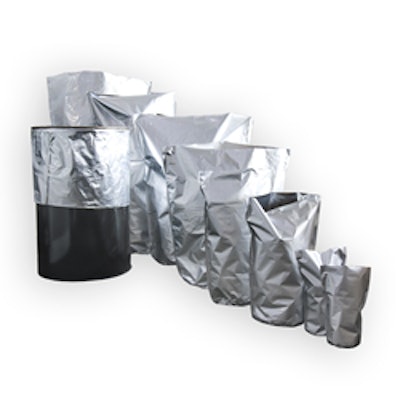
IMPAK’s protective drum liners are manufactured from high-barrier foil Mylar laminate and have a flat, round bottom that allows them to conform to the interior of drums and pails.
Polyethylene drum liners have long been used to protect drums, allowing processors to reuse the drum without downtime for cleaning, but they do little to protect the product itself. The Mylar-foil inserts from IMPAK are specifically made to dramatically increase shelf life while protecting contents from the degrading effects of water, moisture vapor, light and oxygen.
In addition to enhanced barrier properties and tensile strength, the majority of IMPAK’s drum liners are produced with a structure that can handle hot-fill and autoclave sterilization processes. This was a deciding factor for a multinational urethane producer looking to eliminate downtime for product cooling;
“Our product is produced at temps in excess of 250°F and can still be over 230°F when it hits the drum liner. It is critical to us that the integrity and purity of our product remain completely intact and unaffected by the innermost layer of the drum liner. IMPAK’s materials technology and understanding of our application ensured the success of this product,” says Michael N., Midwest Multinational Chemical Producer.
With available sizes ranging from 1 gal to 55 gal, these drum liners serve a range of applications from sensitive biological media to industrial chemicals and pharmaceutical intermediates, resins and more. The inner layer is an FDA-compliant food-safe material and the bags may be heat-sealed.
As a supplier of spout bags with highly specialized fitments, IMPAK can also custom produce round bottom drum liners with valves and fitments for liquid filling.