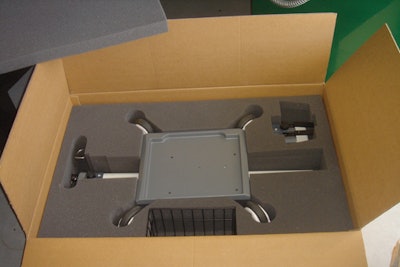
This task will provide all of the critical attributes and requirements for the device that could have an effect on the package design and performance. The design inputs will also influence the selection of materials appropriate for and compatible with the device.
In most cases, packages are intended to simply contain the product. However, for medical devices, there are other functions that the package serves; it provides protection, identification, processability, ease of use, and special applications for device use and presentation. A basic knowledge of the product's use, dimensions, shape, and special characteristics (e.g. sharp edges, points, fragility, etc.); distribution environment, application, and barrier requirements are essential to selecting appropriate materials and effectively designing the final package.
Protection of the device by the package may be provided in several different ways. Primarily, the sterile medical device must be protected from the bacteria and microorganisms natural to the environment. The package must provide a protective barrier from the environment but must also allow the product to be terminally sterilized and opened easily by medical professionals while also maintaining integrity until point of end use. Materials must allow for the most efficient and effective sterilization method but not be degraded by that method. The package must also protect the product from the environmental hazards that are common during distribution and handling. In addition, there cannot be any damage to the package itself from shock or impacts associated with handling in shipment, resulting in loss of seal integrity. This provision is covered under the FDA 21 CFR, Part 820.130 'Device packaging':
“Each manufacturer shall ensure that device packaging and shipping containers are designed and constructed to protect the device from alteration or damage during the customary conditions of processing, storage, handling, and distribution.”
In addition, for devices being marketed in the European Union, the Medical Device Directive (MDD Council Directive 93/42/EEC), Essential Requirements, must be met. It requires that: “Devices delivered in a sterile state must be designed, manufactured, and packed in a nonreusable pack and/or according to appropriate procedures to ensure that they are sterile when placed on the market and remain sterile, under the storage and transport conditions laid down, until the protective packaging is damaged or opened.”
Furthermore, materials must be resistant to impacts and abrasion. The package must be designed so as to prevent sharp objects from piercing the materials or damaging seals, which is often accomplished by eliminating movement of the device inside the package. In some applications, the product may be so fragile that the package must have cushioning characteristics that prevent excess shock energy to be transmitted to the device. Protection of the device over an extended shelf life is another function of the package design requiring material stability over time.
Summarizing the protective features a package for a sterile medical device must have:
• Sterilization: Provide the ability to terminally sterilize the device by one or more methods without degrading the material.
• Shelf Life: Ensure the stability of the material as a barrier throughout the life cycle of the product.
• Environmental: Barrier to moisture, air, bacteria, oxygen, light.
• Physical: Provide dynamic protection, resist impacts and abrasion, and offer structural support.
The materials most commonly used for medical device packages today incorporate the characteristics required for a protective package. So how do you ensure that the package will protect the product? Follow the six-step checklist below:
Step 1. Consult the regulations. The medical device manufacturer should consult with its regulatory department to ensure that the device falls under the requirements of any FDA or other international regulation for packaging.
Step 2. Gather packaging design requirements. The packaging engineer/designer must collaborate with the relevant project team members to create a packaging design requirements document.
Step 3. Establish packaging system conformity requirements. The goal of a protective packaging system is to ensure that the product reaches its end use in a usable and sterile condition. The package system must prevent any breach of the sterile barrier (for a sterile barrier package) and prevent damage to the medical device, which is not easily detectable and may impact the safe and effective use of the device.
Step 4. Investigate labeling requirements. General Labeling Provisions are minimum requirements for all devices. Medical device labeling is regulated by 21 CFR Part 801, which contains active subparts A, C, D, E and H. Subpart A -General Labeling Provisions, should be carefully reviewed for required compliance as well as the remaining subparts to determine if special compliance is indicated.
Step 5. Conduct distribution and handling tests. Today's increasingly complex medical devices require the package designer to perform a thorough investigation of the anticipated distribution, storage and handling conditions of their medical device. This is typically performed in a laboratory using published standards that simulate the distribution environment.
Step 6. Perform stability testing, accelerated and real-time aging of the sterile barrier system. For medical devices, the industry-recognized compliance standard, ISO 11607(1) and (2):2006 requires stability testing of the sterile barrier system. Manufacturers universally execute shelf-life studies to support product and package (sterility) expiration dating. The evaluation of age-related phenomena to whole package and seal integrity can be evaluated through the execution of whole package and seal integrity tests at specified time intervals throughout the accelerated aging and real-time aging protocols.
By Pat Nolan, COO of DDL. He has 27-plus years of experience in the testing and analysis of packaging and products for shock and vibration hazards inherent in the distribution system. Nolan serves the package testing industry as Chairman for the ASTM committee D-10 on Packaging and is also a member of the AAMI committee to draft a Technical Information Report (TIR), which identifies 11607 compliance regulation guidelines.
In most cases, packages are intended to simply contain the product. However, for medical devices, there are other functions that the package serves; it provides protection, identification, processability, ease of use, and special applications for device use and presentation. A basic knowledge of the product's use, dimensions, shape, and special characteristics (e.g. sharp edges, points, fragility, etc.); distribution environment, application, and barrier requirements are essential to selecting appropriate materials and effectively designing the final package.
Protection of the device by the package may be provided in several different ways. Primarily, the sterile medical device must be protected from the bacteria and microorganisms natural to the environment. The package must provide a protective barrier from the environment but must also allow the product to be terminally sterilized and opened easily by medical professionals while also maintaining integrity until point of end use. Materials must allow for the most efficient and effective sterilization method but not be degraded by that method. The package must also protect the product from the environmental hazards that are common during distribution and handling. In addition, there cannot be any damage to the package itself from shock or impacts associated with handling in shipment, resulting in loss of seal integrity. This provision is covered under the FDA 21 CFR, Part 820.130 'Device packaging':
“Each manufacturer shall ensure that device packaging and shipping containers are designed and constructed to protect the device from alteration or damage during the customary conditions of processing, storage, handling, and distribution.”
In addition, for devices being marketed in the European Union, the Medical Device Directive (MDD Council Directive 93/42/EEC), Essential Requirements, must be met. It requires that: “Devices delivered in a sterile state must be designed, manufactured, and packed in a nonreusable pack and/or according to appropriate procedures to ensure that they are sterile when placed on the market and remain sterile, under the storage and transport conditions laid down, until the protective packaging is damaged or opened.”
Furthermore, materials must be resistant to impacts and abrasion. The package must be designed so as to prevent sharp objects from piercing the materials or damaging seals, which is often accomplished by eliminating movement of the device inside the package. In some applications, the product may be so fragile that the package must have cushioning characteristics that prevent excess shock energy to be transmitted to the device. Protection of the device over an extended shelf life is another function of the package design requiring material stability over time.
Summarizing the protective features a package for a sterile medical device must have:
• Sterilization: Provide the ability to terminally sterilize the device by one or more methods without degrading the material.
• Shelf Life: Ensure the stability of the material as a barrier throughout the life cycle of the product.
• Environmental: Barrier to moisture, air, bacteria, oxygen, light.
• Physical: Provide dynamic protection, resist impacts and abrasion, and offer structural support.
The materials most commonly used for medical device packages today incorporate the characteristics required for a protective package. So how do you ensure that the package will protect the product? Follow the six-step checklist below:
Step 1. Consult the regulations. The medical device manufacturer should consult with its regulatory department to ensure that the device falls under the requirements of any FDA or other international regulation for packaging.
Step 2. Gather packaging design requirements. The packaging engineer/designer must collaborate with the relevant project team members to create a packaging design requirements document.
Step 3. Establish packaging system conformity requirements. The goal of a protective packaging system is to ensure that the product reaches its end use in a usable and sterile condition. The package system must prevent any breach of the sterile barrier (for a sterile barrier package) and prevent damage to the medical device, which is not easily detectable and may impact the safe and effective use of the device.
Step 4. Investigate labeling requirements. General Labeling Provisions are minimum requirements for all devices. Medical device labeling is regulated by 21 CFR Part 801, which contains active subparts A, C, D, E and H. Subpart A -General Labeling Provisions, should be carefully reviewed for required compliance as well as the remaining subparts to determine if special compliance is indicated.
Step 5. Conduct distribution and handling tests. Today's increasingly complex medical devices require the package designer to perform a thorough investigation of the anticipated distribution, storage and handling conditions of their medical device. This is typically performed in a laboratory using published standards that simulate the distribution environment.
Step 6. Perform stability testing, accelerated and real-time aging of the sterile barrier system. For medical devices, the industry-recognized compliance standard, ISO 11607(1) and (2):2006 requires stability testing of the sterile barrier system. Manufacturers universally execute shelf-life studies to support product and package (sterility) expiration dating. The evaluation of age-related phenomena to whole package and seal integrity can be evaluated through the execution of whole package and seal integrity tests at specified time intervals throughout the accelerated aging and real-time aging protocols.
By Pat Nolan, COO of DDL. He has 27-plus years of experience in the testing and analysis of packaging and products for shock and vibration hazards inherent in the distribution system. Nolan serves the package testing industry as Chairman for the ASTM committee D-10 on Packaging and is also a member of the AAMI committee to draft a Technical Information Report (TIR), which identifies 11607 compliance regulation guidelines.
Companies in this press-release