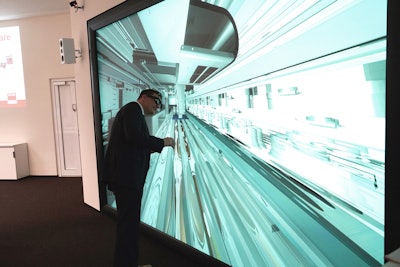
Coca-Cola and McDonald’s recent foray into retail packaging that consumers can fold into headsets or viewers might be considered “wicked cool,” but packaging equipment displayed in virtual reality also generates excitement by providing vivid color and animated views of machinery in action, often from angles and perspectives that creatively and clearly demonstrate how the equipment looks, runs, and often how easily it can be cleaned or changed over.
At recent packaging-centric trade shows, 3D imaging of equipment has wowed visitors. That was also the case at PACK EXPO/Pharma EXPO, where Optima Pharma and Optima Life Science unveiled turnkey projects as well as new and flexible machines using virtual reality via on-site simulations at its “VR-Box.”
For example, it displayed its MultiUse Filler virtually—a machine suited for everything from laboratory applications to fully automated processing of small batches, such as for biopharmaceutical medications. The system can process all types of nested syringe, vial and cartridge formats and is equipped with a transport system that processes large vial ranges at rates up to 150 products/min, without the need to change format parts. Its modular design gives end users flexibility for quick responses to all market and production demands.
Optima Life Science also virtually displayed its new OPTIMA TDC125 machine. This machine manufactures transdermal patches (TDS) and oral filmstrips (ODF) on a laboratory or small production scale. The scalable machine is suitable for manufacturing product samples for clinical tests, for market launch, as well as for subsequent production. In the simplest form the system operates intermittently. Alternatively, the system can be operated in a continuous mode with a high output in series production. Both intermittent- and the continuous-mode variants were shown in 3D.
Optima Pharma presented pharmaceutical turnkey projects in 3D using virtual reality, including large systems it has implemented for filling and sealing under an isolator. With turnkey projects Optima is building complete lines that include e-beam, filling, closing, isolator technology, freeze-drying, and secondary packaging.
Optima says, “Turnkey projects can be as big as a mid-sized family house. Here Virtual Reality can be a great help for discussions with the customer while project engineering is still going on. You can ‘zoom’ into the machine, walk through it and see all details before they are built in metal.”
The company says its first customer projects involve well-known international firms, though customer names or specifics cannot yet be divulged. Optima does note that early in 2016 companies and partners of Packaging Valley established the "Virtual Reality Center" in Germany’s Schwäbisch Hall, where life-sized visualization and 3D presentations enable greater efficiency in allocation of resources. In addition, virtual designs and mock-ups can be implemented quickly and cost effectively prior to prototype construction.—Jim Butschli