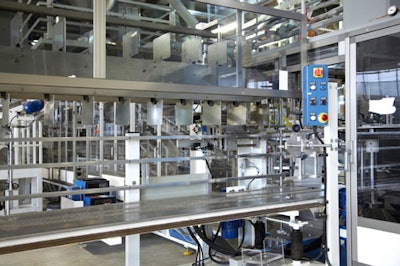
HCP: How does Allied Automation work with pharmaceutical firms?
JG: This is our 20th year at Allied. From our inception we've worked with companies such as Abbott, BD, Glaxo, and Johnson & Johnson. These companies use manufacturers for specific packaging equipment such as blister packaging, cartoning, shrink-banding, labeling, and so on. Allied typically integrates automation equipment within a company's packaging line. We could be inserting product into a blister-pack kit, say on a form fill seal machine, at their required line rate, and in a specific orientation. We may have to validate the presence of those components with a vision system that's typically integrated into the packaging line. We try to offer a solution that another packaging supplier may not provide. Maybe it's inspecting, or adding inserts or outserts, or installing a scanner for bar-code reading.
HCP: How is the pharmaceutical market unique from other industries that you serve?
JG: In consumer industries, packaging may emphasize shelf appeal and theft-deterrence if the customer is making an expensive component. For the pharmaceutical industry, that's not always a requirement. The pharmaceutical company is selling to hospitals or into medical distribution, so the packaging requirement may involve proper validation and tracking of lots. In case of a recall, we may need to track the medical information that goes into that product's packaging. Often, the equipment must meet cleanroom requirements.
HCP: So is Allied Automation selling machinery or services?
JG: We build machinery--anything from prototype and development equipment all the way through to fully automated assembly lines. Much of the equipment is proprietary and we can't really discuss specific applications. The equipment could be assembly systems, or test and inspection systems, or we could be retrofitting an existing cartoner to handle a new type of carton that is in the developmental stage. We could be adding labeling capacity to an existing type of cartoner. It's all of the technologies that you would find in typical automation that need to be applied to either an existing packaging system or something new that's coming out.
HCP: Yet I imagine you need to be sensitive to not be competitive with the primary equipment supplier.
JG: Certainly. We don't want to compete with a labeling company, let's say. We want to be offering something that is just not out there, where a customer has a need and they understand that they can get certain machine, but they need a unique, customized piece of equipment. That's what we can offer. Maybe they need to conduct a specific inspection and their space constraints are tight, so we would find a way to install a vision system or bar-code scanning device, and we would modify the controls to accomplish that task.
HCP: It seems like there are specific needs within the pharmaceutical community, be it for validation and regulatory issues, serialization, etc., correct?
JG: That's correct. Inspection requirements can be tough. If it's a vision system, the lighting always becomes a big factor. When you inspect the product, you have to guarantee that you can move the rejects from that inspection offline. And there is validation that has to be performed. That's usually tough to get through, but it beats performing these tasks manually.
HCP: One of the things that we run into is how companies interpret terms such as validation, qualification, etc. Do you have an answer for that?
JG: Validation, from Allied Automation's perspective, refers to a process of calibration and verification of the system itself (Does an inspection station meet the inspection requirements?) Qualification refers to verification of the validation process by checking the quality of the product made by the system. (Did a number of parts made on the system meet the standards required by manufacturing?)
HCP: There are so many pressures are on these pharmaceutical companies, and now they are being looked at to be sustainable and greener on top of that. Are you running into that much?
JG: Oh yes! With every piece of equipment, we are hearing about the carbon footprint, especially on medical device-type assembly systems. We are aware that when a syringe is used, and then thrown away it will leave a fairly sizeable carbon footprint. Now with the packaging, we have a little more flexibility in that you can start to consider plastics that can be recycled more easily. Companies are evaluating products or components that are green. In clean rooms, particulate is always an issue, so paper products are not typically acceptable.
HCP: We hear of medical devices being sterilized and reused again, but there are regulatory issues there, right?
JG: Absolutely! It seems that nobody really wants to get involved with sterilization. There are liability risks. People tend to want to start with a kit that's full of components, and when they are through using what they need, they throw the rest away. It's a tremendous waste with tremendous environmental impact.
HCP: Does this provide Allied Automation with increased kitting work?
JG: We don't do a tremendous amount of kitting. I would say more medical device assemblies that become an ingredient within a kit. Often we will assemble a device and transfer it by robot to a blister pack.
HCP: For years, we've heard that the pharmaceutical market has lagged behind food and beverage in terms of its packaging line efficiency and automation. But there are growing factors out there causing pharmaceutical firms to look at improving their efficiency and reduce costs. Do you agree with that?
JG: In pharmaceutical production, the equipment is often used beyond a typical deprecation period because of the validation hurdles required with the installation of new equipment. Older equipment usually equates to lower efficiency. For medical device assembly, I do agree that OEE (Overall Equipment Effectiveness) is often more difficult to achieve because there usually are more components to handle. This leads to more equipment jams and stoppages. Often we are required to handle a variety of different parts for different assemblies. With this flexibility, there usually is a lower OEE.
HCP: What key trends do you see with regard to pharmaceutical packaging that we should keep our eyes open for in the next year or two?
JG: One, I think there is going to be a tremendous green initiative. Recycling will become more important and the energy used to produce products will be reduced or renewable.
Another trend I envision is the mass expansion of foreign companies building medical products for the U.S. market. The FDA has been somewhat of a hurdle for this, however it is just a matter of time before most products are produced in countries like China.
Medical and pharmaceutical manufacturing has always been pretty much here to stay, and now this looks to be in jeopardy. I certainly am concerned about the possibility of all manufacturers being allowed to go overseas to produce drugs and devices.
-By Jim Butschli, Editor
JG: This is our 20th year at Allied. From our inception we've worked with companies such as Abbott, BD, Glaxo, and Johnson & Johnson. These companies use manufacturers for specific packaging equipment such as blister packaging, cartoning, shrink-banding, labeling, and so on. Allied typically integrates automation equipment within a company's packaging line. We could be inserting product into a blister-pack kit, say on a form fill seal machine, at their required line rate, and in a specific orientation. We may have to validate the presence of those components with a vision system that's typically integrated into the packaging line. We try to offer a solution that another packaging supplier may not provide. Maybe it's inspecting, or adding inserts or outserts, or installing a scanner for bar-code reading.
HCP: How is the pharmaceutical market unique from other industries that you serve?
JG: In consumer industries, packaging may emphasize shelf appeal and theft-deterrence if the customer is making an expensive component. For the pharmaceutical industry, that's not always a requirement. The pharmaceutical company is selling to hospitals or into medical distribution, so the packaging requirement may involve proper validation and tracking of lots. In case of a recall, we may need to track the medical information that goes into that product's packaging. Often, the equipment must meet cleanroom requirements.
HCP: So is Allied Automation selling machinery or services?
JG: We build machinery--anything from prototype and development equipment all the way through to fully automated assembly lines. Much of the equipment is proprietary and we can't really discuss specific applications. The equipment could be assembly systems, or test and inspection systems, or we could be retrofitting an existing cartoner to handle a new type of carton that is in the developmental stage. We could be adding labeling capacity to an existing type of cartoner. It's all of the technologies that you would find in typical automation that need to be applied to either an existing packaging system or something new that's coming out.
HCP: Yet I imagine you need to be sensitive to not be competitive with the primary equipment supplier.
JG: Certainly. We don't want to compete with a labeling company, let's say. We want to be offering something that is just not out there, where a customer has a need and they understand that they can get certain machine, but they need a unique, customized piece of equipment. That's what we can offer. Maybe they need to conduct a specific inspection and their space constraints are tight, so we would find a way to install a vision system or bar-code scanning device, and we would modify the controls to accomplish that task.
HCP: It seems like there are specific needs within the pharmaceutical community, be it for validation and regulatory issues, serialization, etc., correct?
JG: That's correct. Inspection requirements can be tough. If it's a vision system, the lighting always becomes a big factor. When you inspect the product, you have to guarantee that you can move the rejects from that inspection offline. And there is validation that has to be performed. That's usually tough to get through, but it beats performing these tasks manually.
HCP: One of the things that we run into is how companies interpret terms such as validation, qualification, etc. Do you have an answer for that?
JG: Validation, from Allied Automation's perspective, refers to a process of calibration and verification of the system itself (Does an inspection station meet the inspection requirements?) Qualification refers to verification of the validation process by checking the quality of the product made by the system. (Did a number of parts made on the system meet the standards required by manufacturing?)
HCP: There are so many pressures are on these pharmaceutical companies, and now they are being looked at to be sustainable and greener on top of that. Are you running into that much?
JG: Oh yes! With every piece of equipment, we are hearing about the carbon footprint, especially on medical device-type assembly systems. We are aware that when a syringe is used, and then thrown away it will leave a fairly sizeable carbon footprint. Now with the packaging, we have a little more flexibility in that you can start to consider plastics that can be recycled more easily. Companies are evaluating products or components that are green. In clean rooms, particulate is always an issue, so paper products are not typically acceptable.
HCP: We hear of medical devices being sterilized and reused again, but there are regulatory issues there, right?
JG: Absolutely! It seems that nobody really wants to get involved with sterilization. There are liability risks. People tend to want to start with a kit that's full of components, and when they are through using what they need, they throw the rest away. It's a tremendous waste with tremendous environmental impact.
HCP: Does this provide Allied Automation with increased kitting work?
JG: We don't do a tremendous amount of kitting. I would say more medical device assemblies that become an ingredient within a kit. Often we will assemble a device and transfer it by robot to a blister pack.
HCP: For years, we've heard that the pharmaceutical market has lagged behind food and beverage in terms of its packaging line efficiency and automation. But there are growing factors out there causing pharmaceutical firms to look at improving their efficiency and reduce costs. Do you agree with that?
JG: In pharmaceutical production, the equipment is often used beyond a typical deprecation period because of the validation hurdles required with the installation of new equipment. Older equipment usually equates to lower efficiency. For medical device assembly, I do agree that OEE (Overall Equipment Effectiveness) is often more difficult to achieve because there usually are more components to handle. This leads to more equipment jams and stoppages. Often we are required to handle a variety of different parts for different assemblies. With this flexibility, there usually is a lower OEE.
HCP: What key trends do you see with regard to pharmaceutical packaging that we should keep our eyes open for in the next year or two?
JG: One, I think there is going to be a tremendous green initiative. Recycling will become more important and the energy used to produce products will be reduced or renewable.
Another trend I envision is the mass expansion of foreign companies building medical products for the U.S. market. The FDA has been somewhat of a hurdle for this, however it is just a matter of time before most products are produced in countries like China.
Medical and pharmaceutical manufacturing has always been pretty much here to stay, and now this looks to be in jeopardy. I certainly am concerned about the possibility of all manufacturers being allowed to go overseas to produce drugs and devices.
-By Jim Butschli, Editor