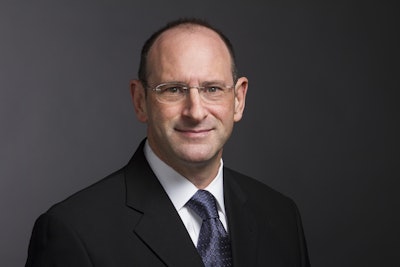
LAWS
In late May, the maker of a nasal spray product for treating allergies announced a recall of the products because, FDA reports, some containers of the product were “found to contain small glass particles.” The problem was discovered because of a customer complaint, but no adverse events or injuries had been reported.
In early July, FDA says, a different company announced a recall of pre-filled syringes of a drug used after some surgeries that might have the wrong labels (the strength of the product might be indicated incorrectly). This problem too was discovered because of a consumer complaint and again, no adverse events or injuries have been reported.
EFFECT
First things first: I have absolutely no idea what caused the issues for these specific companies. Reports like these appear in the news roughly every couple of weeks.
But these reports brought to mind two encounters I had in past years on the topic of quality and compliance by drug and device companies. One was a conversation with a consultant, and the other was a speech by an astronaut.
First, the consultant: There I was, many years ago, at the cocktail party affiliated with a Food and Drug Law industry conference, and I was chatting with a manufacturing consultant. Somehow the conversation came around to why there seemed lately to be more reports of drug and device quality problems necessitating recalls and market withdrawals. The consultant said he thought it was because of cost-cutting. Companies were cutting back on quality assurance steps and training in order to save money, he asserted, an that led to an uptick in product problems and, hence, recalls.
There’s a limit to how much a company’s quality-related activities can be cut back, because many are required by regulatory requirements, but this guy absolutely believed that a reduction in spending led to a reduction in dedication to quality which in turn had led to an increase in problems.
Now, before we go around pointing fingers at an entire industry, fair’s fair, this guy’s remark was what we call ‘anecdotal,’ meaning one person’s informal commentary rather than reliable data. In fact, it was worse than anecdotal because there was alcohol involved. Worse still because the guy was in the business of selling GMP compliance consulting services to drug and device companies, for gosh sakes.
Despite all that, I have always harbored the suspicion that this fellow was right that a loss of focus or emphasis on the GMP side, reflected in a reduction in budgets for example, sometimes does result in increased numbers of finished product quality problems. Assuring quality standards are maintained is hard to do on the cheap and requires a culture in which all involved employees understand and accept the importance of compliance, as well as, to borrow a phrase from the Harry Potter realm, “constant vigilance.” (That’s what Alastor "Mad-Eye Moody” tells Harry is needed to protect oneself against bad wizards. As you no doubt remember.)
Second, the astronaut: Mike Mullane, an experienced space shuttle astronaut, gives rather terrific speeches to corporate events, and several years ago I heard him. In discussing his view of the reasons for the Challenger disaster (remember the leaking o-rings), he went into a lengthy dissertation about lowering one’s own or one’s company’s standards of excellence or quality.
At one point he asked, “What happens the day you decide to lower your quality standards?”
After a dramatic pause, he gave the answer: “Nothing!” Nothing happens the day you decide to lower your standards, he observed, and that’s why you think it’s OK to keep them lowered. Only later, he argued, do the bad consequences show themselves.
I offer these two memories as a booster shot for everyone’s commitment to quality. There’s never a bad time for such a reminder.
INFORMATION ONLY. NOT LEGAL ADVICE.