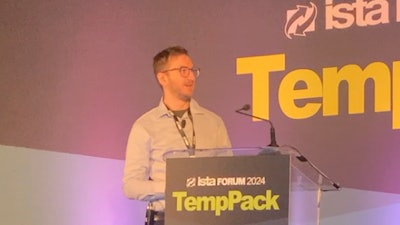
Gary Paul, packaging engineer at Kite Pharma, shared in his talk at ISTA's TempPack that the patient brings new variability into the process compared with traditional manufacturing because the starting material is the patient’s own cells.
Cell and gene therapy companies must schedule flexibility into their processes—on one hand, they need to be ready to produce when materials arrive, but on the other, something could happen prior to the patient's collection. In most cases, the patient receiving the drug is very sick and they may need to cancel, postpone, take care of family issues, etc.
On the packaging side of collection, he noted that companies need to strike a balance with shipper design. “You need to design a shipper that is effective, but also very easy, because you're working with nurses and doctors that do not typically deal with this package. They have their normal duties... and if this is something that they only do once a month, they're not going to have that muscle memory,” he said.
Liquid nitrogen dewars themselves have their own learning curve for cryogenic shipping. Paul added, "You want to make sure that you're not using any cleaning agents that could cause problems. We have seen some cleaning agents provide false readings of other substances when they go through customs."
Ultimately, you’ll need a good partnership and communication with your hospitals and treatment centers, along with a simple-yet-effective shipper. And as any packaging engineer knows, there's no one-size-fits-all. When you only have one chance, every step of the process must be tightly controlled. He reminded attendees, “Losing your starting materials means that you might not get a chance to treat that patient.”