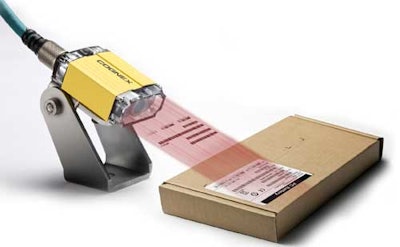
That's one message from this wide-ranging Q&A between Healthcare Packaging (HCP) and Cognex representatives Robb Robles (RR), product marketing manager, and Kris Bierbaum, pharmaceutical global accounts manager, discuss serialization and anti-counterfeiting from the global perspective of the maker of In-Sight® Track & Trace, an identification and data verification smart camera-based system just launched in the U.S. for healthcare serialization.
HCP: In-Sight Track & Trace was first introduced last year for pharmaceutical and medical device applications in Europe. Why was it initially made available in Europe?
RR: Europe had the most urgency—they are ahead of the U.S. in terms of putting requirements in place for labeling pharmaceutical packages, particularly prescription medicines.
HCP: What are some of those requirements?
RR: Every country is a little different. Basically three components are typically required for full, item-level traceability.
First is establishing standards for the kind of data to be tracked, and how it is to be presented. For example, the standards may state that the data must include batch information, lot information, expiration date, and a unique serial number. There are also formal guidelines for the order and presentation of the data, such as the maximum number of digits allowed in a data field, or where hyphens may appear.
GS1, a global organization that promotes supply chain data standards, is lobbying the FDA and other equivalent organizations around the world as well as pharmaceutical manufacturers to adopt a common global standard for this information.
The second requirement is for a data format that can be easily read and exchanged among all parties in the supply chain. Typically that format has been a 1D barcode, but that's changing to a 2D barcode--specifically, Data Matrix--because it can contain more information.
Third is the assignment of a unique serial number to each individual package, which enables traceability down to the item level, and will enable tracking of every item from the manufacturer all the way to the retail pharmacy.
Different countries require different combinations of these requirements. At some point, there will be a global standard, but it's being assembled by consensus, one country at a time. So there is a direction that everyone is pointing in—they are just going to get there at different times.
HCP: And that would help in the battle against counterfeiting and diversion, yes?
RR: Yes. Counterfeiting is a big problem in many parts of the world that threatens patient safety and ultimately the manufacturer's bottom line. Another problem is diversion, where products are being sold for unauthorized purposes or in geographies where the products are not authorized to be sold. Traceability enables pharmaceutical manufacturers, working together with enforcement agencies, to follow counterfeit medicines back to the source and to discover at which point in the supply chain the diversion occurred.
A common global data standard paired with item-level serialization will make it easier for manufacturers, packagers, distributors, pharmacists, and everyone involved in the supply chain to trace products back to their point of origin and authenticate them as legitimate. And also in the case of a product recall, it makes it easy and efficient to remove products, no matter where they are in the supply chain. This level of traceability is commonly referred to as e-Pedigree.
HCP: Why would you say that Europe is ahead of the United States, for example?
KB: One thing that is driving Europe's adoption is how they process medical reimbursements through their healthcare systems. Consumers submit documentation about the drugs they purchase to the country's healthcare agency, which then provides reimbursement. Turkey took a leading role in addressing fraud in the reimbursement process by mandating new drug traceability processes. These processes also help control the proliferation of counterfeit drugs. So the motivation to drive this forward in many countries was tied to management of fraud in the reimbursement process, as well as patient safety.
While EFPIA and other EU agencies are offering guidance on these processes, each country is driving the specific mandate and priorities. Germany, France, Turkey, and others that have either passed legislation or will pass legislation over the coming couple of years that will require a Data Matrix code encoded with the GS1 data standard. In particular, France has instituted a labeling requirement that the GTIN, expiration date, and lot information must be marked on every product, with a 2D Data Matrix bar code being selected as the preferred data carrier. January 2011 is the required date for compliance.
In the Americas, Brazil has taken the lead for protecting consumers and the supply chain. In January 2009, Brazil passed a law mandating that drug manufacturers and distributors act on specific serialization and track-and-trace requirements with a compliance deadline of January 2012. ETCO (http://www.etco.org.br/about-etco.php), a non-governmental organization focused on developing ethical business practices, was hired by the Brazilian equivalent of the FDA called ANVISA to set up a pilot study involving a group of pharmaceutical solution providers (including Cognex) to prove the feasibility of achieving the initiative.
HCP: And what about the U.S.?
RR: Right now California is the only state that has a compliance deadline for traceability. The California requirements are similar to Brazil in that they are pushing for full serialization, with a unique identifier on every individual package. Their deadline of 2015 gives companies more time to comply than most European countries have required.
However, the FDA just issued new guidelines for labeling on prescription drug packaging in March of this year. These guidelines recommend inclusion of an sNDC (Serialized National Drug Code) on each package. Previous guidelines had already put in place the NDC, so the significant difference here is the addition of a serial number, which will enable item-level traceability of prescription drugs for the first time in the United States. The sNDC is compatible with the GS1 data standard.
The guideline is not binding and has no compliance date attached, but generally companies don't deviate from FDA guidelines so I would expect this to increase efforts of U.S. manufacturers and packagers to establish infrastructure for traceability compliance.
HCP: Tell us a bit about In-Sight Track & Trace.
RR: In-Sight Track & Trace is a software package designed for Cognex In-Sight vision systems that makes it easy for manufacturers to set up a complete identification and data verification solution for labels on pharmaceutical or medical device packages. The fundamental capabilities are reading an ID code and verifying the accuracy of the printed text—for example, date/lot code information. If the label contains GS1 data, In-Sight Track & Trace can verify that the data is formatted correctly, and that it matches the printed text. Mismatched or incorrectly formatted data would indicate a process or database problem demanding immediate attention.
Another key capability of In-Sight Track & Trace is that it can assess the quality of the Data Matrix codes on 100% of the labels while the system is operating in production mode. This process check helps to make sure that the print quality hasn't degraded in a way that will cause readability issues downstream. Just because In-Sight can read a code, that doesn't mean that some other reader somewhere further along in the supply chain can read it. In-Sight Track & Trace can detect poor print quality very early on in the process, immediately after the label is actually printed or the carton is marked.
HCP: What does a manufacturer actually purchase?
RR: They will purchase an In-Sight vision system, along with the add-on Track & Trace software. There are many different In-Sight models available. Customers choose the In-Sight model that best meets their performance requirements and price requirements.
HCP: Where in the packaging line would a camera typically be placed?
RR: We are promoting it for anywhere on the packaging line—at the item level, carton level, case level, or at the pallet level. But the most strategic area for deployment is actually at the printing or marking station. If you are marking bad codes or poor quality text—or worst of all, printing the wrong information—you want to catch it immediately, before it has a chance to wreak havoc downstream in the supply chain.
HCP: Does In-Sight Track & Trace need a PC?
RR: A PC or PC-based HMI are often used to configure In-Sight Track & Trace, and are generally still necessary for storing production data and maintaining an audit trail. However, the mission-critical label identification and data verification processing occurs directly on the In-Sight smart camera itself, which runs independently of a PC. A key advantage of this approach is that In-Sight Track & Trace minimizes or even reduces the burden of having to install, validate, secure and maintain software on Windows-based PCs in pharmaceutical manufacturing and packaging areas.
HCP: Can the system be used on lines for both solids and liquids?
KB: It can be used for any pharmaceutical product that requires marking, typically at the unit-dose or item level. So you can use it for the back of a blister, or a vial label, or essentially wherever you can create a mark that needs to be read and verified.
The system serves as a building block, a self-contained module that's scalable. We find especially here in the U.S. that as people assess serialization options, they are starting out with something small and simple before moving to a broader-based application. The smart camera vision technology is scalable in that you can quickly and easily deploy it into new applications as your needs grow.
HCP: Can the system communicate with multiple production lines within a pharmaceutical facility?
RR: Yes, In-Sight vision systems support standard Ethernet TCP/IP protocols, which makes it easy for In-Sight Track & Trace to exchange data with any software system in the plant, such as serialization, quality and audit trail databases, as well as MES and ERP systems.
HCP: Will Cognex be marketing this to contract packagers?
KB: Absolutely. Since contract packers typically have lower margins and more cost pressures, a modular, lower cost system that can be readily adapted to their needs can provide benefits. Often, these companies are packaging products from multiple brand owners. This makes things even more complex because they have multiple systems requirements in which they have to comply. At the same time, they have multiple brand owners that they have to satisfy, and these brand owners may each have a different approach.
HCP: It's interesting that we are looking at an advanced technology for a pharmaceutical market that some consider lags behind other industries, such as food and beverage. Here it seems the pharmaceutical area is taking the lead. Would you agree?
KB: I think that the processes that have been implemented to protect consumers in the pharmaceutical market are very relevant in the food industry. Things like tracing the origin of food ingredients and managing the accuracy of labels and packaging materials are already being actively pursued using track-and-trace technologies. All it will take is an FDA recall due to packaging errors or an identified contamination issue to get the food and beverage industry to ramp up their initiatives in this area. So I think the food industry is going to be catching up in terms of their level of compliance.
HCP: Do food firms face the same level of counterfeiting and diversion concerns that pharmaceutical companies do?
KB: On the high end they do. Counterfeiting and diversion have been ongoing problems in high-value food areas such as wine and liquor for many years, as well as for tobacco products.
The pharmaceutical industry has typically not been techno-centric. In the past they installed a lot of expensive technology because they had to, without really understanding it well. What's happening now, I think, is that pharmaceutical companies are watching their money more carefully than they did 10 years ago and being more discriminating and informed about their technology investments.
HCP: In-Sight Track & Trace was first introduced last year for pharmaceutical and medical device applications in Europe. Why was it initially made available in Europe?
RR: Europe had the most urgency—they are ahead of the U.S. in terms of putting requirements in place for labeling pharmaceutical packages, particularly prescription medicines.
HCP: What are some of those requirements?
RR: Every country is a little different. Basically three components are typically required for full, item-level traceability.
First is establishing standards for the kind of data to be tracked, and how it is to be presented. For example, the standards may state that the data must include batch information, lot information, expiration date, and a unique serial number. There are also formal guidelines for the order and presentation of the data, such as the maximum number of digits allowed in a data field, or where hyphens may appear.
GS1, a global organization that promotes supply chain data standards, is lobbying the FDA and other equivalent organizations around the world as well as pharmaceutical manufacturers to adopt a common global standard for this information.
The second requirement is for a data format that can be easily read and exchanged among all parties in the supply chain. Typically that format has been a 1D barcode, but that's changing to a 2D barcode--specifically, Data Matrix--because it can contain more information.
Third is the assignment of a unique serial number to each individual package, which enables traceability down to the item level, and will enable tracking of every item from the manufacturer all the way to the retail pharmacy.
Different countries require different combinations of these requirements. At some point, there will be a global standard, but it's being assembled by consensus, one country at a time. So there is a direction that everyone is pointing in—they are just going to get there at different times.
HCP: And that would help in the battle against counterfeiting and diversion, yes?
RR: Yes. Counterfeiting is a big problem in many parts of the world that threatens patient safety and ultimately the manufacturer's bottom line. Another problem is diversion, where products are being sold for unauthorized purposes or in geographies where the products are not authorized to be sold. Traceability enables pharmaceutical manufacturers, working together with enforcement agencies, to follow counterfeit medicines back to the source and to discover at which point in the supply chain the diversion occurred.
A common global data standard paired with item-level serialization will make it easier for manufacturers, packagers, distributors, pharmacists, and everyone involved in the supply chain to trace products back to their point of origin and authenticate them as legitimate. And also in the case of a product recall, it makes it easy and efficient to remove products, no matter where they are in the supply chain. This level of traceability is commonly referred to as e-Pedigree.
HCP: Why would you say that Europe is ahead of the United States, for example?
KB: One thing that is driving Europe's adoption is how they process medical reimbursements through their healthcare systems. Consumers submit documentation about the drugs they purchase to the country's healthcare agency, which then provides reimbursement. Turkey took a leading role in addressing fraud in the reimbursement process by mandating new drug traceability processes. These processes also help control the proliferation of counterfeit drugs. So the motivation to drive this forward in many countries was tied to management of fraud in the reimbursement process, as well as patient safety.
While EFPIA and other EU agencies are offering guidance on these processes, each country is driving the specific mandate and priorities. Germany, France, Turkey, and others that have either passed legislation or will pass legislation over the coming couple of years that will require a Data Matrix code encoded with the GS1 data standard. In particular, France has instituted a labeling requirement that the GTIN, expiration date, and lot information must be marked on every product, with a 2D Data Matrix bar code being selected as the preferred data carrier. January 2011 is the required date for compliance.
In the Americas, Brazil has taken the lead for protecting consumers and the supply chain. In January 2009, Brazil passed a law mandating that drug manufacturers and distributors act on specific serialization and track-and-trace requirements with a compliance deadline of January 2012. ETCO (http://www.etco.org.br/about-etco.php), a non-governmental organization focused on developing ethical business practices, was hired by the Brazilian equivalent of the FDA called ANVISA to set up a pilot study involving a group of pharmaceutical solution providers (including Cognex) to prove the feasibility of achieving the initiative.
HCP: And what about the U.S.?
RR: Right now California is the only state that has a compliance deadline for traceability. The California requirements are similar to Brazil in that they are pushing for full serialization, with a unique identifier on every individual package. Their deadline of 2015 gives companies more time to comply than most European countries have required.
However, the FDA just issued new guidelines for labeling on prescription drug packaging in March of this year. These guidelines recommend inclusion of an sNDC (Serialized National Drug Code) on each package. Previous guidelines had already put in place the NDC, so the significant difference here is the addition of a serial number, which will enable item-level traceability of prescription drugs for the first time in the United States. The sNDC is compatible with the GS1 data standard.
The guideline is not binding and has no compliance date attached, but generally companies don't deviate from FDA guidelines so I would expect this to increase efforts of U.S. manufacturers and packagers to establish infrastructure for traceability compliance.
HCP: Tell us a bit about In-Sight Track & Trace.
RR: In-Sight Track & Trace is a software package designed for Cognex In-Sight vision systems that makes it easy for manufacturers to set up a complete identification and data verification solution for labels on pharmaceutical or medical device packages. The fundamental capabilities are reading an ID code and verifying the accuracy of the printed text—for example, date/lot code information. If the label contains GS1 data, In-Sight Track & Trace can verify that the data is formatted correctly, and that it matches the printed text. Mismatched or incorrectly formatted data would indicate a process or database problem demanding immediate attention.
Another key capability of In-Sight Track & Trace is that it can assess the quality of the Data Matrix codes on 100% of the labels while the system is operating in production mode. This process check helps to make sure that the print quality hasn't degraded in a way that will cause readability issues downstream. Just because In-Sight can read a code, that doesn't mean that some other reader somewhere further along in the supply chain can read it. In-Sight Track & Trace can detect poor print quality very early on in the process, immediately after the label is actually printed or the carton is marked.
HCP: What does a manufacturer actually purchase?
RR: They will purchase an In-Sight vision system, along with the add-on Track & Trace software. There are many different In-Sight models available. Customers choose the In-Sight model that best meets their performance requirements and price requirements.
HCP: Where in the packaging line would a camera typically be placed?
RR: We are promoting it for anywhere on the packaging line—at the item level, carton level, case level, or at the pallet level. But the most strategic area for deployment is actually at the printing or marking station. If you are marking bad codes or poor quality text—or worst of all, printing the wrong information—you want to catch it immediately, before it has a chance to wreak havoc downstream in the supply chain.
HCP: Does In-Sight Track & Trace need a PC?
RR: A PC or PC-based HMI are often used to configure In-Sight Track & Trace, and are generally still necessary for storing production data and maintaining an audit trail. However, the mission-critical label identification and data verification processing occurs directly on the In-Sight smart camera itself, which runs independently of a PC. A key advantage of this approach is that In-Sight Track & Trace minimizes or even reduces the burden of having to install, validate, secure and maintain software on Windows-based PCs in pharmaceutical manufacturing and packaging areas.
HCP: Can the system be used on lines for both solids and liquids?
KB: It can be used for any pharmaceutical product that requires marking, typically at the unit-dose or item level. So you can use it for the back of a blister, or a vial label, or essentially wherever you can create a mark that needs to be read and verified.
The system serves as a building block, a self-contained module that's scalable. We find especially here in the U.S. that as people assess serialization options, they are starting out with something small and simple before moving to a broader-based application. The smart camera vision technology is scalable in that you can quickly and easily deploy it into new applications as your needs grow.
HCP: Can the system communicate with multiple production lines within a pharmaceutical facility?
RR: Yes, In-Sight vision systems support standard Ethernet TCP/IP protocols, which makes it easy for In-Sight Track & Trace to exchange data with any software system in the plant, such as serialization, quality and audit trail databases, as well as MES and ERP systems.
HCP: Will Cognex be marketing this to contract packagers?
KB: Absolutely. Since contract packers typically have lower margins and more cost pressures, a modular, lower cost system that can be readily adapted to their needs can provide benefits. Often, these companies are packaging products from multiple brand owners. This makes things even more complex because they have multiple systems requirements in which they have to comply. At the same time, they have multiple brand owners that they have to satisfy, and these brand owners may each have a different approach.
HCP: It's interesting that we are looking at an advanced technology for a pharmaceutical market that some consider lags behind other industries, such as food and beverage. Here it seems the pharmaceutical area is taking the lead. Would you agree?
KB: I think that the processes that have been implemented to protect consumers in the pharmaceutical market are very relevant in the food industry. Things like tracing the origin of food ingredients and managing the accuracy of labels and packaging materials are already being actively pursued using track-and-trace technologies. All it will take is an FDA recall due to packaging errors or an identified contamination issue to get the food and beverage industry to ramp up their initiatives in this area. So I think the food industry is going to be catching up in terms of their level of compliance.
HCP: Do food firms face the same level of counterfeiting and diversion concerns that pharmaceutical companies do?
KB: On the high end they do. Counterfeiting and diversion have been ongoing problems in high-value food areas such as wine and liquor for many years, as well as for tobacco products.
The pharmaceutical industry has typically not been techno-centric. In the past they installed a lot of expensive technology because they had to, without really understanding it well. What's happening now, I think, is that pharmaceutical companies are watching their money more carefully than they did 10 years ago and being more discriminating and informed about their technology investments.