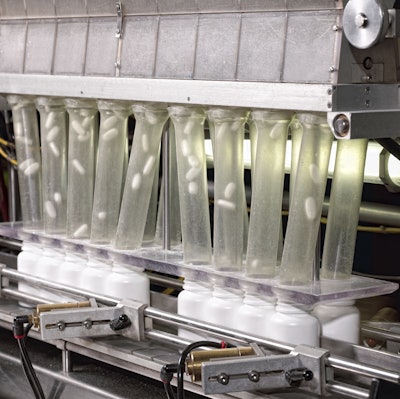
The pharmaceutical and biologics manufacturing industry is “a powerful river of good, doing the right thing, from CEOs to people on the manufacturing floor,” said Madhu Balachandran, Executive Vice President, Amgen, Inc., at the 2014 PDA/FDA Joint Regulatory Conference in Washington, DC.
In his presentation, “Perspectives on Biotech Manufacturing of the Future,” Balachandran stressed that while trying to attain our goals of quality manufacturing, we stumble because the challenges are many—and growing. They include the following:
• More patients globally
• Complex supply chains
• Market shifts
• Competition
• Cost pressures
• Changing regulatory landscape
Amgen is “making proteins so fragile,” he said. “As we try to ship these proteins around the world we are forced to use transport cold chains that may not be well established or very dependable.”
Defense in depth
The supply chain is stressed, not only for APIs, excipients, and finished drugs, but also for components of increasingly complex devises to help patients and healthcare workers adhere to medication routines. These delivery devices are complex to design (behind the scenes), to make it far more simple and convenient to administer the medications.
Controlling the supply chain for tiny electrical motors and injection-molded components is becoming hugely important.
“There are three important things to remember [about making drugs],” he said. “Quality is first and the other two are not important!” he joked.
Amgen is taking a systematic approach to delivering consistent results in a highly risk-laden environment, and it is looking at the U.S. Navy’s nuclear fleet for inspiration:
• 160,000,000 miles
• 100 nuclear reactors on any given day
• 50 years accident-free
“A truly remarkable achievement,” said Balachandran.
And the process the Navy uses is applicable regardless of business, and regardless of industry.
The process procedures the Navy writes are clear, correct and complete, and written with the operator in mind.
Processes are so well characterized that you can operate well within validated parameters.
Training of people is constant, formal, and routine.
Where Amgen has applied this “defense in depth” strategy, they have seen an immediate and dramatic drop in errors, and a dramatic increase in quality manufacturing
Amgen calls it Next-Gen manufacturing and has recently completed a plant in Singapore. One focus is the use of disposable, single-use processing components. This eliminates the need for cleaning and sterilization, and all the validation that goes with it.
Another focus is scaling down the size of the plant and increasing the efficiency of the process and concentrating on greater yields in biologic production.
The Next-Gen facility in Singapore proves the concept, reducing capital investments and cost per gram, and enabling deferral of major capital decisions.
Another element is on-line analytics so precise that you can eliminate as much as 80% of testing.
These Next-Gen plants will employ smaller pieces of equipment, take three years to build versus five, and require 1/3 the staff. Amgen plans to engineer more of these plants, providing backup manufacturing facilities around the globe.
Scale-up issues will be minimized with pilot, clinical, and commercial plants all one size.
The process is simple, robust, and sustainable, with fewer things to go wrong,” according to Balachandran.
The amount of testing we do before we release a drug is astonishingly large, he said. A goal of the process performance is to eliminate most testing where the drug is removed from the floor.
Balachandran told the audience that with one Amgen drug, Enbral, both Health Canada and the U.S. FDA have accepted 80% less testing.