its X 5 Tablet Press at INTERPHEX NYC, April 16-18.