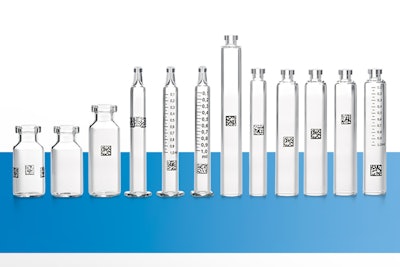
This content was written and submitted by the supplier. It has only been modified to comply with this publication’s space and style.
Health authorities and regulators are increasingly looking for much higher levels of traceability during the manufacture of parenteral medicines. The most common processes and technologies applied to achieve compliance are now reaching their technical limitations – so new approaches are needed to deliver the traceability requirements.
The International Society for Pharmaceutical Engineering (ISPE) recently published the Discussion Paper, “Unique Identification on Primary Containers to Drive Produce Traceability & Quality.” It is the outcome of a collaboration with a working group lead by the Stevanato Group, which includes pharmaceutical companies, contract manufacturing organizations (CMOs), fill & finish machine manufacturers, inspection machine producers, and a software company.
The document outlines the current implementation of unique container identification technology in parenteral manufacturing lines, including potential solutions, and a summary of the challenges technology developers face to develop and implement solutions within their operations.
Modern manufacturing operations in parenteral medicines are complex processes. Being able to trace each container within the process reduces risk and enables a detailed root cause analysis to improve each process.
Stevanato Group played a key role in drafting the document, leveraging its multi-year experience in the development of its novel container traceability solution that marks each primary container with a unique machine-readable 2D data matrix barcode. Each bulk or pre-sterilized glass syringe, cartridge, and vial aggregated in nested secondary packaging is given its own “fingerprint.” Thanks to Stevanato Group’s high-speed visual inspection machines, marked filled containers with defects can be immediately identified and segregated.
“Primary container serialization enables pharma companies to have unit-level traceability in the key steps of their manufacturing process, avoiding batch mix-ups before labeling and limiting batch segregation in the event of a problem, which often result in lost or missed revenue," says Fabio Bertacchini, product management director at Stevanato Group.
"With this document, Stevanato Group is leveling the playing field of primary serialization to facilitate its implementation by the industry. As many of the existing technologies are closed due to IP ownership, our goal is to create an open-source solution that could benefit all. To do that, we are working with multiple stakeholders to remove any possible barriers to entry and implement solutions that minimize any impact on existing processes," says Tod Urquhart, product manager and core team leader at Stevanato Group.