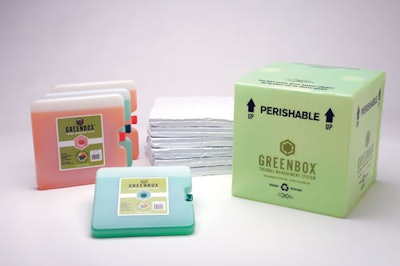
Entropy Solutions, Inc. was announced as the Diamond winner at the 22nd DuPont Awards for Packaging Innovation, DuPont Packaging & Industrial Polymers with its Greenbox temperature-sensitive shipper, developed to maintain and control the temperature of vaccines, blood, and biologic-based products during transit.
The Greenbox system includes a plastic, corrugated outer skin, Thermal-Lok hyper insulation panels, and PureTemp™ PCM (phase-change material) panels. The outer container is injection-molded of high-density polyethylene.
PureTemp is a patented, proprietary formulation of renewable plant-based phase-change materials used to maintain and control temperature. It can continually regulate the temperature of a product or structure using the surrounding ambient energy. PCMs are compounds that liquefy and solidify at specific temperatures. During the process of liquefying and solidifying within a set temperature range, PCMs absorb, store, and release large amounts of energy. These natural properties of latent heat energy help maintain a product's or structure's temperature and buffer it from temperature swings.
Entropy Solutions' President Eric Lindquist believes there are several mistakes companies make that lead to temperature-related product losses. They include:
• Product shipped in inferior thermal packaging, and the product is compromised. In the case of many vaccines, the product experiences a “thermal shock” after coming into direct contact with ice-based gel packs.
• Delays happen in transit. Lindquist says he has yet to see a figure for compromised product due to the recent volcano incident in Europe, however he believes it will be significant. Companies have a thermal shipper that may or may not be qualified, which then experiences delay—a missed connection, no available space, dry ice restrictions, etc.—so the product then goes out of acceptable temperature range.
• Mispacks. Most often the decision on how many packs to use is made by the packer at time of packing. If the product is packed in New Jersey in February, and is destined for Phoenix, the packer must decide whether to use an amount of gel packs that is right for New Jersey or an amount right for Phoenix.
• Improper equilibration. To avoid the “thermal shock syndrome” that is mentioned above, products that are prepared in a freezer—both water/ice-based gels and 5°C paraffins—need time to equilibrate before packing. This means that the coolants need to sit out between 15 to 30 minutes before they are to be packed.
The Greenbox system is touted as reusable. How frequently end-user companies reuse them varies by customer and is dependent on the mode by which they are transported.
How many times must they be reused to be economically advantageous compared with more common thermal shipping products? Lindquist points out, “The price range for qualified systems is from $18 [for a 24-hour version] to $380 [for a 72-hour version].” He advises users to look at the following factors:
• Cost per use: A typical validated “one-and-done” package with conventional components costs around $28, which is also cost per use. Packages using the advanced PCMs such as the Greenbox combined with durable carton materials cost around $109, but can be reused more than 50 times.
• Outbound freight cost: Because of the lower number of components in a package with advanced PCMs (specifically, the need not to insulate between the PCM and the payload), freight cost is lower.
• Packing time: Many traditional convection-based shipping systems have more than 18 packing steps and take approximately two minutes to pack. Greenbox systems use six steps and are packed in an average of 28 seconds.
• Warehouse expense: A characteristic of most conventional temperature-controlled packages is that many different dimensions are necessary to account for any change in mass or volume. Greenbox does not require a comparable variety of components and has smaller overall dimensions.
—Jim Butschli
The Greenbox system includes a plastic, corrugated outer skin, Thermal-Lok hyper insulation panels, and PureTemp™ PCM (phase-change material) panels. The outer container is injection-molded of high-density polyethylene.
PureTemp is a patented, proprietary formulation of renewable plant-based phase-change materials used to maintain and control temperature. It can continually regulate the temperature of a product or structure using the surrounding ambient energy. PCMs are compounds that liquefy and solidify at specific temperatures. During the process of liquefying and solidifying within a set temperature range, PCMs absorb, store, and release large amounts of energy. These natural properties of latent heat energy help maintain a product's or structure's temperature and buffer it from temperature swings.
Entropy Solutions' President Eric Lindquist believes there are several mistakes companies make that lead to temperature-related product losses. They include:
• Product shipped in inferior thermal packaging, and the product is compromised. In the case of many vaccines, the product experiences a “thermal shock” after coming into direct contact with ice-based gel packs.
• Delays happen in transit. Lindquist says he has yet to see a figure for compromised product due to the recent volcano incident in Europe, however he believes it will be significant. Companies have a thermal shipper that may or may not be qualified, which then experiences delay—a missed connection, no available space, dry ice restrictions, etc.—so the product then goes out of acceptable temperature range.
• Mispacks. Most often the decision on how many packs to use is made by the packer at time of packing. If the product is packed in New Jersey in February, and is destined for Phoenix, the packer must decide whether to use an amount of gel packs that is right for New Jersey or an amount right for Phoenix.
• Improper equilibration. To avoid the “thermal shock syndrome” that is mentioned above, products that are prepared in a freezer—both water/ice-based gels and 5°C paraffins—need time to equilibrate before packing. This means that the coolants need to sit out between 15 to 30 minutes before they are to be packed.
The Greenbox system is touted as reusable. How frequently end-user companies reuse them varies by customer and is dependent on the mode by which they are transported.
How many times must they be reused to be economically advantageous compared with more common thermal shipping products? Lindquist points out, “The price range for qualified systems is from $18 [for a 24-hour version] to $380 [for a 72-hour version].” He advises users to look at the following factors:
• Cost per use: A typical validated “one-and-done” package with conventional components costs around $28, which is also cost per use. Packages using the advanced PCMs such as the Greenbox combined with durable carton materials cost around $109, but can be reused more than 50 times.
• Outbound freight cost: Because of the lower number of components in a package with advanced PCMs (specifically, the need not to insulate between the PCM and the payload), freight cost is lower.
• Packing time: Many traditional convection-based shipping systems have more than 18 packing steps and take approximately two minutes to pack. Greenbox systems use six steps and are packed in an average of 28 seconds.
• Warehouse expense: A characteristic of most conventional temperature-controlled packages is that many different dimensions are necessary to account for any change in mass or volume. Greenbox does not require a comparable variety of components and has smaller overall dimensions.
—Jim Butschli
Companies in this article